The leak rate for a vacuum furnace is a critical performance metric that ensures the furnace maintains its vacuum integrity, preventing contamination and ensuring optimal heat treatment results. The leak rate is typically measured by isolating the furnace after achieving a high vacuum level, recording the pressure over time, and calculating the rate of pressure increase. A standard acceptance criterion is a leak rate of less than 5 Microns per hour. This test is essential for maintaining the cleanliness and efficiency of the vacuum furnace, as higher leak rates can introduce impurities and adversely affect heat-treating processes.
Key Points Explained:
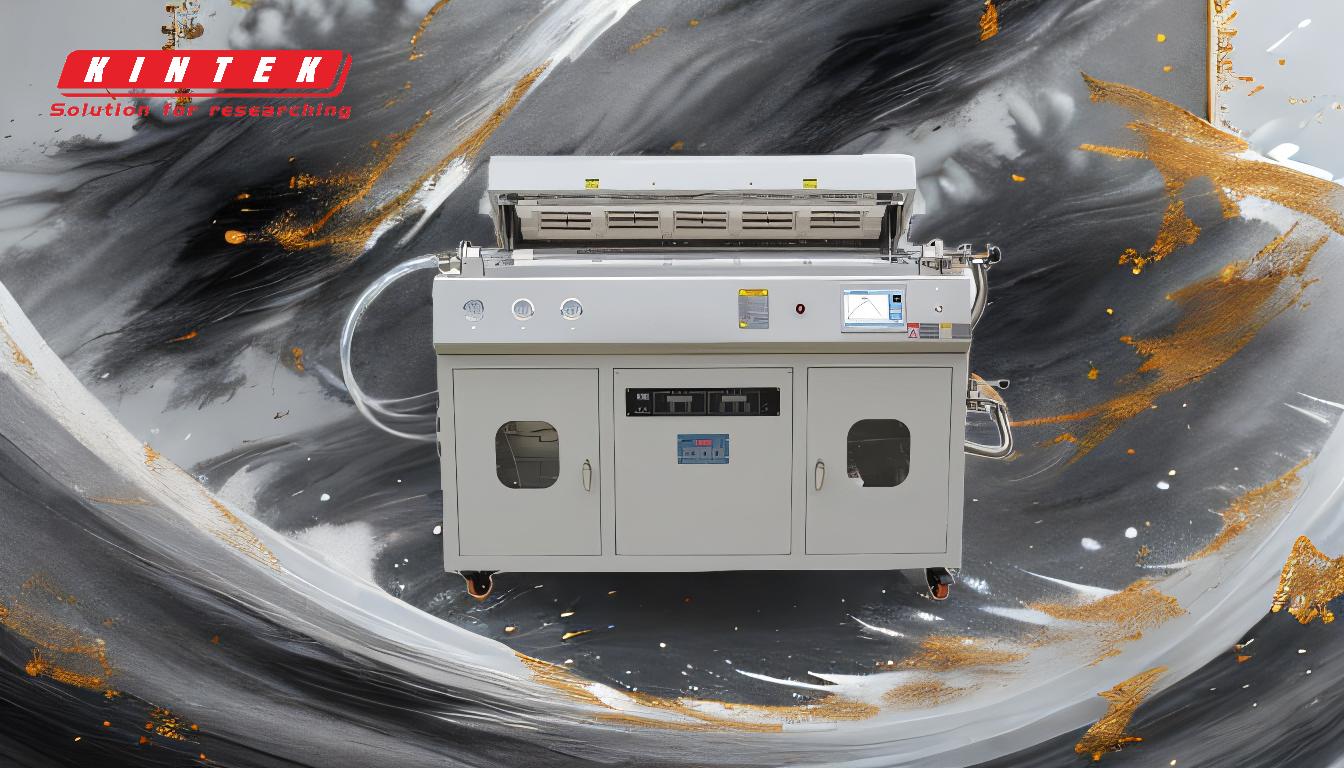
-
Definition of Leak Rate:
- The leak rate measures the rate at which air or other gases enter the vacuum furnace when it is isolated from the pumping system. It is expressed in units like Microns per hour (μm/hr) or Torr per hour.
- A lower leak rate indicates better vacuum integrity, ensuring a contamination-free environment for heat treatment processes.
-
Importance of Leak Rate Testing:
- Leak rate testing ensures that the furnace maintains its vacuum tightness, preventing impurities from entering the processing environment.
- Contamination from leaks can lead to poor heat-treating results, such as oxidation or inconsistent material properties.
- Regular leak rate testing is part of maintaining the furnace's performance and extending its operational life.
-
How Leak Rate is Measured:
- The furnace is pumped down to a high vacuum level, typically 1 x 10^-4 Torr or better.
- The pumping system is then isolated, and the vacuum level is recorded after 30 and 60 minutes.
- The leak rate is calculated based on the pressure increase over time and compared to acceptance criteria, such as less than 5 Microns per hour.
-
Acceptance Criteria for Leak Rate:
- A leak rate of less than 5 Microns per hour is generally considered acceptable for most vacuum furnaces.
- Higher leak rates can indicate issues such as worn seals, improper door closures, or other mechanical problems that need to be addressed.
-
Impact of High Leak Rates:
- A higher leak rate allows air to continuously enter the furnace, increasing the residual oxygen content.
- This can lead to oxidation, contamination, and inconsistent heat-treating results, particularly in processes like annealing, quenching, or brazing.
- Maintaining a low leak rate is crucial for achieving the desired material properties and ensuring process consistency.
-
Operational Best Practices:
- Operators must follow strict cleanliness protocols, such as wearing clean garments and white gloves, to avoid introducing contaminants.
- Workpieces should be handled carefully, packed in plastic envelopes, and sealed with nitrogen to prevent contamination.
- Regular maintenance and inspection of seals, gaskets, and other components are essential to maintain a low leak rate.
-
Relation to Other Vacuum Performance Metrics:
- The leak rate is one of several key metrics for evaluating a vacuum furnace's performance, including ultimate vacuum, operating vacuum, and pump-down times.
- For example, diffusion-pumped furnaces typically achieve an ultimate vacuum of 10^-6 Torr, while mechanical pump/blower combinations aim for 20 Microns Hg or better.
- These metrics collectively ensure the furnace operates efficiently and meets the requirements for specific heat treatment processes.
By understanding and maintaining the leak rate of a vacuum furnace, operators can ensure the integrity of the vacuum environment, achieve consistent heat-treating results, and prolong the lifespan of the equipment. For more details on vacuum furnaces, visit vacuum furnace.
Summary Table:
Aspect | Details |
---|---|
Definition | Measures air/gas entry rate when isolated, expressed in Microns/hour (μm/hr). |
Acceptance Criteria | Leak rate should be <5 Microns/hour for optimal performance. |
Measurement Process | Isolate furnace, record pressure over time, calculate pressure increase. |
Impact of High Leak Rate | Causes oxidation, contamination, and inconsistent heat-treating results. |
Best Practices | Regular testing, cleanliness protocols, and maintenance of seals/gaskets. |
Ensure your vacuum furnace operates at peak performance—contact our experts today for guidance!