The furnace atmosphere in thermal analysis significantly impacts the outcomes of heat treatment processes. It serves two primary roles: as a chemically reactive medium, it facilitates surface modifications like hardening by enabling reactions with the material's surface. Conversely, as a protective medium, it prevents harmful chemical reactions, such as oxidation or decarburization, thereby preserving the material's integrity. The choice of atmosphere—whether inert gases like argon or reactive gases like hydrogen—depends on the desired outcome, ensuring that the material's properties are optimized for its intended application. Proper control of the furnace atmosphere is essential to avoid unwanted reactions and achieve consistent, high-quality results.
Key Points Explained:
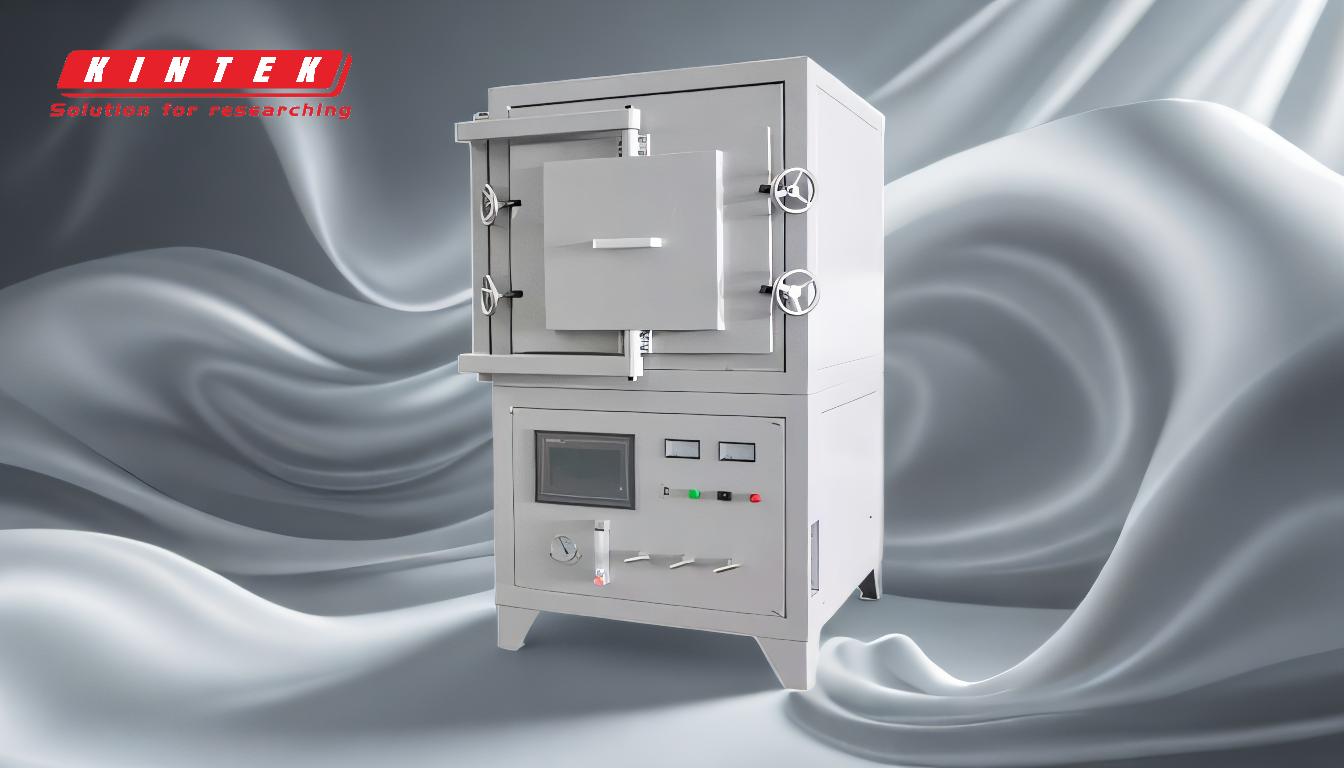
-
Role of Furnace Atmosphere in Thermal Analysis
- The furnace atmosphere is critical in determining the chemical and physical changes that occur during thermal processes.
- It can either promote or inhibit surface reactions, depending on the desired outcome.
- For example, in processes like hardening, reactive gases such as hydrogen or carbon monoxide are used to enhance surface characteristics.
- In contrast, inert gases like argon or nitrogen are used to protect materials from oxidation or other harmful reactions.
-
Chemically Reactive vs. Protective Atmospheres
- Reactive Atmospheres: These enable surface modifications by facilitating chemical reactions. For instance, carbon-rich atmospheres are used in carburizing processes to increase surface hardness.
- Protective Atmospheres: These prevent unwanted reactions, such as oxidation or decarburization, by creating an inert environment. This is crucial for maintaining the material's structural integrity and surface quality.
-
Common Gases Used in Furnace Atmospheres
- Inert Gases: Argon and nitrogen are commonly used to create a non-reactive environment, protecting materials from oxidation and other surface degradation.
- Reactive Gases: Hydrogen, carbon monoxide, and methane are used to promote specific surface reactions, such as hardening or carburizing.
- Mixed Gases: Some processes require a combination of gases to achieve both protective and reactive effects, such as in sintering processes where oxidation and decarburization must be controlled simultaneously.
-
Impact on Material Properties
- The furnace atmosphere directly influences the material's surface and bulk properties.
- For example, in sintering, the atmosphere ensures proper bonding of powdered metals by controlling oxidation and decarburization.
- In heat treatment, the atmosphere can alter hardness, toughness, and corrosion resistance, depending on the gases used.
-
Control of Furnace Atmosphere
- Precise regulation of the furnace atmosphere is essential to achieve consistent results.
- This involves selecting the appropriate gas mixture, maintaining the correct gas flow rates, and monitoring the atmosphere's composition throughout the process.
- Failure to control the atmosphere can lead to defects such as surface scaling, decarburization, or incomplete sintering, rendering the material unsuitable for its intended use.
-
Applications in Different Thermal Processes
- Heat Treatment: The atmosphere is tailored to support processes like annealing, hardening, and tempering, ensuring the desired mechanical properties are achieved.
- Sintering: The atmosphere is regulated to control sintering vectors, ensuring proper bonding and preventing defects in powdered metal components.
- Brazing and Soldering: The atmosphere prevents oxidation and ensures strong, clean joints between materials.
In summary, the furnace atmosphere is a critical factor in thermal analysis, influencing the chemical and physical properties of materials. By carefully selecting and controlling the atmosphere, manufacturers can achieve precise outcomes, whether enhancing surface characteristics or protecting materials from degradation. Proper understanding and management of furnace atmospheres are essential for optimizing thermal processes and ensuring high-quality results.
Summary Table:
Aspect | Details |
---|---|
Role of Atmosphere | Determines chemical/physical changes; promotes or inhibits surface reactions. |
Reactive Atmospheres | Enable surface modifications (e.g., hardening, carburizing). |
Protective Atmospheres | Prevent oxidation, decarburization; preserve material integrity. |
Common Gases | Inert (argon, nitrogen); Reactive (hydrogen, carbon monoxide, methane). |
Impact on Properties | Influences hardness, toughness, corrosion resistance, and bonding quality. |
Control Requirements | Precise gas selection, flow rates, and monitoring for consistent results. |
Applications | Heat treatment, sintering, brazing, and soldering. |
Ready to optimize your thermal processes? Contact our experts today for tailored furnace atmosphere solutions!