A rotary kiln is a versatile industrial heating furnace designed to process materials at high temperatures in a controlled environment. It functions as a heat exchanger, dryer, calcinator, and incinerator, enabling a wide range of thermal processes such as calcination, sintering, thermal desorption, and incineration. The kiln operates by rotating a slightly inclined cylindrical vessel, allowing materials to move from the upper to the lower end while being heated uniformly. This equipment is widely used in industries like cement production, where it calcines limestone to produce raw concrete, as well as in processes involving chemical transformations, organic combustion, and material phase changes.
Key Points Explained:
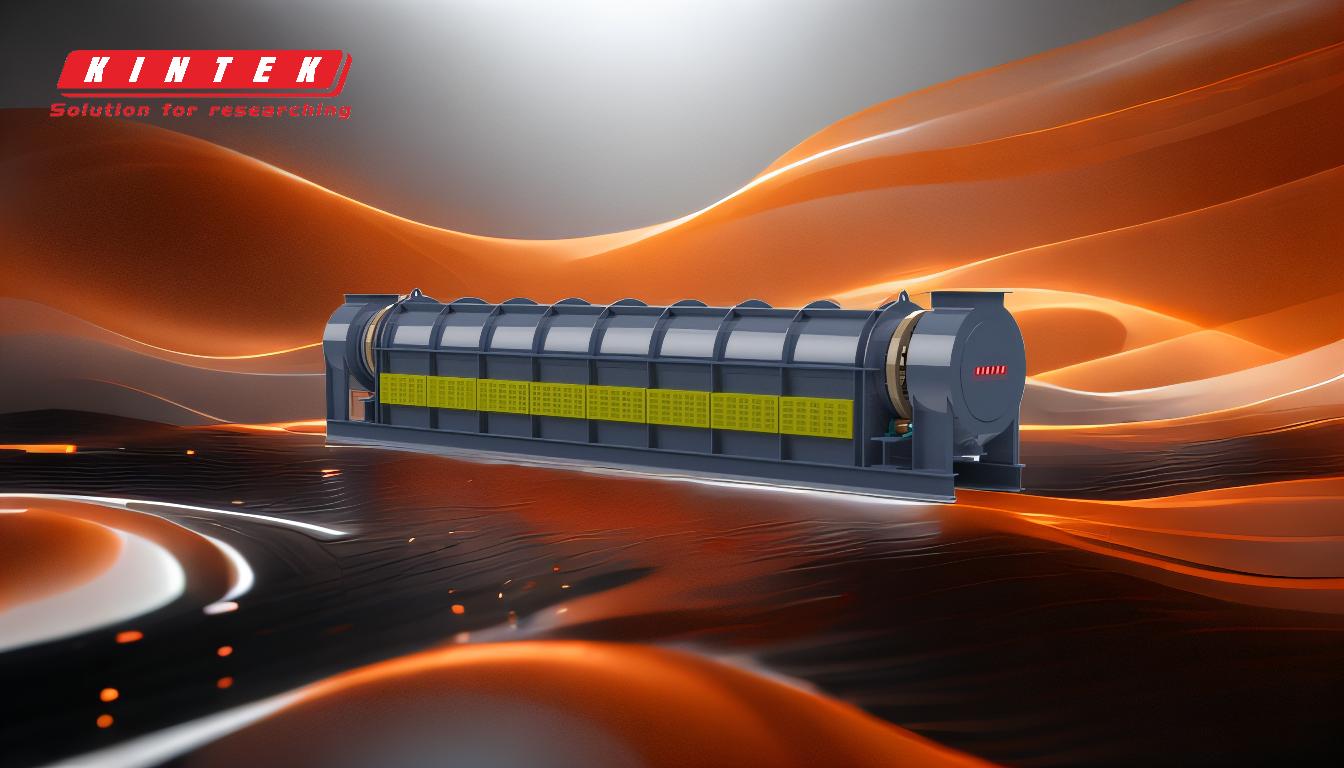
-
Primary Function of a Rotary Kiln:
- A rotary kiln is primarily used to heat solids to a predetermined temperature in a controlled environment to induce chemical or physical reactions. This makes it a critical tool in industries requiring high-temperature processing.
-
Design and Operation:
- The kiln consists of a cylindrical vessel inclined slightly from the horizontal, which rotates slowly about its longitudinal axis. This design ensures uniform heating and mixing of materials as they move from the upper to the lower end.
- Hot gases flow through the kiln, either co-currently (same direction as material flow) or counter-currently (opposite direction), to facilitate efficient heat transfer.
-
Key Applications:
- Calcination: One of the most common uses, especially in the cement industry, where limestone is calcined at high temperatures to produce raw concrete.
- Thermal Desorption: Used to remove contaminants from materials by heating them to high temperatures.
- Sintering: A process that fuses particles into a solid mass without melting them completely, often used in metallurgy and ceramics.
- Incineration: Used for waste treatment, where organic materials are combusted at high temperatures.
-
Versatility in Thermal Processing:
- Rotary kilns are capable of performing multiple thermal functions, including drying, high-temperature chemical transformations, organic combustion, heat setting, reduction roasting, and induration (hardening of materials).
-
Material Transformation:
- The kiln facilitates the transformation of materials by changing their state or chemical composition. For example, it can convert raw materials like limestone into cement clinker or process ores to extract metals.
-
Batch vs. Continuous Processes:
- Rotary kilns can operate in both batch and continuous modes, making them adaptable to various industrial needs. Continuous processes are common in large-scale operations like cement production, while batch processes are used for smaller or specialized applications.
-
Heat Source and Efficiency:
- The heat required for the kiln can be generated internally (e.g., by a flame inside the kiln) or externally (e.g., from an external furnace). The design ensures efficient heat transfer and energy utilization.
-
Industrial Significance:
- Rotary kilns are indispensable in industries such as cement, metallurgy, chemicals, and waste management. Their ability to handle high temperatures and diverse materials makes them a cornerstone of modern industrial processing.
By combining these functions and features, rotary kilns play a crucial role in enabling industrial processes that require precise temperature control and material transformation. Their design and versatility make them a vital piece of equipment for achieving high-quality, consistent results in various applications.
Summary Table:
Aspect | Details |
---|---|
Primary Function | Heats solids to induce chemical or physical reactions in controlled environments. |
Design & Operation | Rotating cylindrical vessel with slight incline for uniform heating and mixing. |
Key Applications | Calcination, sintering, thermal desorption, incineration, and more. |
Versatility | Performs drying, chemical transformations, combustion, and material hardening. |
Material Transformation | Converts raw materials (e.g., limestone to cement clinker) and processes ores. |
Process Modes | Batch or continuous operation for diverse industrial needs. |
Heat Source | Internal (flame) or external (furnace) heat generation for efficiency. |
Industrial Significance | Essential in cement, metallurgy, chemicals, and waste management industries. |
Unlock the potential of rotary kilns for your industrial processes—contact our experts today!