The HIP (Hot Isostatic Pressing) process in ceramics is a high-pressure and high-temperature treatment that enhances the material's strength, durability, and overall quality. By subjecting the ceramic material to uniform pressure and heat using argon gas in a specialized HIP machine, the process eliminates internal voids and defects, resulting in improved mechanical properties. This method not only reduces scrap and minimizes post-processing but can also replace separate homogenization treatments, making it a versatile and efficient solution for a wide range of ceramic applications.
Key Points Explained:
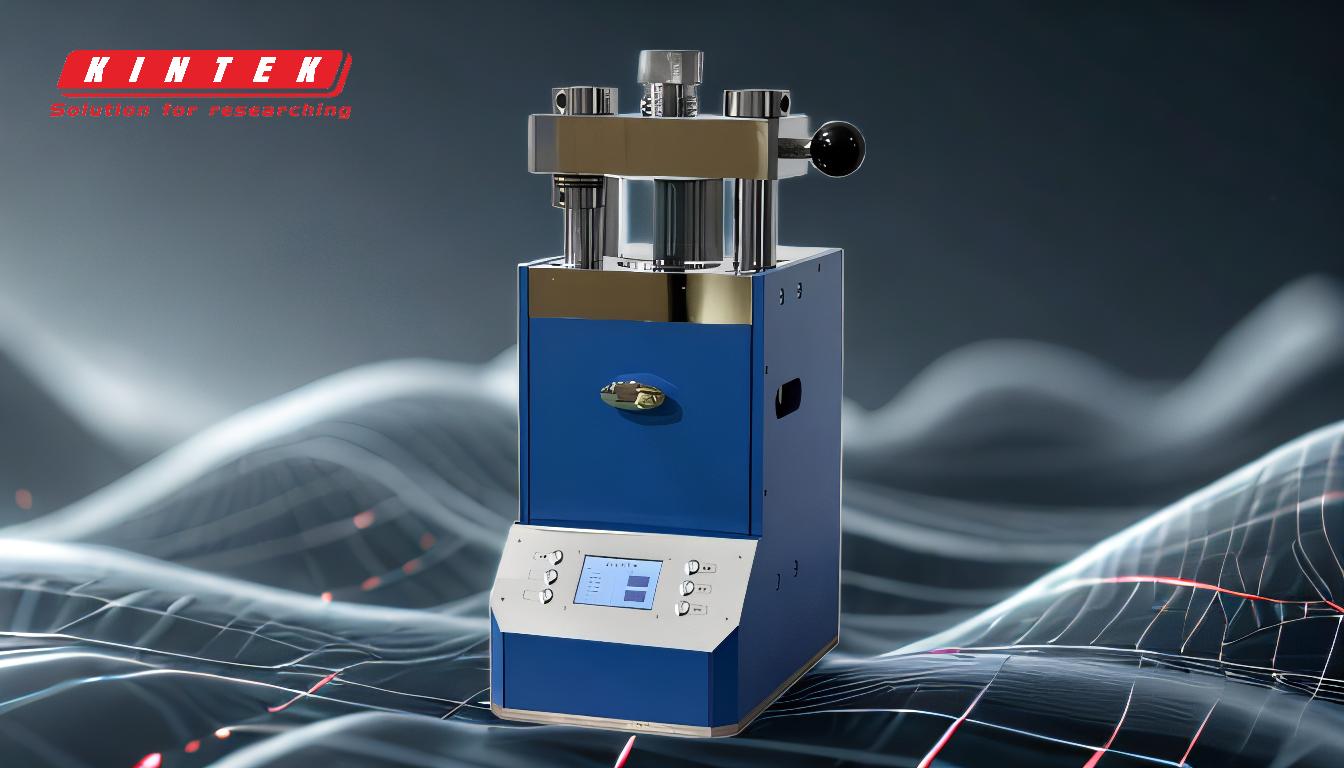
-
Purpose of the HIP Process in Ceramics:
- The HIP process is designed to improve the quality and mechanical properties of ceramic materials. By eliminating internal defects such as voids and porosity, it enhances the material's strength, durability, and reliability.
- This process is particularly beneficial for ceramics used in demanding applications, such as aerospace, medical implants, and industrial components, where high performance and reliability are critical.
-
How the HIP Process Works:
- The ceramic material is placed inside an HIP machine, which consists of a furnace and a pressure vessel.
- Argon gas is introduced into the vessel, and both temperature and pressure are increased simultaneously. The typical pressure range is 100-200 MPa, and temperatures can reach up to 2000°C, depending on the material.
- The combination of high pressure and heat causes the material to densify, closing internal voids and improving its microstructure.
- After a specific holding time, the vessel is cooled, and the treated ceramic is removed, now exhibiting enhanced physical properties.
-
Benefits of the HIP Process:
- Improved Mechanical Properties: The process results in ceramics with higher strength, toughness, and fatigue resistance, making them suitable for critical applications.
- Reduced Scrap and Machining: By eliminating defects, the HIP process reduces the need for extensive machining and minimizes material waste, leading to cost savings.
- Versatility: HIP can be applied to a wide range of ceramic materials, including oxides, carbides, and nitrides, as well as composites.
- Rejuvenation of Old Parts: The process can restore the properties of worn or damaged ceramic components, extending their service life.
-
Integration with Homogenization Treatments:
- The HIP process is often carried out at temperatures similar to those used in homogenization treatments. This overlap allows HIP to serve a dual purpose, eliminating the need for separate homogenization steps in some cases.
- This integration simplifies the manufacturing process, reduces energy consumption, and saves time, making HIP an efficient solution for ceramic production.
-
Applications of HIP in Ceramics:
- Aerospace: HIP-treated ceramics are used in turbine blades, heat shields, and other components that require high strength and thermal stability.
- Medical: Ceramic implants, such as dental crowns and orthopedic prosthetics, benefit from the enhanced durability and biocompatibility achieved through HIP.
- Industrial: Cutting tools, wear-resistant components, and electrical insulators are examples of industrial applications where HIP-processed ceramics excel.
-
Environmental and Economic Advantages:
- By reducing material waste and minimizing the need for additional processing, the HIP process contributes to more sustainable manufacturing practices.
- The ability to rejuvenate old parts also supports circular economy principles, reducing the demand for new raw materials and lowering overall production costs.
In summary, the HIP process is a transformative technique for ceramics, offering significant improvements in material properties, cost efficiency, and environmental sustainability. Its ability to integrate with other treatments and its wide applicability make it a cornerstone of modern ceramic manufacturing.
Summary Table:
Aspect | Details |
---|---|
Purpose | Improves ceramic quality by eliminating voids and enhancing mechanical properties. |
How It Works | Uses argon gas, high pressure (100-200 MPa), and high heat (up to 2000°C). |
Benefits | Enhanced strength, reduced scrap, versatility, and rejuvenation of old parts. |
Applications | Aerospace, medical implants, industrial components, and cutting tools. |
Environmental Impact | Reduces waste, supports sustainability, and lowers production costs. |
Unlock the potential of ceramics with the HIP process—contact our experts today for tailored solutions!