The life expectancy of a heating element depends on several factors, including usage patterns, maintenance, and the quality of the element. On average, a heating element in an oven can last between 5 to 15 years. However, this range can vary significantly based on operational conditions such as the furnace atmosphere, watt density, operating temperature, and whether the element is used continuously or intermittently. Manufacturers typically only warrant against manufacturing defects, as factors like rapid heating and cooling cycles or operation in a reducing atmosphere can significantly impact the element's lifespan. Proper maintenance and understanding of these variables are crucial for maximizing the longevity of a heating element.
Key Points Explained:
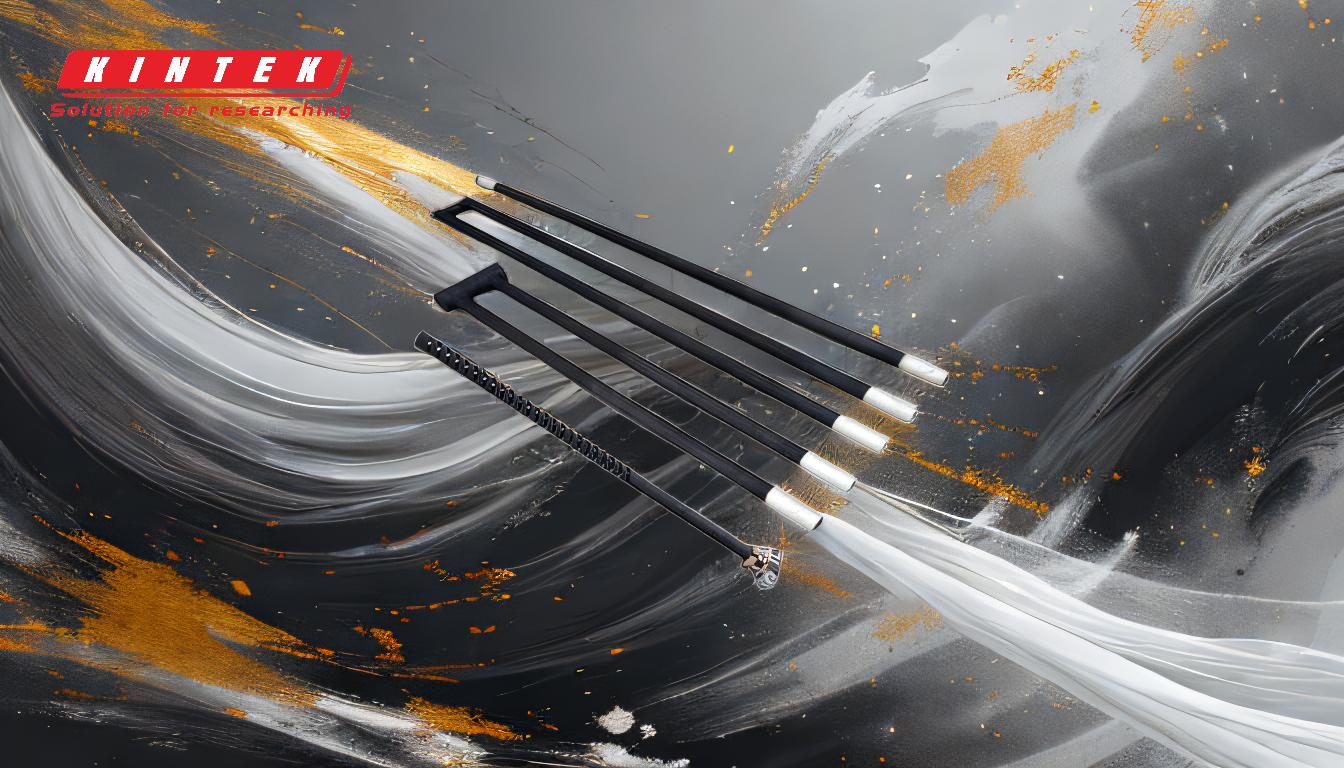
-
Average Lifespan of a Heating Element:
- Heating elements, particularly in ovens, generally last between 5 to 15 years. This range is influenced by factors such as usage frequency, maintenance practices, and the quality of the element itself.
-
Factors Affecting Lifespan:
- Furnace Atmosphere: The environment in which the heating element operates plays a significant role. For example, a reducing atmosphere can shorten the element's life.
- Watt Density: Higher watt densities can lead to faster degradation of the heating element.
- Operating Temperature: Consistently operating at high temperatures can reduce the element's lifespan.
- Maintenance Frequency: Regular maintenance can help extend the life of a heating element by ensuring it operates efficiently and identifying issues early.
- Service Type: Continuous use typically results in a shorter lifespan compared to intermittent use.
-
Manufacturer Warranties:
- Manufacturers usually only provide warranties against manufacturing defects. This is because many external factors, such as rapid heating and cooling cycles or operation in specific atmospheres, can affect the element's longevity and are beyond the manufacturer's control.
-
Specific Considerations for Silicon Carbide Heating Elements:
- Silicon carbide heating elements are particularly sensitive to the factors mentioned above. Their lifespan can be significantly impacted by the furnace atmosphere, watt density, operating temperature, and whether they are used continuously or intermittently.
-
Importance of Maintenance:
- Regular maintenance is crucial for maximizing the lifespan of a heating element. This includes cleaning, inspecting for damage, and ensuring the element operates within recommended parameters.
-
Practical Tips for Extending Lifespan:
- Avoid rapid heating and cooling cycles.
- Operate within the recommended temperature range.
- Ensure the furnace atmosphere is suitable for the element.
- Perform regular maintenance checks.
Understanding these key points can help equipment and consumable purchasers make informed decisions about the selection, use, and maintenance of heating elements, thereby optimizing their lifespan and performance.
Summary Table:
Key Factor | Impact on Lifespan |
---|---|
Furnace Atmosphere | Reducing atmospheres can shorten lifespan. |
Watt Density | Higher watt density leads to faster degradation. |
Operating Temperature | High temperatures reduce lifespan. |
Maintenance Frequency | Regular maintenance extends lifespan by ensuring efficient operation. |
Service Type | Continuous use shortens lifespan compared to intermittent use. |
Manufacturer Warranty | Covers only manufacturing defects, not external factors like rapid heating cycles. |
Want to extend the life of your heating elements? Contact our experts today for tailored advice!