A chamber furnace, often referred to as a sintering furnace, is a specialized piece of equipment designed to heat materials to high temperatures in a controlled environment. Its primary function is to sinter materials, which involves heating them to a temperature below their melting point to fuse particles together, reducing porosity and increasing density. This process is crucial in various industries, including ceramics, metallurgy, and dentistry, where it is used to create durable and high-performance components. The furnace operates by creating a vacuum or controlled atmosphere to prevent oxidation and contamination, ensuring the quality and integrity of the sintered products.
Key Points Explained:
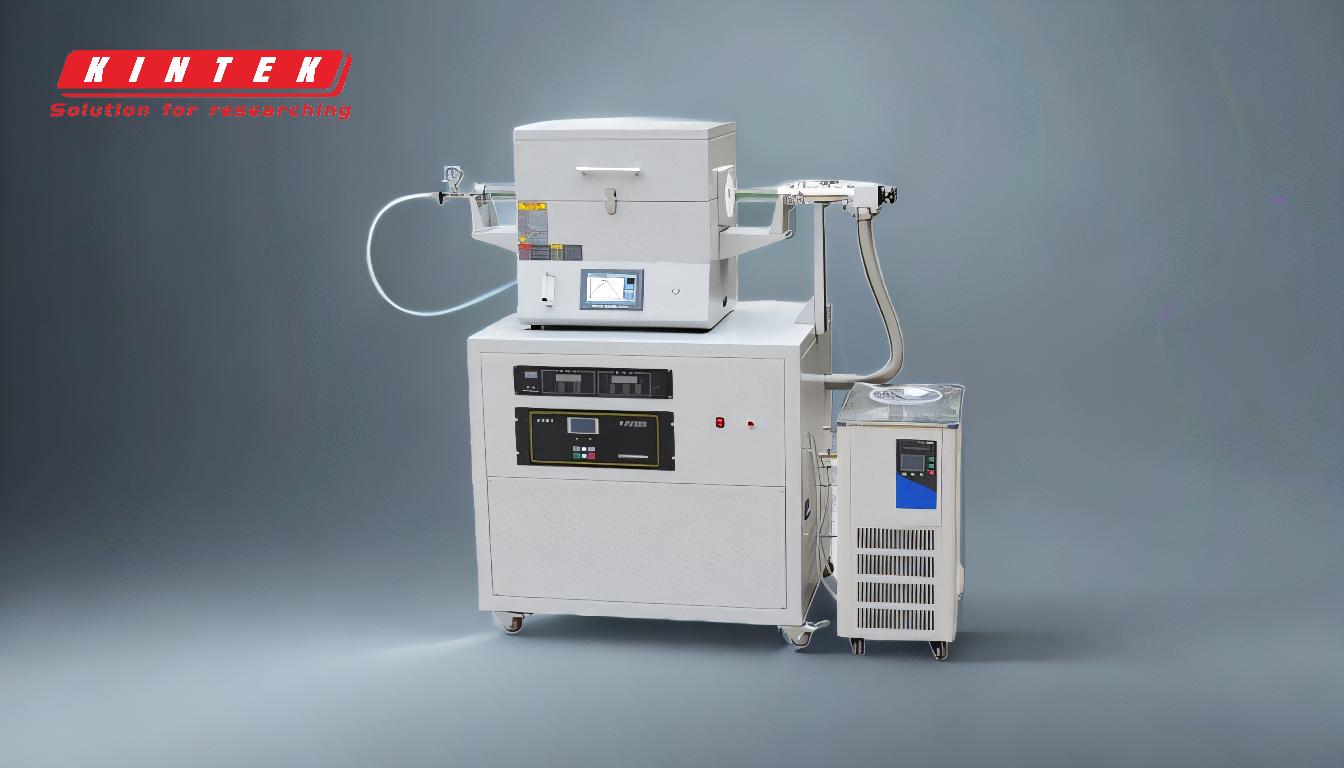
-
Primary Function of a Chamber Furnace:
- The main purpose of a chamber furnace is to sinter materials, which involves heating them to high temperatures below their melting point. This process fuses particles together, reducing porosity and increasing the material's density and strength. This is particularly important in industries like ceramics and metallurgy, where the final product's durability and performance are critical.
-
Applications in Various Industries:
- Dentistry: In the dental industry, chamber furnaces are used to sinter zirconia restorations such as crowns, bridges, and frameworks. The high temperatures achieved in the furnace allow zirconia to reach its final hardness, ensuring the restorations are strong and durable.
- Metallurgy: Chamber furnaces are used to heat treat metals, increasing their durability and hardness. This process enhances the metal's ability to withstand deformation and energy absorption before cracking.
- Ceramics: In the ceramics industry, chamber furnaces are used to sinter ceramic powders, transforming them into solid, high-density materials. This is essential for producing components with precise mechanical and thermal properties.
-
Vacuum and Controlled Atmosphere:
- Chamber furnaces often operate in a vacuum or controlled atmosphere to prevent oxidation and contamination. This is crucial for maintaining the quality and integrity of the sintered materials. The vacuum environment also aids in heat transfer and other surface treatments, such as ion-nitriding and carburization.
-
Components and Operation:
- A typical chamber furnace consists of several key components, including the furnace body, heater, pressure system, and vacuum system. The operation involves loading the material into the furnace, evacuating the air to create a vacuum, heating the material to the required temperature, and then cooling it down. This controlled process ensures consistent and high-quality results.
-
Benefits of Using a Chamber Furnace:
- Improved Material Properties: Sintering in a chamber furnace results in materials with reduced porosity and increased density, leading to better mechanical and thermal properties.
- Controlled Environment: The ability to control the atmosphere within the furnace prevents oxidation and contamination, ensuring the final product's quality.
- Versatility: Chamber furnaces can be used for a wide range of materials and applications, making them a versatile tool in various industries.
-
Comparison with Other Furnaces:
- Unlike tempering furnaces, which are designed to heat treat metals to increase their hardness and durability, chamber furnaces focus on sintering materials to improve their density and strength. Additionally, chamber furnaces often operate in a vacuum or controlled atmosphere, which is not typically the case with tempering furnaces.
In summary, a chamber furnace, or sintering furnace, is an essential piece of equipment in various industries, providing the high temperatures and controlled environments needed to sinter materials effectively. Its ability to improve material properties and ensure product quality makes it a valuable tool in the production of durable and high-performance components.
Summary Table:
Key Aspect | Details |
---|---|
Primary Function | Sinter materials to fuse particles, reduce porosity, and increase density. |
Applications | Dentistry (zirconia restorations), Metallurgy (heat treatment), Ceramics. |
Operating Environment | Vacuum or controlled atmosphere to prevent oxidation and contamination. |
Key Benefits | Improved material properties, controlled environment, and versatility. |
Comparison with Other Furnaces | Focuses on sintering, not tempering, often operates in a vacuum. |
Ready to enhance your material processing? Contact us today to learn more about chamber furnaces!