Heating elements are crucial components in various applications, and their efficiency depends on factors like material, design, and operating conditions. The most efficient type of heating element is determined by its ability to convert electrical energy into heat with minimal losses, durability, and suitability for specific applications. Based on the provided references, ceramic heaters stand out as the most efficient heating element due to their ability to convert 96% of input power into heat, making them highly energy-efficient. Additionally, stainless steel heating elements are also highly efficient, offering fast thermal response, high temperature control accuracy, and long life. Below is a detailed explanation of the key points.
Key Points Explained:
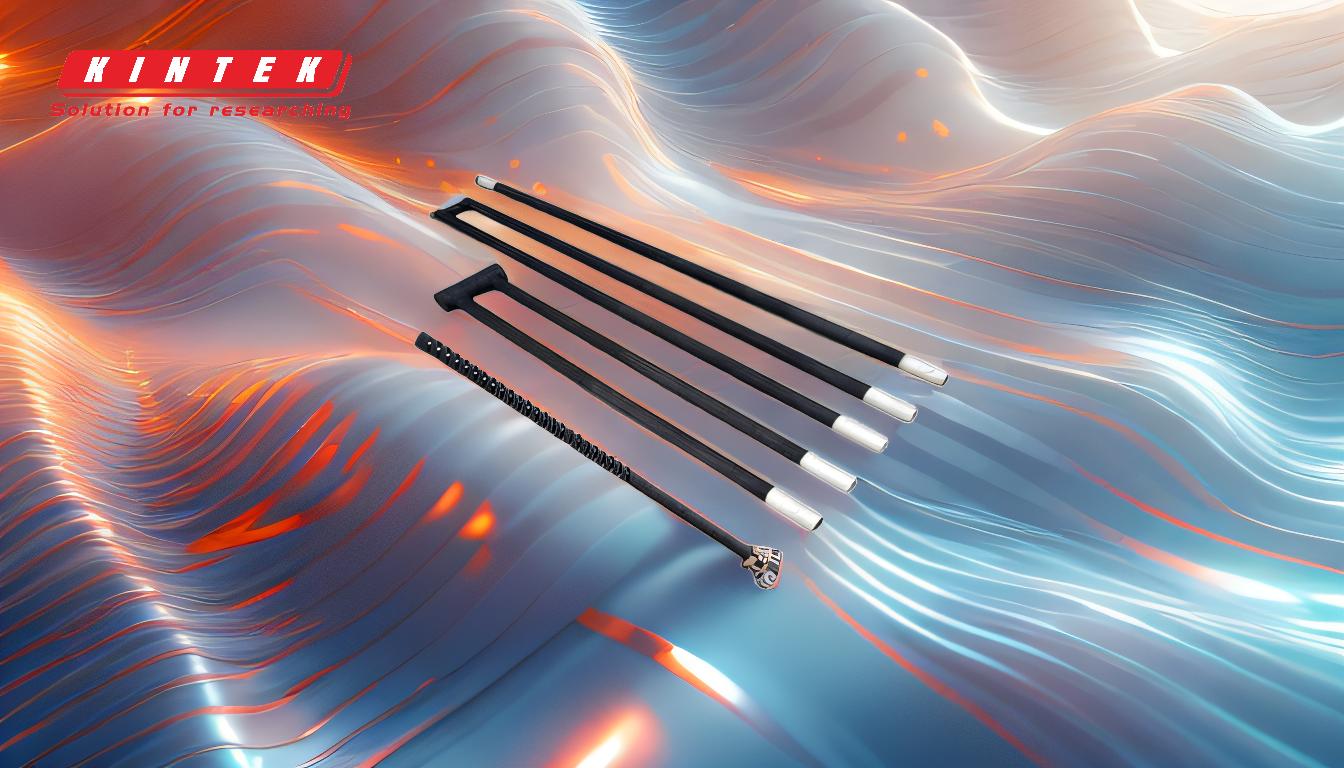
-
Ceramic Heaters: The Most Efficient Heating Element
- Ceramic heaters are highly energy-efficient, converting 96% of their input power into heat. This makes them one of the most efficient heating elements available.
- They can operate at temperatures up to 700°C, making them suitable for high-temperature applications.
- Their efficiency is attributed to the ceramic material's ability to retain and distribute heat evenly, reducing energy waste.
- Ceramic heaters are often used in industrial and domestic applications where precision and energy efficiency are critical.
-
Stainless Steel Heating Elements: High Efficiency and Versatility
- Stainless steel heating elements are known for their fast thermal response and high temperature control accuracy, which contribute to their efficiency.
- They have a high thermal conversion efficiency, meaning they convert a large portion of electrical energy into heat with minimal losses.
- These elements are lightweight, easy to disassemble, and have a simple structure, making them cost-effective and easy to maintain.
- Their ability to be bent into various shapes and their long service life make them adaptable to a wide range of applications.
-
Material Considerations for Efficiency
- Metallic Materials: Materials like molybdenum, tungsten, tantalum, and nickel-chromium alloy are commonly used in heating elements due to their high melting points and resistance to oxidation. These materials are efficient but may not match the energy conversion rates of ceramic heaters.
- Non-Metallic Materials: Graphite, silicon carbide, and molybdenum dioxide are used in specialized applications. While they offer high-temperature capabilities, their efficiency is generally lower compared to ceramic and stainless steel elements.
-
Application-Specific Efficiency
- The efficiency of a heating element also depends on its application. For example:
- Ceramic heaters are ideal for applications requiring precise temperature control and high energy efficiency, such as in industrial ovens or space heaters.
- Stainless steel heating elements are better suited for applications requiring durability and versatility, such as in water heaters or industrial furnaces.
- The efficiency of a heating element also depends on its application. For example:
-
Energy Efficiency and Cost-Effectiveness
- While ceramic heaters are the most energy-efficient, stainless steel heating elements offer a balance between efficiency, cost, and durability.
- The choice of heating element should consider not only energy efficiency but also factors like initial cost, maintenance requirements, and lifespan.
-
Environmental Impact
- Efficient heating elements like ceramic and stainless steel contribute to energy conservation and reduced environmental impact by minimizing energy waste.
- Their long lifespan and reliability also reduce the need for frequent replacements, further lowering their environmental footprint.
In summary, ceramic heaters are the most efficient heating elements due to their high energy conversion rate and suitability for high-temperature applications. However, stainless steel heating elements are also highly efficient and offer additional benefits like versatility and durability. The choice of heating element should be based on the specific requirements of the application, balancing efficiency, cost, and performance.
Summary Table:
Heating Element | Efficiency | Key Features | Applications |
---|---|---|---|
Ceramic Heaters | 96% energy conversion | High-temperature operation (up to 700°C), even heat distribution | Industrial ovens, space heaters |
Stainless Steel | High thermal conversion | Fast thermal response, lightweight, durable | Water heaters, industrial furnaces |
Metallic Materials | Moderate efficiency | High melting points, oxidation resistance | Specialized high-temperature applications |
Non-Metallic Materials | Lower efficiency | High-temperature capabilities | Specialized industrial uses |
Need help choosing the right heating element for your application? Contact our experts today for personalized advice!