The normal temperature for sintering varies depending on the material being processed and the desired properties of the final product. For zirconia, sintering typically occurs at temperatures closer to 1,500°C, although the transformation from monoclinic to polytetragonal structure happens around 1,100°C to 1,200°C. Higher temperatures result in denser zirconia, often reaching close to 99% of the theoretical maximum density. For ceramic composites, sintering temperatures range between 900°C and 1250°C. In dental applications, sintering furnaces usually operate at high temperatures, typically ranging from 1200°C to 1400°C. The sintering process is critical, and factors such as ramp rate, temperature consistency during hold time, and cooling rate are essential for achieving optimal results.
Key Points Explained:
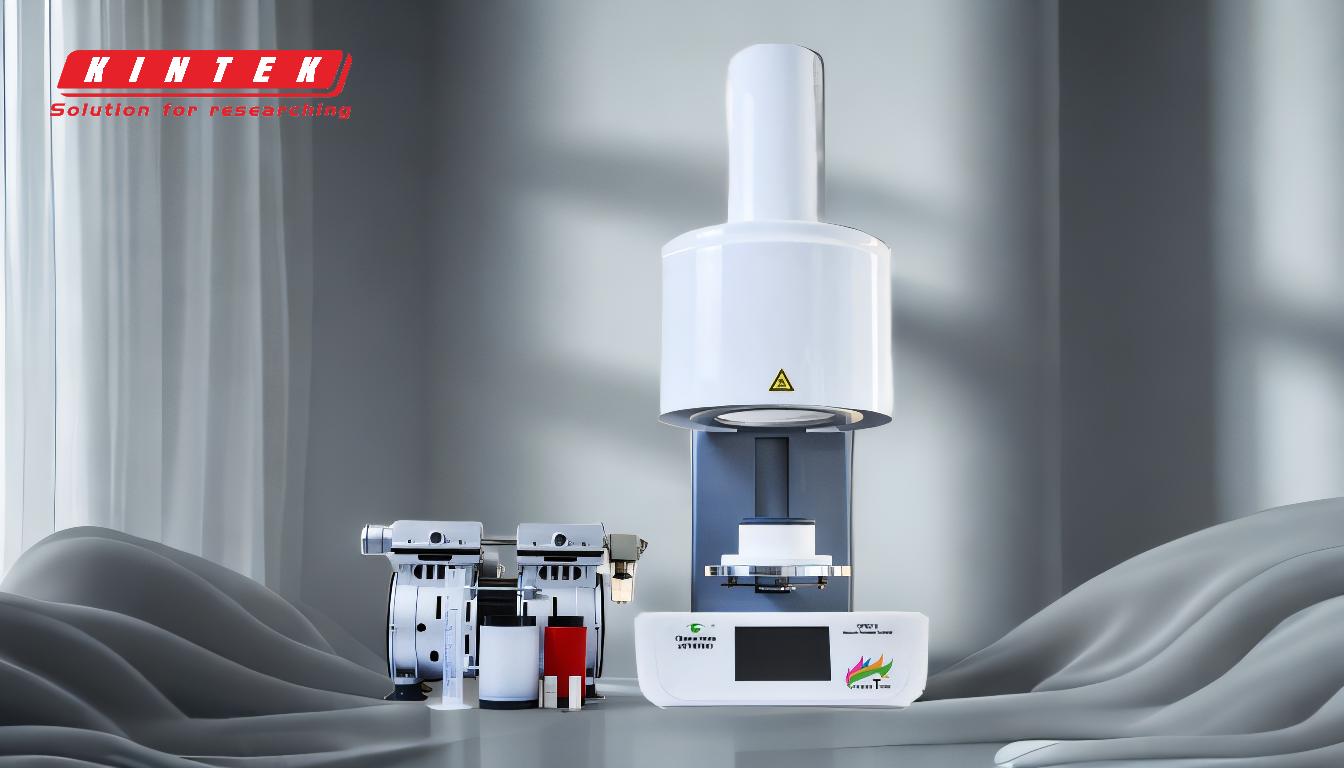
-
Temperature Range for Zirconia Sintering:
- Zirconia sintering typically occurs at temperatures closer to 1,500°C.
- The transformation from monoclinic to polytetragonal structure happens around 1,100°C to 1,200°C.
- Higher sintering temperatures result in denser zirconia, often reaching close to 99% of the theoretical maximum density.
-
Temperature Range for Ceramic Composites:
- Sintering of ceramic composites is conducted at temperatures between 900°C (1650°F) and 1250°C (2300°F).
- This range ensures the material achieves the desired mechanical properties and density.
-
Dental Sintering Furnaces:
- Dental sintering furnaces usually require high temperatures, typically ranging from 1200°C to 1400°C.
- These temperatures are necessary to achieve the required strength and aesthetics for dental restorations.
-
General Sintering Process:
- The sintering process is conducted at elevated temperatures, usually above 1800°F (982°C), depending on the application.
- The process can occur in an inert, reducing, or oxidizing atmosphere, depending on the material and desired characteristics.
-
Critical Factors in Sintering:
- Ramp Rate: The rate at which the temperature increases from 900°C to the top temperature is critical.
- Temperature Consistency: Maintaining a consistent temperature during the hold time is essential for uniform sintering.
- Cooling Rate: The rate of cooling back to about 900°C is crucial to prevent defects and ensure the material's integrity.
-
Standard Sintering Furnaces:
- Standard sintering furnaces can operate at maximum temperatures ranging from 1400°C to 1700°C.
- These furnaces are designed to handle the high temperatures required for sintering various materials.
-
Controlled Atmosphere Sintering:
- Sintering is often carried out in continuous furnaces under controlled speed and in an atmosphere with a controlled chemical composition.
- The temperature typically ranges between 750°C and 1300°C, depending on the material and desired characteristics.
By understanding these key points, one can better appreciate the complexities and critical factors involved in the sintering process, ensuring the production of high-quality materials with the desired properties.
Summary Table:
Material/Application | Temperature Range (°C) | Key Characteristics |
---|---|---|
Zirconia Sintering | ~1,500°C | Denser zirconia, ~99% theoretical density |
Ceramic Composites | 900°C - 1,250°C | Desired mechanical properties and density |
Dental Sintering Furnaces | 1,200°C - 1,400°C | Required strength and aesthetics for dental restorations |
General Sintering Process | >982°C (1,800°F) | Inert, reducing, or oxidizing atmosphere |
Critical Factors | Ramp rate, consistency, cooling rate | Ensures uniform sintering and material integrity |
Standard Sintering Furnaces | 1,400°C - 1,700°C | Handles high temperatures for various materials |
Controlled Atmosphere | 750°C - 1,300°C | Controlled speed and chemical composition |
Need help optimizing your sintering process? Contact our experts today for tailored solutions!