The induction melting method is a highly efficient and precise technique used to melt metals, particularly those that are reactive and cannot be melted in the presence of air. This method utilizes electromagnetic induction to generate heat within the metal, causing it to melt. The process is often conducted in a vacuum to prevent contamination from gases like oxygen and nitrogen, which can react with the metal. Key components include an induction furnace, a refractory-lined crucible, and an induction coil. The method is widely used in industries requiring high-purity metals and alloys, such as aerospace and medical device manufacturing.
Key Points Explained:
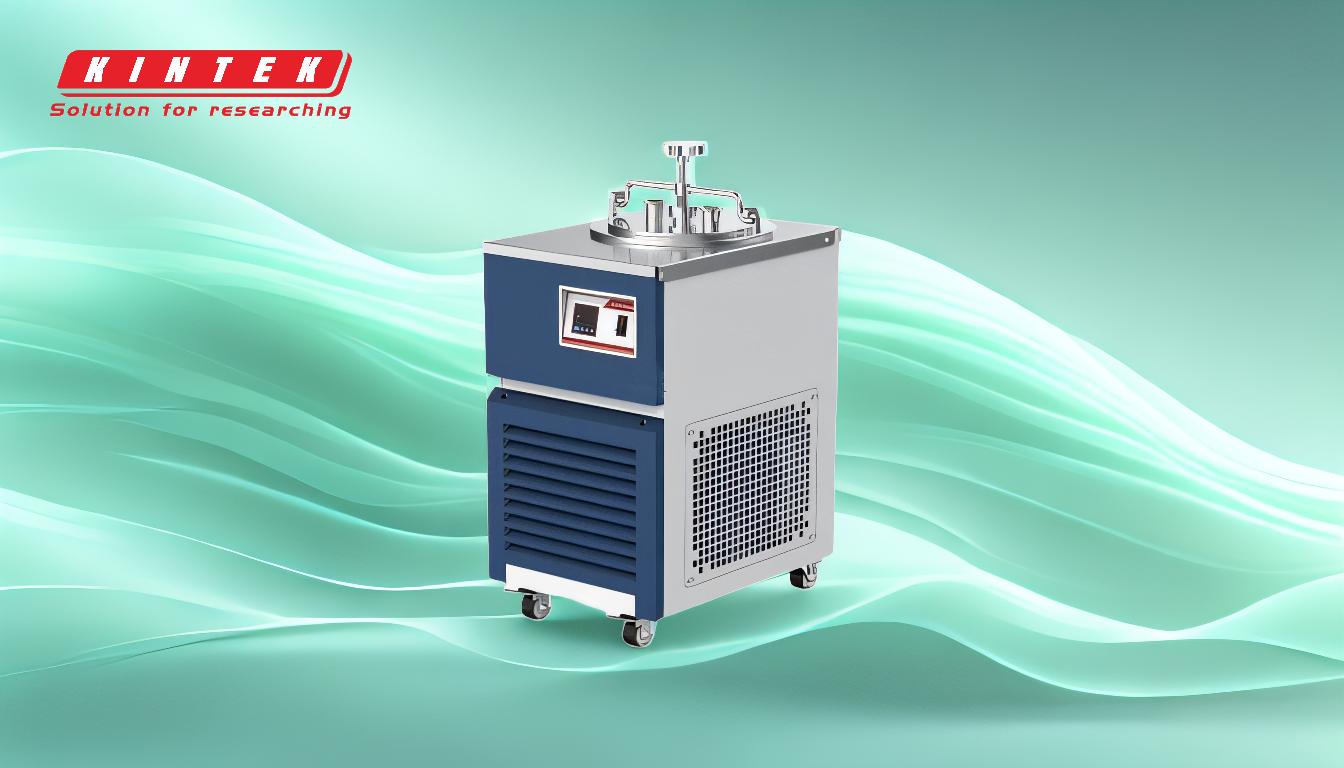
-
Electromagnetic Induction and Eddy Currents:
- Induction melting relies on electromagnetic induction to generate heat. When an alternating current passes through the induction coil, it creates a fluctuating magnetic field. This field induces eddy currents within the metal placed in the crucible. These eddy currents generate heat due to the electrical resistance of the metal, leading to its melting. This method is particularly effective for metals with high electrical conductivity.
-
Vacuum Environment:
- The process is often conducted in a vacuum chamber to eliminate the presence of reactive gases like oxygen and nitrogen. This is crucial for metals and alloys that are prone to oxidation or nitridation. The vacuum environment ensures that the final product is free from gas impurities, resulting in higher purity and better mechanical properties.
-
Refractory-Lined Crucible:
- The crucible, which holds the metal, is lined with refractory materials that can withstand extremely high temperatures. This lining protects the crucible from the intense heat generated during the melting process and ensures that the metal does not react with the crucible material, maintaining the purity of the melt.
-
Induction Furnace:
- The core component of the induction melting setup is the induction furnace. This furnace consists of an induction coil that surrounds the crucible. The coil is connected to a power supply that provides the alternating current necessary to generate the magnetic field. The design of the furnace allows for precise control over the melting process, making it suitable for producing high-quality alloys.
-
Calculating Power Requirements:
- The power required for the induction melting process can be calculated using the formula: [ P = \frac{C \times T \times G}{0.24 \times t \times \eta} ] where (C) is the specific heat of the material, (T) is the heating temperature, (G) is the weight of the workpiece, (t) is the time, and (\eta) is the heating efficiency. This formula helps in determining the energy requirements for melting specific quantities of metal, ensuring efficient operation of the furnace.
-
Electromagnetic Stirring:
- One of the advantages of induction melting is the electromagnetic stirring effect. The eddy currents not only generate heat but also create a stirring motion within the molten metal. This stirring helps in achieving a uniform composition and temperature throughout the melt, which is essential for producing high-quality alloys with consistent properties.
-
Applications and Advantages:
- Induction melting is widely used in industries that require high-purity metals and alloys, such as aerospace, medical devices, and electronics. The method offers several advantages, including precise temperature control, high purity of the final product, and the ability to melt reactive metals that cannot be processed in air. Additionally, the process is energy-efficient and can be automated for consistent results.
In summary, the induction melting method is a sophisticated and efficient technique for melting metals, particularly those that are reactive and require high purity. The use of electromagnetic induction, combined with a vacuum environment, ensures that the final product is free from impurities and has uniform composition. This method is essential for industries that demand high-quality metals and alloys with precise properties.
Summary Table:
Key Aspect | Description |
---|---|
Electromagnetic Induction | Generates heat via eddy currents in the metal, ideal for high-conductivity metals. |
Vacuum Environment | Prevents contamination by reactive gases, ensuring high-purity metals. |
Refractory-Lined Crucible | Withstands extreme heat, protecting the crucible and maintaining metal purity. |
Induction Furnace | Core component with precise control, suitable for high-quality alloy production. |
Power Calculation | Formula: (P = \frac{C \times T \times G}{0.24 \times t \times \eta}), ensuring efficient operation. |
Electromagnetic Stirring | Ensures uniform composition and temperature in the molten metal. |
Applications | Aerospace, medical devices, electronics—ideal for high-purity metals and alloys. |
Discover how induction melting can revolutionize your metal processing—contact us today!