The Physical Vapour Deposition (PVD) method is a widely used technique for synthesizing nanoparticles, thin films, and coatings. It involves the vaporization of a solid material in a vacuum environment, followed by the condensation of the vapor onto a substrate to form nanoparticles or thin films. PVD is a versatile and precise method, offering control over particle size, morphology, and composition. It is commonly used in industries such as electronics, optics, and materials science due to its ability to produce high-quality, uniform nanoparticles with minimal contamination. The process typically includes steps like evaporation, transportation, and deposition, and can be tailored to achieve specific material properties.
Key Points Explained:
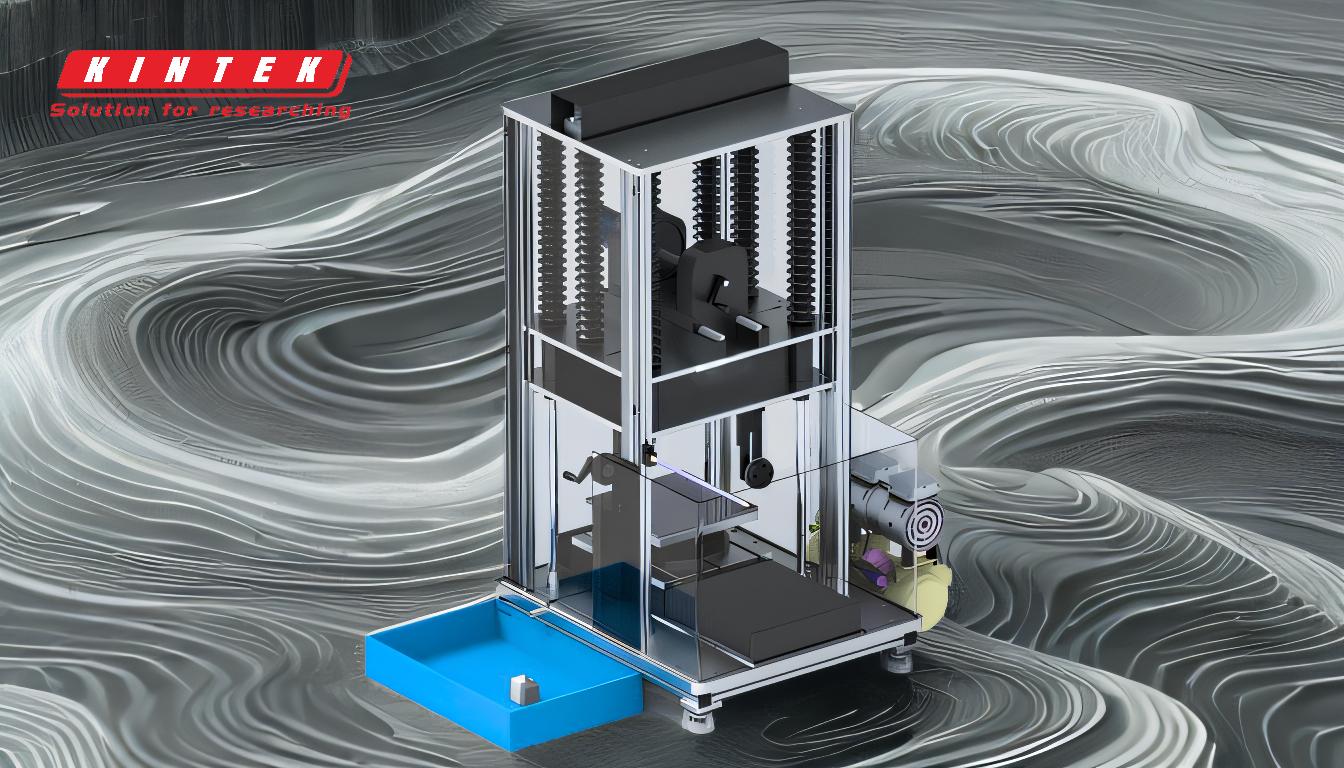
-
Overview of PVD Method:
- Physical Vapour Deposition (PVD) is a process where a solid material is vaporized in a vacuum and then deposited onto a substrate to form nanoparticles or thin films.
- It is a clean and efficient method for synthesizing high-purity nanoparticles with controlled properties.
-
Key Steps in PVD:
- Evaporation: The target material is vaporized using techniques such as thermal evaporation, electron beam evaporation, or sputtering.
- Transportation: The vaporized atoms or molecules travel through the vacuum chamber to the substrate.
- Deposition: The vapor condenses on the substrate, forming a thin film or nanoparticles.
-
Types of PVD Techniques:
- Thermal Evaporation: The material is heated until it vaporizes. This is suitable for materials with low melting points.
- Electron Beam Evaporation: A focused electron beam is used to vaporize the material, ideal for high-melting-point materials.
- Sputtering: High-energy ions bombard the target material, causing atoms to be ejected and deposited on the substrate.
- Pulsed Laser Deposition (PLD): A laser is used to vaporize the material, providing precise control over deposition.
-
Advantages of PVD:
- High purity of deposited materials due to the vacuum environment.
- Control over particle size, morphology, and film thickness.
- Ability to deposit a wide range of materials, including metals, ceramics, and composites.
- Environmentally friendly, as it typically does not involve harmful chemicals.
-
Applications of PVD:
- Electronics: Used for depositing thin films in semiconductor devices, sensors, and displays.
- Optics: Produces anti-reflective coatings, mirrors, and optical filters.
- Materials Science: Creates wear-resistant and corrosion-resistant coatings.
- Nanotechnology: Synthesizes nanoparticles for catalysis, energy storage, and biomedical applications.
-
Challenges and Considerations:
- High equipment and operational costs due to the need for vacuum systems.
- Limited scalability for large-scale production.
- Requires precise control over process parameters, such as temperature, pressure, and deposition rate.
-
Future Trends in PVD:
- Development of hybrid PVD techniques combining multiple methods for enhanced material properties.
- Integration of PVD with other nanofabrication techniques for advanced applications.
- Focus on improving scalability and reducing costs for industrial adoption.
In summary, the Physical Vapour Deposition method is a powerful and versatile technique for nanoparticle synthesis, offering precise control over material properties and applications across various industries. Its ability to produce high-quality, contamination-free materials makes it a preferred choice for advanced material fabrication.
Summary Table:
Aspect | Details |
---|---|
Process Overview | Vaporization of solid material in a vacuum, followed by deposition. |
Key Steps | Evaporation, Transportation, Deposition |
Techniques | Thermal Evaporation, Electron Beam Evaporation, Sputtering, PLD |
Advantages | High purity, precise control, wide material range, eco-friendly |
Applications | Electronics, Optics, Materials Science, Nanotechnology |
Challenges | High costs, limited scalability, precise parameter control required |
Future Trends | Hybrid techniques, integration with nanofabrication, improved scalability |
Discover how PVD can revolutionize your nanoparticle synthesis—contact our experts today for tailored solutions!