The pressure for PVD coating is a critical factor that influences the quality and properties of the deposited thin film. PVD (Physical Vapor Deposition) is typically conducted under high-vacuum conditions, often at pressures below 10^-4 Torr, to ensure minimal contamination and optimal deposition conditions. At these low pressures, the process is line-of-sight, meaning that the vaporized material travels directly from the target to the substrate without significant scattering. However, at higher pressures (≥10^-4 Torr), vapor scattering occurs, which can enable the coating of surfaces not directly in the line of sight of the source. The choice of pressure depends on the specific PVD technique used and the desired properties of the coating, such as uniformity, adhesion, and thickness.
Key Points Explained:
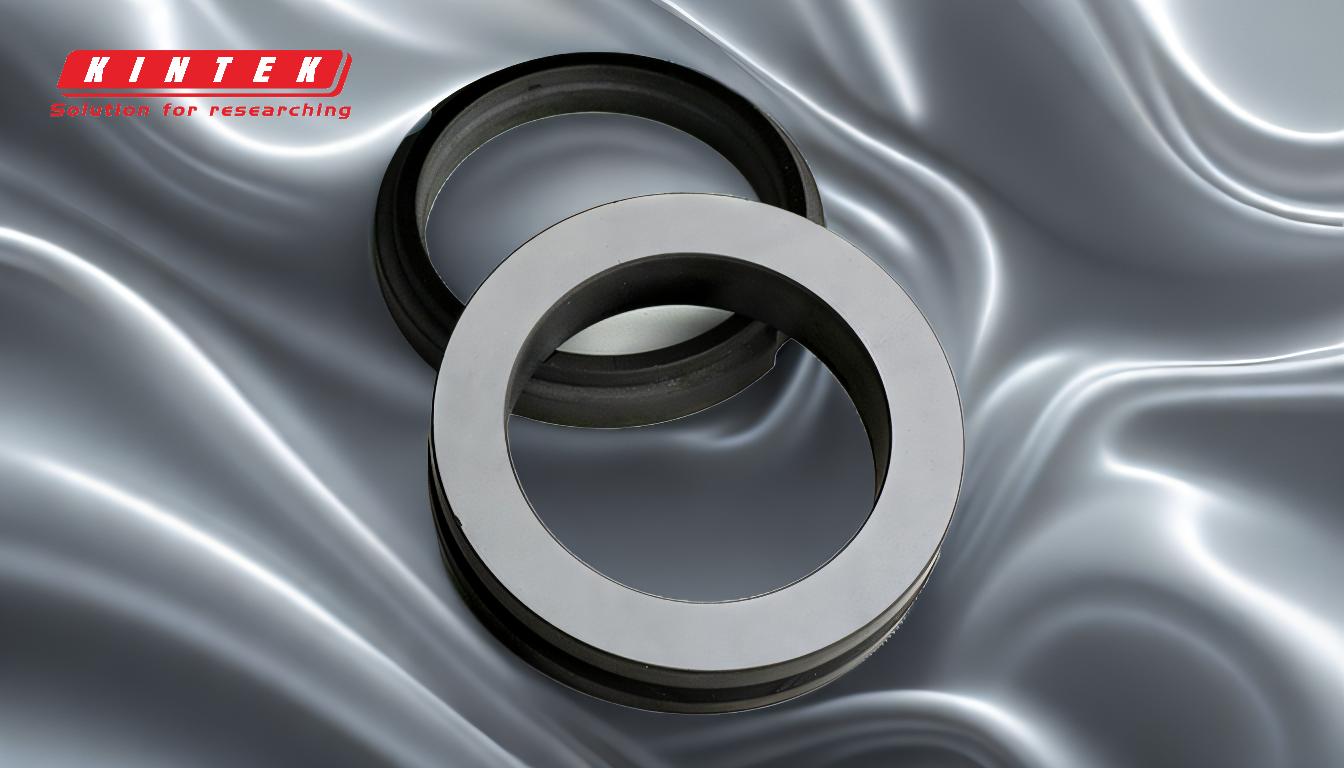
-
High-Vacuum Environment:
- PVD coating is typically performed under high-vacuum conditions, often at pressures below 10^-4 Torr. This low-pressure environment minimizes the presence of contaminants and ensures that the vaporized material can travel directly from the target to the substrate without significant interference from gas molecules.
-
Line-of-Sight Process:
- At low pressures (<10^-4 Torr), PVD is a line-of-sight process. This means that the vaporized material travels in a straight line from the target to the substrate, limiting the ability to coat surfaces that are not directly in the line of sight of the source. This is particularly important for achieving uniform coatings on complex geometries.
-
Vapor Scattering at Higher Pressures:
- At higher pressures (≥10^-4 Torr), significant vapor scattering occurs. This scattering allows the vaporized material to reach surfaces that are not directly in the line of sight of the source, enabling more uniform coating of complex shapes. However, higher pressures can also lead to increased contamination and reduced coating quality.
-
Impact on Coating Properties:
- The pressure during PVD coating directly affects the properties of the deposited film, including its uniformity, adhesion, and thickness. Lower pressures generally result in higher-quality coatings with better adhesion and fewer defects, while higher pressures can improve coverage on complex geometries but may compromise coating quality.
-
Dependence on PVD Technique:
- The optimal pressure for PVD coating can vary depending on the specific technique used. For example, Electron Beam Physical Vapor Deposition (EBPVD) typically requires very low pressures to maintain the line-of-sight nature of the process, while other techniques like sputtering may operate at slightly higher pressures to achieve desired coating properties.
-
Surface Pretreatment and Cleanliness:
- The effectiveness of PVD coating is also influenced by the pretreatment and cleanliness of the substrate. High-vacuum conditions help maintain surface cleanliness, but proper pretreatment is essential to ensure good adhesion and coating quality. Contaminants or trapped air can negatively impact the coating process, especially at lower pressures.
In summary, the pressure for PVD coating is a crucial parameter that affects the deposition process and the quality of the resulting thin film. Operating under high-vacuum conditions (below 10^-4 Torr) is generally preferred for achieving high-quality coatings, but higher pressures may be used to improve coverage on complex geometries. The choice of pressure should be carefully considered based on the specific PVD technique and the desired properties of the coating.
Summary Table:
Parameter | Details |
---|---|
Optimal Pressure | Below 10^-4 Torr (high-vacuum conditions) |
Line-of-Sight Process | Vaporized material travels directly to the substrate at low pressures |
Vapor Scattering | Occurs at higher pressures (≥10^-4 Torr), enabling complex geometry coating |
Impact on Coating Quality | Lower pressure = better adhesion, fewer defects; higher pressure = improved coverage |
PVD Technique Dependence | EBPVD requires very low pressure; sputtering may use slightly higher pressure |
Surface Pretreatment | Cleanliness and pretreatment are critical for optimal coating quality |
Need help optimizing your PVD coating process? Contact our experts today for tailored solutions!