The maximum temperature for sintering depends on the material, equipment, and process used. Direct sintering can achieve temperatures up to 3000°C, while standard sintering furnaces typically operate between 1120°C and 1800°C. High-temperature sintering, often used for metals, can reach up to 2050°F (1121°C) or higher, depending on the material and desired properties. Factors like material composition, particle size, and sintering atmosphere also influence the maximum achievable temperature. The choice of temperature is critical for optimizing densification, mechanical properties, and cost-effectiveness.
Key Points Explained:
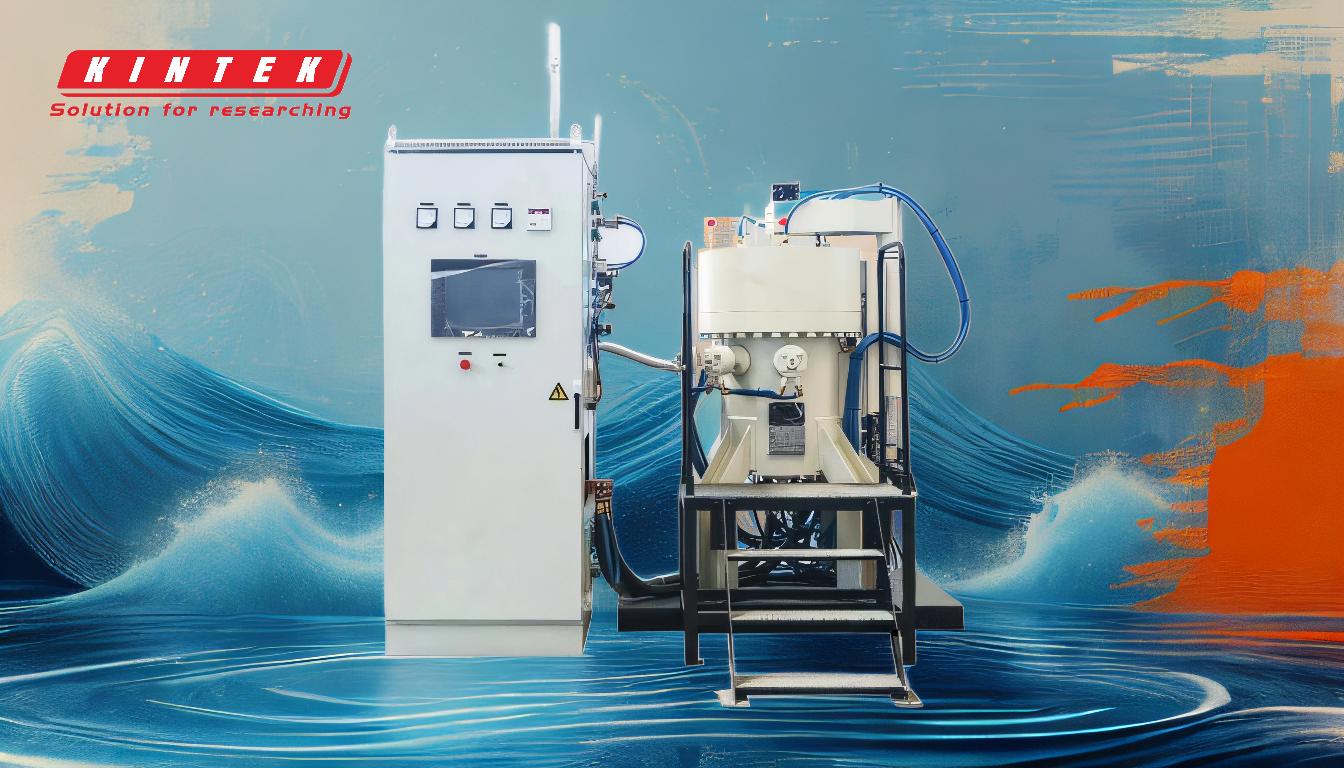
-
Maximum Sintering Temperature Ranges:
- Direct Sintering: Can reach up to 3000°C with high currents, as mentioned in the reference. This method is used for specialized materials requiring extreme heat.
- Standard Sintering Furnaces: Typically operate between 1120°C and 1800°C, depending on the furnace design and material requirements.
- High-Temperature Sintering: Used for metals, particularly iron-heavy alloys, and can reach 2050°F (1121°C) or higher. This process enhances mechanical properties like tensile strength and fatigue resistance.
-
Factors Influencing Maximum Sintering Temperature:
- Material Properties: Different materials have unique sintering temperature requirements. For example, ceramics and metals often require higher temperatures than polymers.
- Equipment Capabilities: The furnace type (belt conveyor, push, or batch) and its maximum operating temperature limit the achievable sintering temperature.
- Atmosphere: Sintering in a vacuum or inert gas (e.g., argon or nitrogen) can enable higher temperatures compared to air, as it prevents oxidation and contamination.
-
Impact of Temperature on Sintering Outcomes:
- Densification: Higher temperatures generally improve densification by enhancing particle bonding and reducing porosity.
- Mechanical Properties: Elevated temperatures can increase tensile strength, bending fatigue strength, and impact energy, but may also lead to grain growth or phase changes.
- Cost and Energy: Higher temperatures require more energy and advanced equipment, increasing operational costs.
-
Trade-offs and Considerations:
- Material Degradation: Excessive temperatures can cause material degradation, such as melting or unwanted phase transformations.
- Process Control: Precise control of temperature, heating rate, and cooling rate is essential to achieve desired properties without defects.
- Economic Feasibility: High-temperature sintering is more expensive due to increased energy consumption and equipment wear.
-
Practical Applications:
- Metals: High-temperature sintering is commonly used for iron, steel, and other alloys to enhance strength and durability.
- Ceramics: Sintering at extreme temperatures (up to 3000°C) is used for advanced ceramics in aerospace and electronics.
- Polymers: Lower sintering temperatures are sufficient for polymers, typically below 300°C.
In summary, the maximum sintering temperature varies widely based on material, equipment, and process requirements. Understanding these factors is crucial for optimizing sintering outcomes and achieving the desired material properties.
Summary Table:
Sintering Type | Temperature Range | Key Applications |
---|---|---|
Direct Sintering | Up to 3000°C | Specialized materials requiring extreme heat |
Standard Sintering | 1120°C - 1800°C | General-purpose sintering for various materials |
High-Temperature Sintering | 2050°F (1121°C) or higher | Metals, particularly iron-heavy alloys |
Need help determining the right sintering temperature for your materials? Contact our experts today!