A plasma source is a device or system that generates plasma, which is an ionized gas consisting of free electrons and ions. Plasma sources are widely used in various industrial and scientific applications, including semiconductor manufacturing, surface treatment, and material deposition. Traditional plasma sources are often designed for specific processes, such as etching, ion-assisted deposition, or plasma-enhanced chemical vapor deposition (PECVD). However, these sources are typically limited in their scalability and versatility due to the physical constraints of their design and operation. Modern advancements aim to overcome these limitations by developing more flexible and scalable plasma sources.
Key Points Explained:
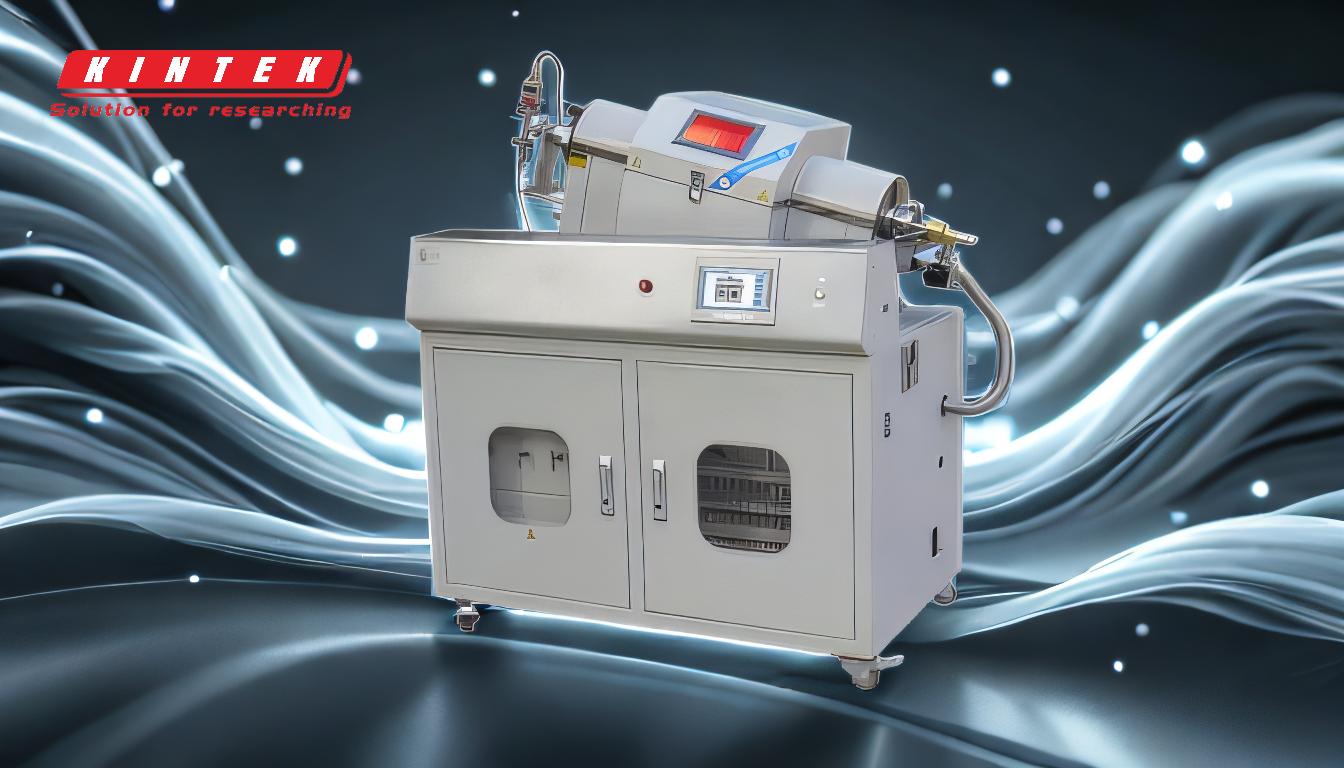
-
Definition of Plasma Source:
- A plasma source is a device that generates plasma, a state of matter where gas is ionized to produce free electrons and ions. This ionized gas is highly reactive and can be used in various industrial processes, including material processing, surface modification, and thin-film deposition.
-
Types of Plasma Sources:
- Traditional Plasma Sources: These include devices like capacitively coupled plasma (CCP) sources, inductively coupled plasma (ICP) sources, and microwave plasma sources. Each type is often optimized for specific applications, such as etching or deposition.
- Modern Plasma Sources: Newer designs aim to be more versatile and scalable, allowing for a broader range of applications and easier integration into different manufacturing processes.
-
Applications of Plasma Sources:
- Etching: Plasma sources are used in semiconductor manufacturing to etch patterns onto silicon wafers. The reactive ions in the plasma can remove material from the wafer surface with high precision.
- Ion-Assisted Deposition: In this process, plasma is used to assist in the deposition of thin films onto substrates. The ions in the plasma help to improve the adhesion and quality of the deposited films.
- Plasma-Enhanced Chemical Vapor Deposition (PECVD): PECVD uses plasma to enhance the chemical reactions that deposit thin films onto substrates. This method is commonly used to deposit silicon dioxide, silicon nitride, and other materials in semiconductor manufacturing.
-
Limitations of Traditional Plasma Sources:
- Process Specificity: Traditional plasma sources are often designed for specific processes, such as etching or deposition. This limits their versatility and makes it difficult to use the same source for multiple applications.
- Scalability Issues: The physical characteristics of traditional plasma sources, such as their size and power requirements, can limit their scalability. This makes it challenging to use them in large-scale manufacturing processes.
-
Advancements in Plasma Source Technology:
- Increased Versatility: Modern plasma sources are being developed to be more versatile, allowing them to be used for a wider range of applications. This includes the ability to switch between different processes, such as etching and deposition, using the same source.
- Improved Scalability: Advances in plasma source design are also addressing scalability issues. Newer sources are being designed to be more compact and energy-efficient, making them suitable for large-scale manufacturing processes.
In summary, plasma sources are critical components in many industrial and scientific applications. While traditional plasma sources are often limited in their versatility and scalability, ongoing advancements in technology are leading to the development of more flexible and scalable plasma sources that can meet the demands of modern manufacturing processes.
Summary Table:
Aspect | Details |
---|---|
Definition | A device generating plasma, an ionized gas with free electrons and ions. |
Types | Traditional (CCP, ICP, microwave) and modern (versatile, scalable) sources. |
Applications | Etching, ion-assisted deposition, PECVD in semiconductor manufacturing. |
Limitations | Process specificity and scalability issues in traditional designs. |
Advancements | Increased versatility and improved scalability in modern designs. |
Learn how plasma sources can revolutionize your processes—contact our experts today!