Tempering is a critical step in the heat treatment process, primarily aimed at reducing brittleness and internal stresses in hardened steel caused by rapid cooling during quenching. By heating the material to a temperature below its transformation range and then cooling it, tempering achieves desired changes in mechanical properties such as increased ductility, toughness, and grain size. This process also helps form specific microstructures like troostite or sorbite, which balance strength and ductility. Overall, tempering ensures that the material retains hardness while becoming less prone to cracking or failure under stress.
Key Points Explained:
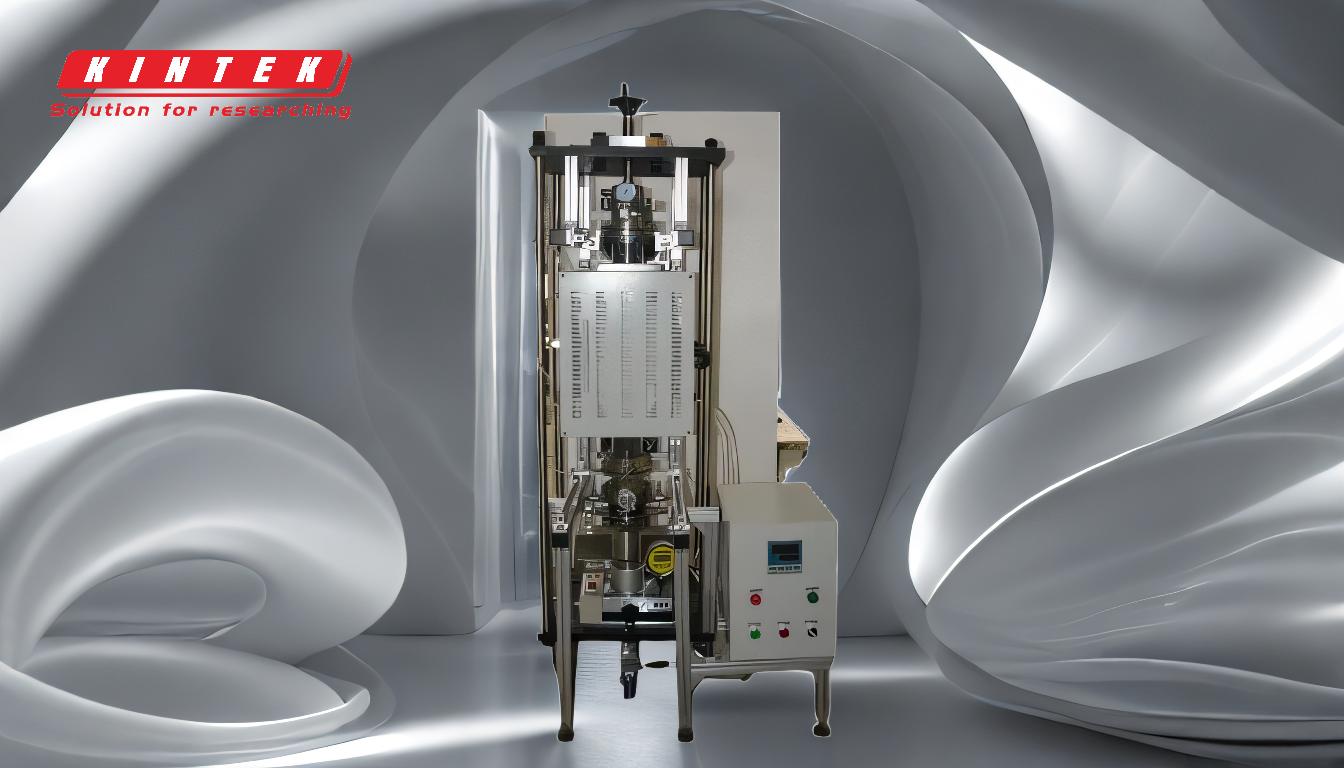
-
Reduction of Brittleness:
- Tempering is essential to reduce the brittleness of hardened steel. After quenching, steel becomes extremely hard but also brittle, making it prone to cracking or breaking under stress. Tempering softens the steel slightly, improving its toughness and making it more suitable for practical applications.
-
Removal of Internal Stresses:
- Rapid cooling during quenching introduces internal strains and stresses in the material. Tempering relieves these stresses by allowing the material to undergo controlled heating and cooling, which helps stabilize its internal structure and prevent distortion or failure.
-
Enhancement of Ductility and Toughness:
- By heating the steel to a specific temperature below its transformation range, tempering improves ductility (the ability to deform without breaking) and toughness (the ability to absorb energy without fracturing). This makes the material more durable and less likely to fail under impact or load.
-
Formation of Desired Microstructures:
- Tempering facilitates the formation of specific microstructures like troostite and sorbite. Troostite is softer and tougher, while sorbite is weaker but more ductile. These structures help balance the material's mechanical properties, ensuring it meets the required performance criteria.
-
Control of Grain Size:
- Tempering can increase the grain size of the material, which contributes to improved ductility and toughness. Larger grains reduce the likelihood of crack propagation, enhancing the material's overall durability.
-
Temperature and Cooling Control:
- The tempering process involves precise control of heating and cooling. The material is heated to a temperature below its transformation range and then cooled at a controlled rate. This ensures the desired changes in properties are achieved without compromising the material's integrity.
-
Balancing Hardness and Ductility:
- One of the primary objectives of tempering is to strike a balance between hardness and ductility. While quenching maximizes hardness, tempering adjusts this hardness to a level that provides sufficient toughness for practical use, ensuring the material is neither too brittle nor too soft.
-
Application-Specific Adjustments:
- The tempering process can be tailored to meet specific application requirements. For example, tools that require high hardness but moderate toughness may undergo low-temperature tempering, while components needing higher toughness may be tempered at higher temperatures.
By addressing these key points, tempering ensures that heat-treated metals achieve the optimal combination of mechanical properties, making them suitable for a wide range of industrial and engineering applications.
Summary Table:
Key Aspect | Description |
---|---|
Reduction of Brittleness | Softens hardened steel, improving toughness and reducing cracking risks. |
Removal of Internal Stresses | Relieves stresses from quenching, stabilizing the material's internal structure. |
Enhanced Ductility & Toughness | Increases material's ability to deform and absorb energy without fracturing. |
Formation of Microstructures | Creates troostite or sorbite to balance strength and ductility. |
Control of Grain Size | Increases grain size, enhancing durability and reducing crack propagation. |
Temperature & Cooling Control | Ensures precise heating and cooling for optimal property adjustments. |
Balancing Hardness & Ductility | Adjusts hardness to provide toughness without compromising strength. |
Application-Specific Adjustments | Tailors tempering to meet specific industrial or engineering needs. |
Optimize your heat treatment process with expert tempering solutions—contact us today!