The High-Density Plasma Chemical Vapor Deposition (HDP-CVD) process is a specialized technique used in semiconductor manufacturing to deposit thin films, particularly silicon oxide layers, onto a substrate. This process involves preparing a semiconductor substrate, placing it in a process chamber, and generating high-density plasma to facilitate the deposition. Key gases such as oxygen and silicon source gases are injected to form the silicon oxide layer, while secondary and primary gases like helium are used to control the process. The substrate is heated to temperatures between 550°C and 700°C to ensure proper deposition. This method is known for its ability to produce high-quality, uniform films with excellent step coverage, making it essential for advanced semiconductor devices.
Key Points Explained:
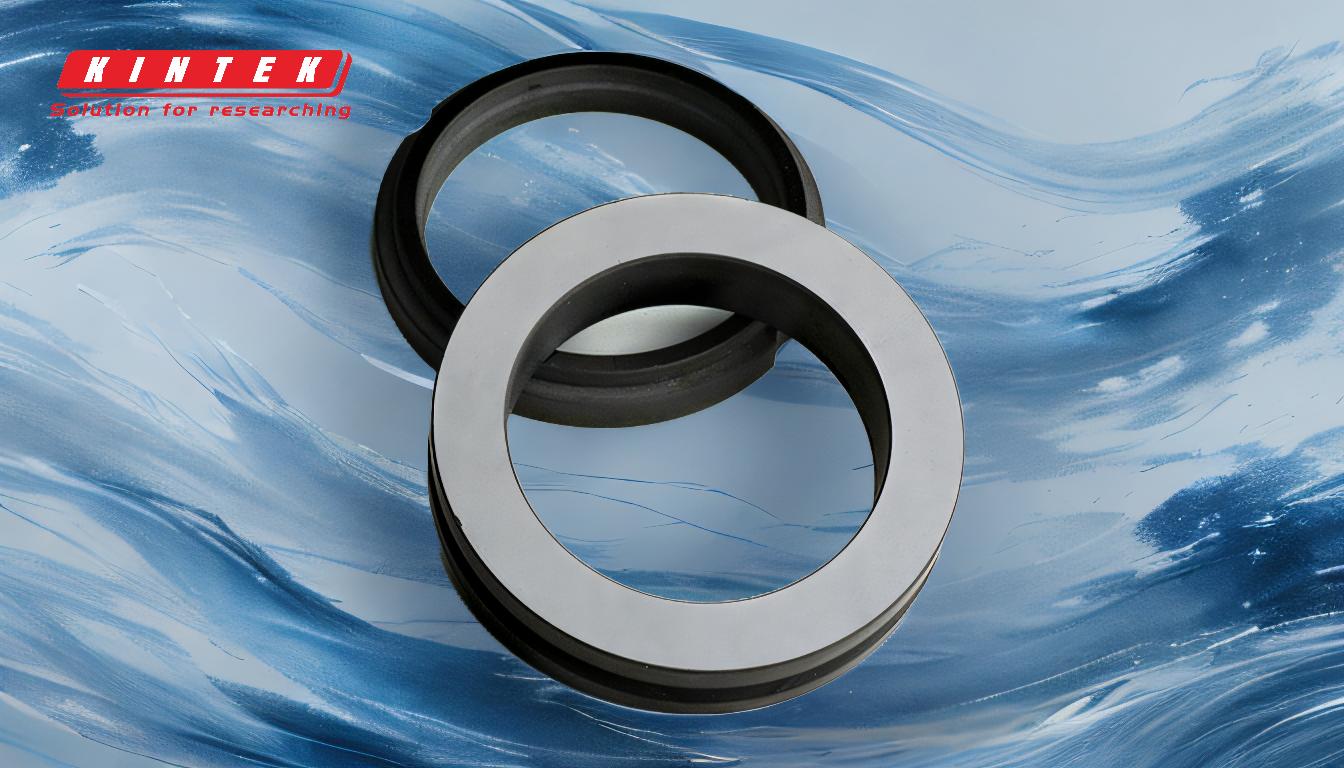
-
Preparation of the Semiconductor Substrate:
- The process begins with the preparation of a semiconductor substrate, which is typically a silicon wafer. This involves cleaning and sometimes pre-treating the substrate to ensure it is free of contaminants and ready for deposition.
-
Placement in the Process Chamber:
- The prepared substrate is then placed inside a process chamber designed for HDP-CVD. This chamber is equipped with the necessary components to generate high-density plasma and control the deposition environment.
-
Generation of High-Density Plasma:
- High-density plasma is generated within the chamber using radio frequency (RF) or microwave energy. This plasma is crucial as it provides the energy needed to break down the precursor gases into reactive species that can form the desired film.
-
Injection of Precursor Gases:
- Oxygen and silicon source gases are injected into the chamber. These gases react in the presence of the high-density plasma to form a silicon oxide layer on the substrate. The use of high-density plasma ensures a high reaction rate, leading to efficient deposition.
-
Use of Secondary and Primary Gases:
- Secondary gases, such as helium, are also introduced into the chamber. These gases help to control the plasma characteristics and improve the uniformity of the deposited film. Helium, in particular, is used for its thermal conductivity, which helps in maintaining a stable temperature within the chamber.
-
Heating of the Substrate:
- The substrate is heated to temperatures ranging from 550°C to 700°C during the deposition process. This heating is essential to ensure that the deposited film adheres well to the substrate and to promote the formation of a high-quality, dense film.
-
Formation of the Silicon Oxide Layer:
- The combination of high-density plasma, precursor gases, and controlled heating results in the formation of a silicon oxide layer on the substrate. This layer is critical for various semiconductor applications, including insulation and passivation layers.
-
Advantages of HDP-CVD:
- The HDP-CVD process offers several advantages, including excellent step coverage, high deposition rates, and the ability to produce films with low defect densities. These characteristics make it particularly suitable for advanced semiconductor devices where precision and reliability are paramount.
In summary, the HDP-CVD process is a sophisticated method for depositing high-quality thin films, particularly silicon oxide, onto semiconductor substrates. It involves a series of carefully controlled steps, including substrate preparation, plasma generation, gas injection, and heating, all of which contribute to the formation of a uniform and reliable film. This process is essential in the fabrication of modern semiconductor devices, where precision and material quality are critical.
Summary Table:
Step | Description |
---|---|
Substrate Preparation | Clean and pre-treat the semiconductor substrate (e.g., silicon wafer). |
Placement in Chamber | Place the substrate in a specialized HDP-CVD process chamber. |
Plasma Generation | Generate high-density plasma using RF or microwave energy. |
Gas Injection | Inject oxygen and silicon source gases to form the silicon oxide layer. |
Use of Secondary Gases | Introduce gases like helium to control plasma and improve film uniformity. |
Substrate Heating | Heat the substrate to 550°C–700°C for proper film adhesion and quality. |
Film Formation | Form a high-quality silicon oxide layer with excellent step coverage. |
Advantages | High deposition rates, low defect densities, and precise film uniformity. |
Discover how the HDP-CVD process can enhance your semiconductor production—contact our experts today!