Quenching steel is a critical process in metallurgy that involves rapidly cooling the metal to achieve desired mechanical properties, such as increased hardness and strength. However, this process can also introduce several negative effects, including internal stresses, distortion, cracking, and reduced toughness. Understanding these drawbacks is essential for optimizing the quenching process and ensuring the quality of the final product.
Key Points Explained:
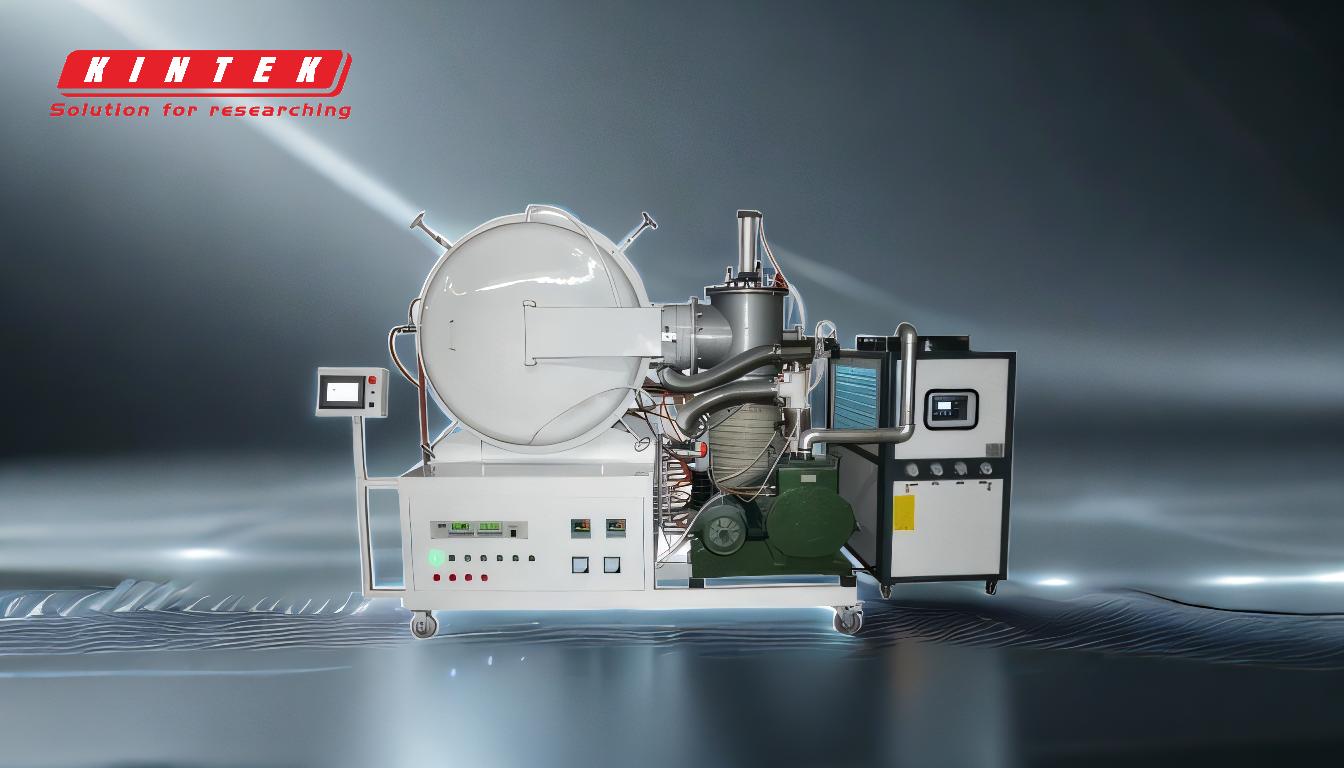
-
Internal Stresses and Distortion:
- Quenching introduces significant thermal gradients within the steel, leading to uneven cooling rates. This can cause internal stresses that may result in distortion or warping of the metal. These stresses can be particularly problematic in complex geometries, where uneven cooling is more likely to occur.
- Distortion can affect the dimensional accuracy of the final product, requiring additional machining or corrective processes, which increases production costs and time.
-
Cracking:
- Rapid cooling can cause the steel to become brittle, especially if the cooling rate is too high or if the steel has a high carbon content. This brittleness can lead to the formation of cracks, which compromise the structural integrity of the material.
- Cracking is more likely to occur in thicker sections of the steel, where the cooling rate is less uniform, or in steels with high hardenability, which are more prone to internal stresses.
-
Reduced Toughness:
- While quenching increases hardness, it often reduces the toughness of the steel. Toughness is the ability of a material to absorb energy and deform plastically before fracturing. A reduction in toughness can make the steel more susceptible to impact failure, especially in applications where the material is subjected to dynamic loading.
- To mitigate this, a tempering process is often applied after quenching to restore some of the lost toughness while maintaining the desired hardness.
-
Residual Stress:
- Quenching can leave residual stresses within the steel, which may not be immediately apparent but can lead to long-term issues such as stress corrosion cracking or premature failure under cyclic loading.
- Techniques such as stress-relief annealing or shot peening are often employed to reduce these residual stresses, but they add complexity and cost to the manufacturing process.
-
Surface Oxidation and Decarburization:
- In some quenching processes, especially those conducted in non-inert atmospheres, the steel may be exposed to oxygen, leading to surface oxidation or decarburization. This can weaken the surface layer, reducing the overall strength and durability of the material.
- Vacuum quenching or the use of protective atmospheres can help mitigate this issue, but these methods require specialized equipment, such as an mpcvd system, which may not be readily available in all facilities.
-
Microstructural Changes:
- Quenching can lead to the formation of undesirable microstructures, such as martensite, which, while hard, can be brittle. In some cases, retained austenite may also be present, which can reduce the overall hardness and stability of the material.
- Proper heat treatment cycles, including controlled cooling rates and subsequent tempering, are necessary to achieve the desired microstructure and balance of properties.
In summary, while quenching is essential for achieving the desired mechanical properties in steel, it is not without its challenges. The process can introduce internal stresses, distortion, cracking, and reduced toughness, all of which must be carefully managed to ensure the quality and performance of the final product. Advanced techniques and equipment, such as vacuum quenching or protective atmosphere systems, can help mitigate some of these issues, but they often come with increased costs and complexity.
Summary Table:
Negative Effect | Description | Mitigation Strategies |
---|---|---|
Internal Stresses | Uneven cooling causes distortion or warping, especially in complex geometries. | Use stress-relief annealing or shot peening to reduce residual stresses. |
Cracking | Rapid cooling leads to brittleness, especially in high-carbon or thick sections. | Control cooling rates and use tempering to restore toughness. |
Reduced Toughness | Quenching increases hardness but decreases toughness. | Apply tempering to balance hardness and toughness. |
Residual Stress | Long-term stresses can cause premature failure. | Employ stress-relief techniques like annealing. |
Surface Oxidation | Exposure to oxygen weakens the surface layer. | Use vacuum quenching or protective atmospheres. |
Microstructural Changes | Formation of brittle martensite or retained austenite. | Optimize heat treatment cycles with controlled cooling and tempering. |
Need expert advice on optimizing your steel quenching process? Contact us today to learn more!