Sputter deposition is a widely used physical vapor deposition (PVD) technique for creating thin films on substrates. It involves bombarding a target material with high-energy ions, typically from an argon plasma, to eject atoms from the target into the gas phase. These ejected atoms then travel through a vacuum chamber and deposit onto a substrate, forming a thin, uniform film. The process is highly controllable, produces dense and conformal coatings, and is suitable for a wide range of materials, making it a preferred method in industries such as semiconductors, optics, and solar cells.
Key Points Explained:
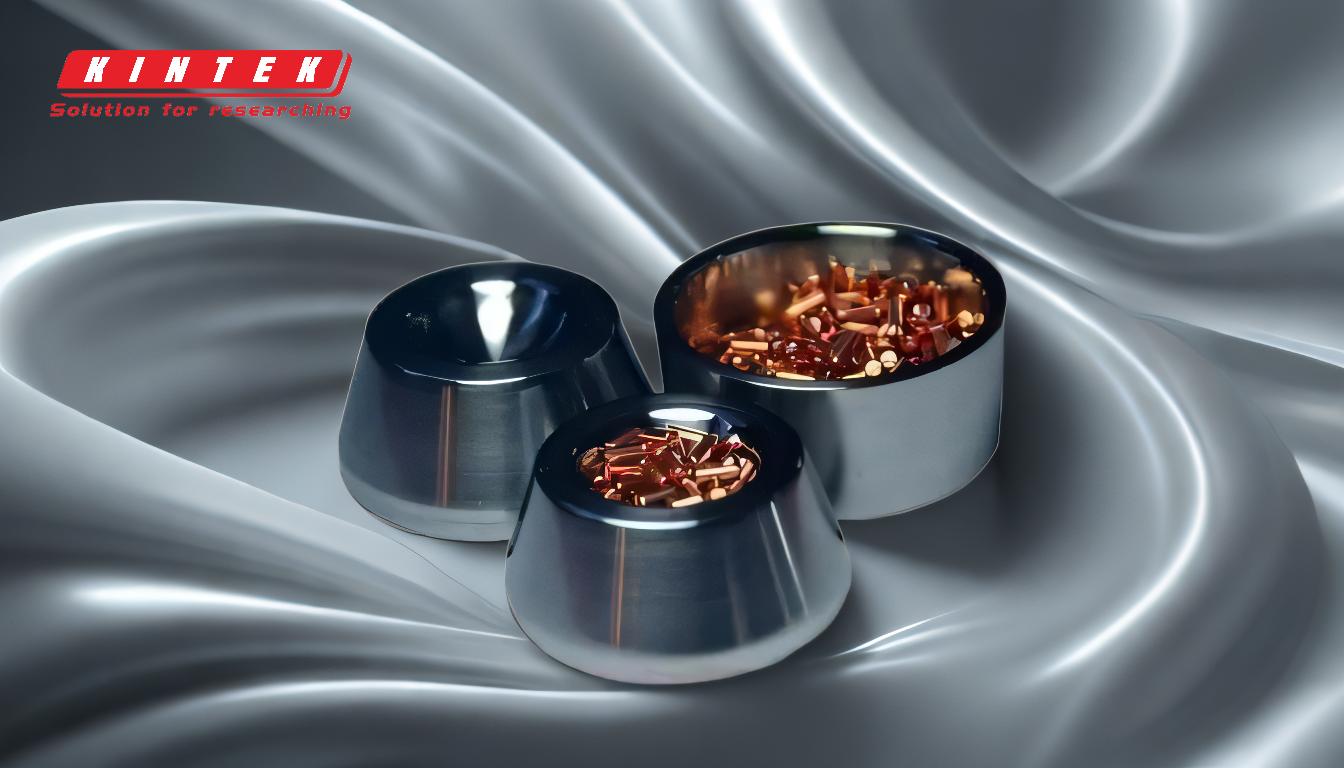
-
Basic Mechanism of Sputter Deposition:
- Sputter deposition relies on the phenomenon of sputtering, where high-energy ions (usually argon ions) collide with a solid target material.
- The collision transfers momentum to the target atoms, causing them to be ejected from the surface and enter the gas phase.
- These ejected atoms travel through a vacuum environment and deposit onto a substrate, forming a thin film.
-
Role of Plasma in Sputtering:
- A plasma is created by ionizing a process gas, typically argon, within a vacuum chamber.
- The plasma consists of positively charged argon ions and free electrons.
- The target material is negatively charged (cathode), attracting the positively charged ions from the plasma.
- The high-energy ions bombard the target, ejecting atoms through momentum transfer.
-
Ejection and Deposition of Target Atoms:
- The ejected atoms from the target are in a high-energy state, which allows them to travel ballistically through the vacuum chamber.
- These atoms condense onto the substrate, forming a thin film with strong adhesion and uniformity.
- The process is highly directional, allowing for precise control over film thickness and composition.
-
Advantages Over Other Deposition Methods:
- Compared to thermal evaporation, sputter deposition produces films with better adhesion and density due to the higher energy of the sputtered atoms.
- It is suitable for a wide range of materials, including metals, alloys, and ceramics.
- The process can be scaled for large-area coatings and is compatible with complex geometries.
-
Magnetron Sputtering:
- Magnetron sputtering is an advanced form of sputter deposition that uses magnetic fields to confine the plasma near the target surface.
- This increases the ionization efficiency and sputtering rate, resulting in faster deposition and better film quality.
- Magnetron sputtering is particularly useful for depositing dense, conformal coatings on complex substrates.
-
Applications of Sputter Deposition:
- Semiconductors: Used for depositing conductive and insulating layers in integrated circuits.
- Optics: Coating lenses and mirrors with anti-reflective or reflective layers.
- Solar Cells: Depositing thin films for photovoltaic applications.
- Decorative Coatings: Applying durable and aesthetically pleasing coatings on consumer products.
-
Resputtering and Film Quality:
- Resputtering occurs when deposited atoms are re-emitted from the substrate due to further ion bombardment.
- This can affect film uniformity and composition but can also be controlled to improve film properties.
- Proper control of process parameters, such as pressure, power, and substrate bias, is critical for achieving high-quality films.
-
Process Control and Parameters:
- Key parameters in sputter deposition include gas pressure, ion energy, target material, and substrate temperature.
- These parameters influence the sputtering rate, film density, and adhesion.
- Advanced systems often include in-situ monitoring and feedback control to optimize film properties.
In summary, sputter deposition is a versatile and precise method for thin film deposition, leveraging the physical process of sputtering to create high-quality coatings. Its ability to work with a wide range of materials and produce dense, conformal films makes it indispensable in many high-tech industries.
Summary Table:
Aspect | Details |
---|---|
Mechanism | High-energy ions bombard a target, ejecting atoms that deposit on a substrate. |
Role of Plasma | Argon plasma ionizes to create ions that sputter target material. |
Advantages | Produces dense, uniform films; works with metals, alloys, and ceramics. |
Magnetron Sputtering | Uses magnetic fields to enhance sputtering rates and film quality. |
Applications | Semiconductors, optics, solar cells, and decorative coatings. |
Process Control | Key parameters: gas pressure, ion energy, target material, substrate temp. |
Discover how sputter deposition can revolutionize your thin film applications—contact our experts today!