An electric muffle furnace is a versatile and essential piece of equipment used in laboratories, industrial settings, and research facilities. Its primary function is to provide high-temperature heating in a controlled environment, making it suitable for a wide range of applications. These include determining moisture, ash, volatile matter, and melting points, as well as conducting elemental analysis, ashing, sintering, heat treatment, and material testing. The muffle furnace is particularly useful in industries such as food, pharmaceuticals, environmental analysis, and materials science, where precise and consistent high-temperature processing is required.
Key Points Explained:
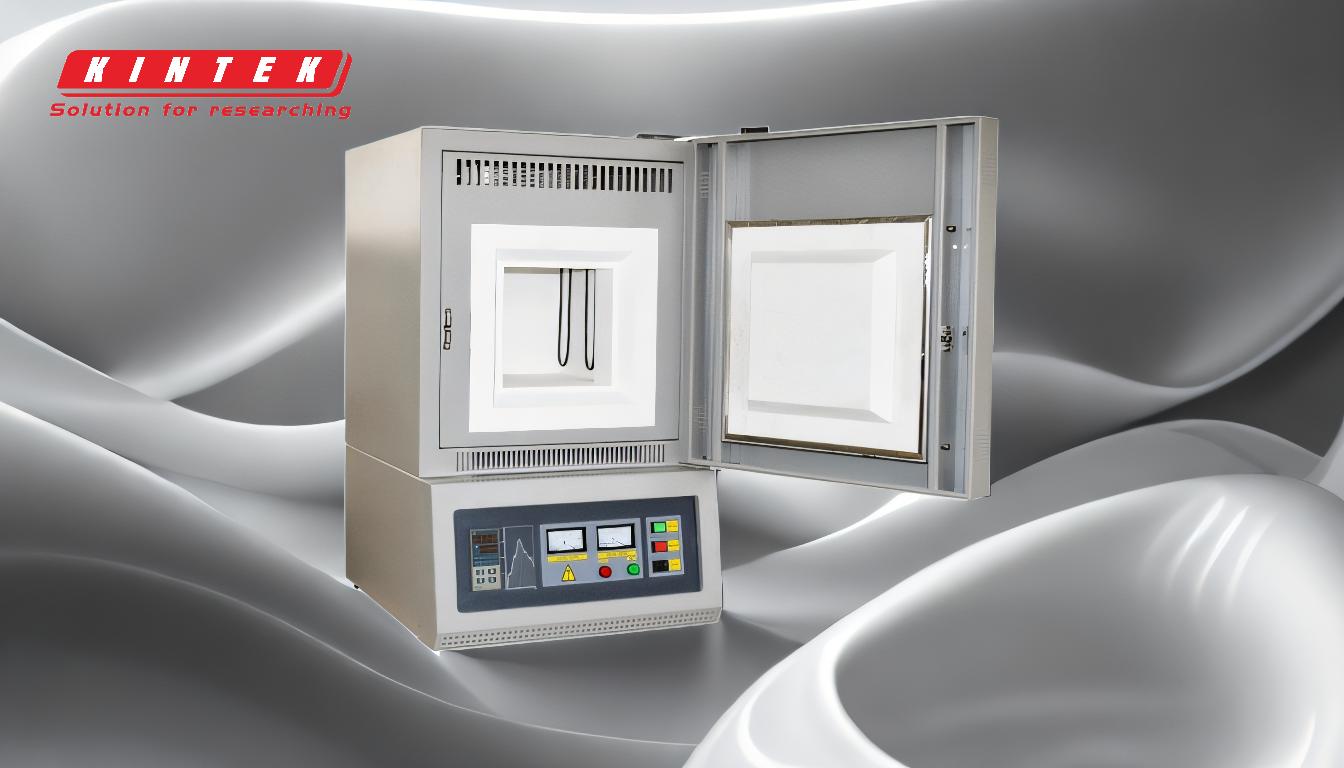
-
High-Temperature Heating and Controlled Environment:
- The muffle furnace is designed to reach and maintain high temperatures, often up to 1200°C or higher, depending on the model.
- It provides a controlled atmosphere, typically in an air environment, which is crucial for processes like ashing, sintering, and heat treatment.
- This controlled environment ensures consistent results and prevents contamination of samples.
-
Ashing and Combustion Analysis:
- One of the primary functions of a muffle furnace is to determine the ash content of materials, such as fuels, food, and pharmaceuticals.
- The furnace burns off organic matter, leaving behind inorganic residues (ash), which can then be analyzed for composition and properties.
- This is particularly important in industries like food testing, where ash content is a key quality parameter.
-
Heat Treatment Processes:
- Muffle furnaces are widely used for heat treatment processes such as annealing, quenching, tempering, and normalizing.
- These processes are essential for altering the mechanical properties of materials, such as metals and alloys, to improve hardness, strength, or ductility.
- The furnace's ability to maintain precise temperatures ensures uniform treatment of materials.
-
Elemental and Composition Analysis:
- The furnace is used in elemental analysis to determine the chemical composition of materials.
- It is also used for melting point analysis, ash composition analysis, and thermogravimetric analysis (TGA), where weight changes in a sample are measured as a function of temperature.
- These analyses are critical in research and quality control across various industries.
-
Sintering and Material Synthesis:
- Muffle furnaces are used for sintering, a process that involves heating powdered materials to a temperature below their melting point to form a solid mass.
- This is commonly used in the production of ceramics, metals, and composite materials.
- The furnace's uniform heating ensures the integrity and strength of the sintered products.
-
Applications in Specific Industries:
- Food Industry: Used for moisture and ash content determination, ensuring product quality and compliance with regulations.
- Pharmaceuticals: Employed for drug testing, sample pretreatment, and determining non-combustible content.
- Environmental Analysis: Used in water quality analysis, soil testing, and pollution studies.
- Materials Science: Essential for research and development of new materials, including ceramics, glass, and coatings.
-
Versatility and General-Purpose Use:
- Beyond specific applications, muffle furnaces are often used as general-purpose ashing furnaces in various fields.
- They are suitable for a wide range of high-temperature processes, including calcination, loss on ignition analysis, and brazing.
- Their versatility makes them indispensable in laboratories and industrial settings.
-
Research and Quality Control:
- Muffle furnaces play a crucial role in research facilities for studying material properties at high temperatures.
- They are also used in quality control processes to ensure that products meet specific standards and specifications.
- Applications include nuclear fuel disposal, technical ceramics production, and soldering.
In summary, the electric muffle furnace is a multifunctional tool that serves as a cornerstone in high-temperature processing and analysis. Its ability to provide precise and controlled heating makes it invaluable across a wide range of applications, from industrial manufacturing to scientific research. Whether used for ashing, sintering, heat treatment, or elemental analysis, the muffle furnace ensures accurate and reliable results, making it an essential piece of equipment in many fields.
Summary Table:
Application | Description |
---|---|
High-Temperature Heating | Reaches up to 1200°C+ for precise, controlled heating in air environments. |
Ashing & Combustion | Determines ash content in food, fuels, and pharmaceuticals. |
Heat Treatment | Used for annealing, quenching, tempering, and normalizing metals and alloys. |
Elemental Analysis | Conducts melting point, ash composition, and thermogravimetric analysis (TGA). |
Sintering & Synthesis | Forms solid masses from powdered materials for ceramics, metals, and composites. |
Industry Applications | Food, pharmaceuticals, environmental analysis, and materials science. |
Research & Quality Control | Ensures product standards and studies material properties at high temperatures. |
Ready to enhance your lab or industrial processes? Contact us today to find the perfect muffle furnace for your needs!