The efficiency of a rotary furnace is a critical factor in its operation, particularly in industries where energy consumption and thermal performance are significant concerns. Rotary furnaces are widely used for processes like melting, pyrolysis, and material treatment, but their efficiency is generally low, ranging from 23% to 27.5%. This low efficiency is primarily due to significant heat loss through exhaust gases, which can reach temperatures between 1100°C and 1315°C. However, advancements in mixing and conveying technologies, such as the use of Archimedes' screw spirals, have improved volume utilization and heat transfer, enhancing overall efficiency. Additionally, factors like furnace temperature, residence time, and pressure control play a crucial role in optimizing performance. Combining rotary furnaces with heat-exchange equipment is an emerging trend that further improves efficiency and reduces operational costs.
Key Points Explained:
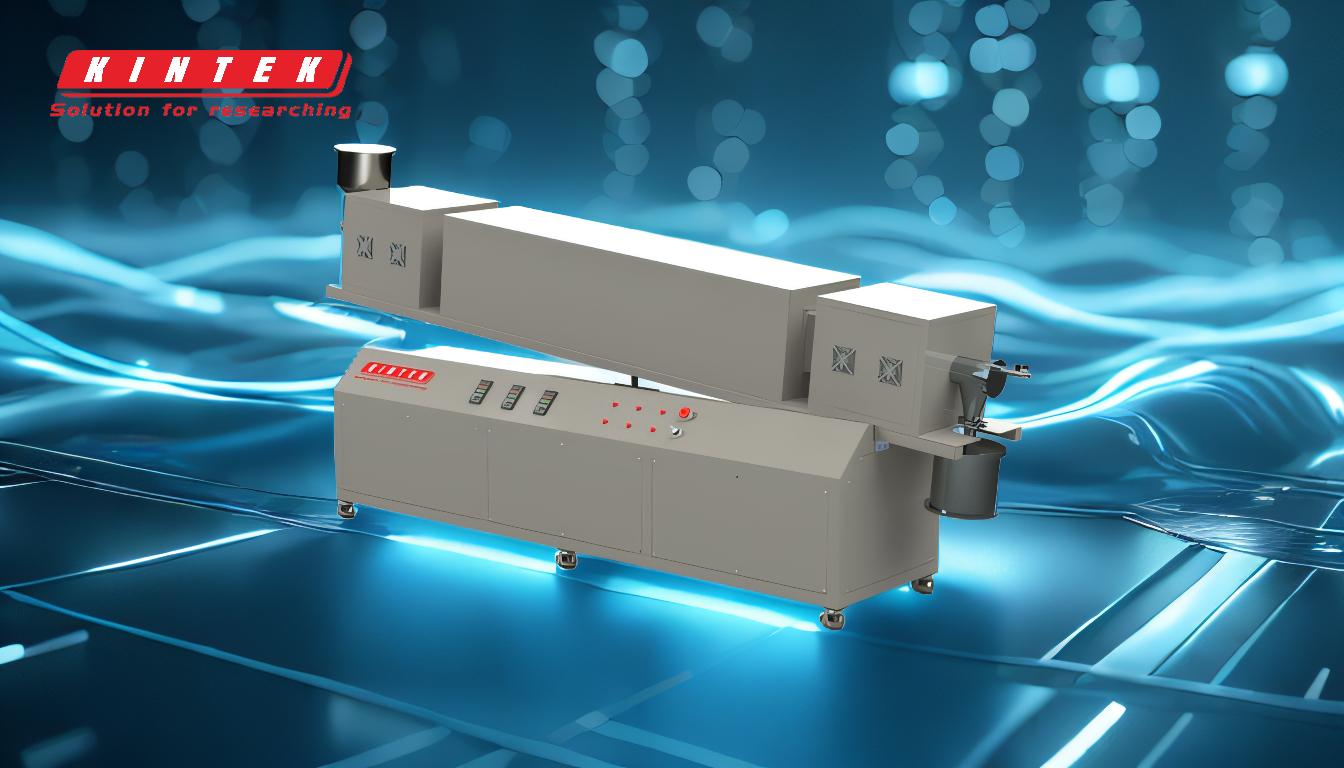
-
Thermal Efficiency of Rotary Furnaces:
- Rotary furnaces typically have a thermal efficiency of 23% to 27.5%, which is relatively low compared to other industrial equipment.
- A significant portion of the heat (50-70%) is lost through exhaust gases, which exit the furnace at high temperatures (1100-1315°C).
- This heat loss is a major contributor to the low overall efficiency of rotary furnaces.
-
Factors Affecting Efficiency:
- Furnace Temperature: The operating temperature of the furnace directly impacts the efficiency. Higher temperatures can improve reaction rates but may also increase heat loss.
- Residence Time: The duration that materials spend inside the furnace affects the completeness of the reactions. Proper control of residence time ensures optimal heat transfer and reaction efficiency.
- Pressure: Internal pressure conditions influence the behavior of gases and materials within the furnace, affecting heat distribution and reaction kinetics.
-
Technological Advancements:
- Mixing Technologies: Innovations like Archimedes' screw spirals enhance mixing, reducing the time required for heat and mass transfer-limited reactions. This improves volume utilization and overall efficiency.
- Heat-Exchange Integration: Combining rotary furnaces with heat-exchange equipment allows for the recovery of waste heat, increasing efficiency and reducing energy consumption.
-
Operational and Maintenance Considerations:
- Proper operation and maintenance are essential for maintaining efficiency. Regular maintenance ensures that the furnace operates at optimal conditions, minimizing energy waste and prolonging equipment life.
- Monitoring and controlling key parameters like temperature, residence time, and pressure are critical for achieving high efficiency.
-
Advantages and Disadvantages:
- Advantages: Rotary furnaces can process low-grade scrap and dross that are challenging for other types of furnaces. This makes them versatile for various industrial applications.
- Disadvantages: They are generally less efficient, require higher maintenance, and produce significant amounts of hazardous waste (salt cake), which must be properly disposed of.
-
Emerging Trends:
- There is a growing trend toward integrating rotary furnaces with advanced heat-exchange systems. This combination enhances efficiency, reduces operational costs, and allows for more compact furnace designs.
By addressing these key points, operators can better understand the factors influencing the efficiency of rotary furnaces and implement strategies to optimize their performance.
Summary Table:
Key Aspect | Details |
---|---|
Thermal Efficiency | 23% to 27.5%, with 50-70% heat loss through exhaust gases (1100-1315°C). |
Factors Affecting Efficiency | - Furnace temperature |
- Residence time
- Pressure control | | Technological Advancements | - Archimedes' screw spirals
- Heat-exchange integration for waste heat recovery | | Advantages | Processes low-grade scrap and dross, versatile for industrial applications. | | Disadvantages | Lower efficiency, higher maintenance, and hazardous waste production. | | Emerging Trends | Integration with heat-exchange systems for improved efficiency and cost savings. |
Optimize your rotary furnace performance today—contact our experts for tailored solutions!