The HIP (Hot Isostatic Pressing) sintering process is a specialized thermal consolidation technique used in powder metallurgy to create high-density, high-performance materials. It involves applying high temperatures and uniform gas pressure simultaneously to compact powder materials, eliminating porosity and impurities. This results in a product with a homogeneous microstructure, enhanced mechanical properties, and near-theoretical density. The process is particularly effective for materials like cemented carbides, where it combines vacuum sintering with post-HIP operations to achieve optimal densification. HIP sintering improves material characteristics such as strength, toughness, and corrosion resistance, making it a preferred method for producing advanced components in industries like aerospace, automotive, and tooling.
Key Points Explained:
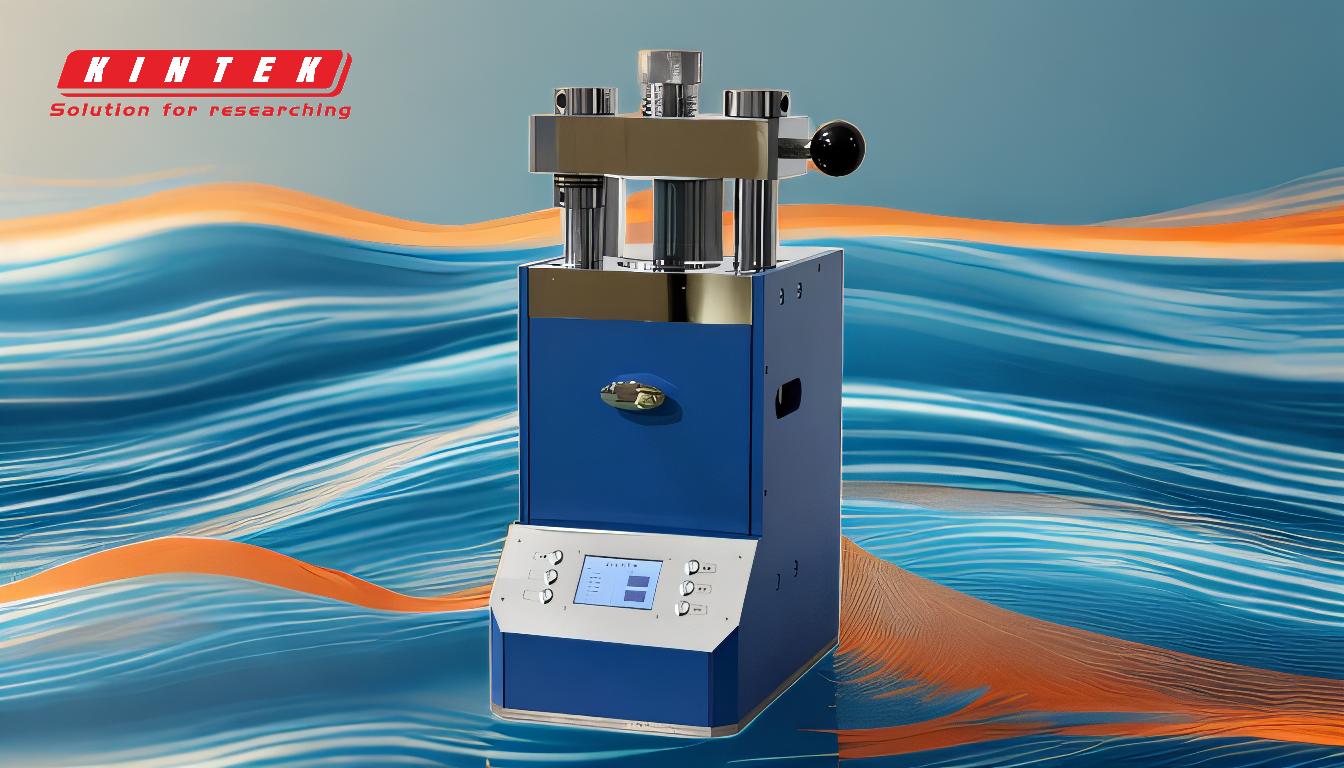
-
Definition of HIP Sintering:
- HIP sintering is a process that combines high temperatures and uniform gas pressure to densify powder materials.
- It is used to eliminate porosity and impurities, resulting in a compact solid with minimal defects.
-
Key Mechanisms:
- Material Deformation: The primary mechanism where high pressure causes the powder particles to deform and bond.
- Creep: A secondary mechanism where the material slowly deforms under high temperature and pressure, aiding in densification.
- Diffusion Bonding: Atoms diffuse across particle boundaries, further eliminating pores and creating a homogeneous microstructure.
-
Process Steps:
- Vacuum Sintering: The material is first heated in a vacuum to remove gases and impurities.
- HIP Application: After vacuum sintering, the vacuum is replaced with pressurized argon gas, applying uniform pressure to the material.
- Cooling: The material is cooled under pressure to maintain its densified structure.
-
Advantages of HIP Sintering:
- Enhanced Material Properties: Produces materials with high strength, toughness, and corrosion resistance.
- Near-Theoretical Density: Achieves almost full theoretical density, minimizing porosity.
- Efficiency: Operates at lower temperatures compared to conventional sintering, reducing energy consumption and environmental impact.
-
Applications:
- Cemented Carbides: Commonly used in tooling and cutting tools due to their hardness and wear resistance.
- Aerospace Components: Produces high-performance parts with excellent mechanical properties.
- Medical Implants: Creates biocompatible materials with high density and strength.
-
Comparison with Conventional Sintering:
- Temperature: HIP sintering operates at lower temperatures (e.g., 1400°C) compared to conventional sintering (e.g., 1450°C).
- Pressure: HIP applies uniform gas pressure, while conventional sintering relies solely on heat.
- Density: HIP achieves higher density and better material properties due to the combined effect of heat and pressure.
-
Environmental and Economic Benefits:
- Energy Efficiency: Lower operating temperatures reduce energy consumption.
- Reduced Waste: Minimizes material defects and waste, improving overall process efficiency.
-
Challenges:
- Cost: The equipment and process are more expensive than conventional sintering.
- Complexity: Requires precise control of temperature and pressure, making the process more complex.
By understanding these key points, equipment and consumable purchasers can better evaluate the benefits and applications of HIP sintering, ensuring they select the most appropriate materials and processes for their specific needs.
Summary Table:
Aspect | Details |
---|---|
Definition | Combines high temperatures and uniform gas pressure to densify materials. |
Key Mechanisms | Material deformation, creep, and diffusion bonding. |
Process Steps | Vacuum sintering, HIP application, and cooling under pressure. |
Advantages | Enhanced strength, toughness, corrosion resistance, and near-theoretical density. |
Applications | Cemented carbides, aerospace components, and medical implants. |
Comparison | Lower temperature, uniform pressure, and higher density than conventional sintering. |
Benefits | Energy efficiency, reduced waste, and improved material properties. |
Challenges | Higher cost and process complexity. |
Ready to enhance your materials with HIP sintering? Contact us today to learn more!