Molybdenum heat treatment is a critical process to enhance its mechanical properties, such as strength, ductility, and resistance to high temperatures. Molybdenum, being a refractory metal, requires careful handling during heat treatment to avoid brittleness and cracking. The process typically involves annealing to relieve internal stresses and improve machinability, as well as controlled cooling to maintain its structural integrity. Molybdenum boats, often used in high-temperature applications, benefit from these treatments to ensure durability and performance in demanding environments like furnace operations, sintering, and rare earth processing.
Key Points Explained:
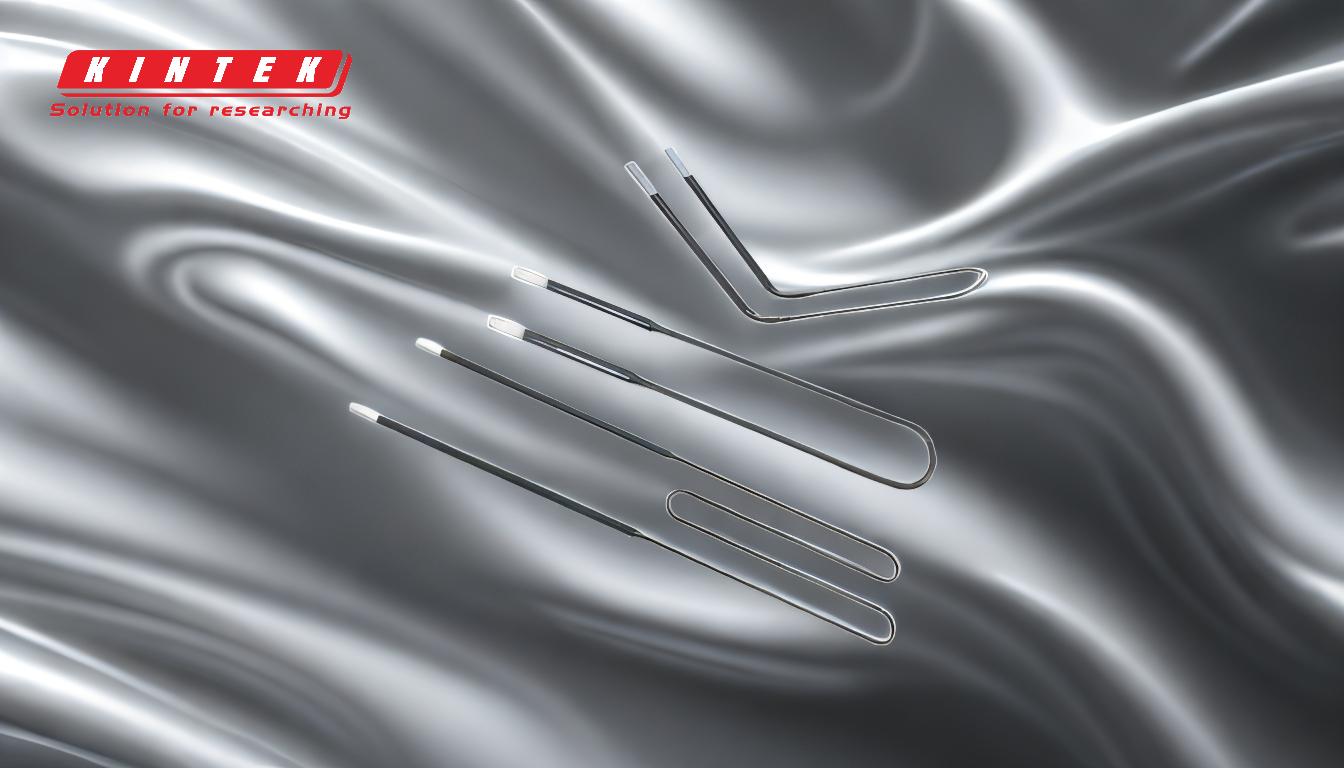
-
Properties of Molybdenum:
- Molybdenum is a refractory metal known for its high melting point (2623°C), excellent thermal conductivity, and resistance to corrosion and wear.
- It is widely used in high-temperature applications, such as in vacuum furnaces, where it can withstand temperatures up to 1700°C without significant degradation.
- Its ductility and strength make it suitable for forming into components like molybdenum boats, which are used in industries such as rare earth processing and nuclear fuel sintering.
-
Heat Treatment Objectives:
- The primary goal of heat treating molybdenum is to relieve internal stresses induced during manufacturing processes like cutting, folding, and welding.
- Heat treatment improves machinability, ductility, and overall mechanical performance, ensuring the material can withstand high-temperature and high-stress environments.
-
Annealing Process:
- Annealing is the most common heat treatment for molybdenum. It involves heating the material to a specific temperature (typically between 800°C and 1200°C) and holding it for a set period to allow recrystallization and stress relief.
- Controlled cooling is essential after annealing to prevent the formation of brittle phases and maintain the material's ductility.
-
Applications in High-Temperature Environments:
- Molybdenum boats are often used in furnace machines for processes like sintering, where they are exposed to extreme temperatures. Proper heat treatment ensures their dimensional stability and longevity.
- In industries like metallurgy, glass, and ceramics, molybdenum components must maintain their structural integrity under continuous high-temperature conditions.
-
Challenges in Heat Treatment:
- Molybdenum becomes brittle at temperatures above 1700°C, so heat treatment must be carefully controlled to avoid exceeding this threshold.
- Rapid cooling or uneven heating can lead to cracking or warping, which compromises the material's performance.
-
Comparison with Other Materials:
- Unlike tungsten, which is harder and more brittle, molybdenum offers better ductility and ease of fabrication, making it more suitable for complex shapes like boats and wires.
- Molybdenum's resistance to staining and corrosion during smelting processes makes it a preferred material in the glass industry.
-
Industrial Relevance:
- Molybdenum boats and other components are critical in applications such as capacitor discharged sintering, nuclear fuel processing, and rare earth element production.
- The material's ability to withstand high temperatures and corrosive environments ensures its widespread use in advanced industrial processes.
By understanding the heat treatment processes and properties of molybdenum, manufacturers can optimize the performance of molybdenum boats and other components, ensuring they meet the rigorous demands of high-temperature applications.
Summary Table:
Aspect | Details |
---|---|
Properties | High melting point (2623°C), thermal conductivity, corrosion resistance |
Heat Treatment Goals | Relieve internal stresses, improve machinability, and enhance ductility |
Annealing Process | Heat to 800°C–1200°C, hold for recrystallization, and control cooling |
Applications | Furnace operations, sintering, rare earth processing, and nuclear fuel |
Challenges | Avoid brittleness above 1700°C, prevent cracking during rapid cooling |
Comparison with Tungsten | Better ductility, easier fabrication, and resistance to staining |
Enhance your molybdenum components' performance—contact our experts today for tailored heat treatment solutions!