Tube furnaces, particularly those with quartz tubes, operate under specific pressure and temperature constraints to ensure safety and optimal performance. The pressure inside a tube furnace is typically maintained below 0.2 bars (3 psi or 0.02 MPa) when operating under vacuum or low-pressure conditions. This pressure limit is crucial to prevent damage to the quartz tube and ensure the furnace operates safely, especially at temperatures up to 1000°C. Additionally, gas flow rates within the furnace are limited to less than 200 SCCM (200 ml/min) to minimize thermal shocks and maintain consistent heating. The design and operation of a tube furnace are influenced by various factors, including process temperature, throughput, atmosphere requirements, and material characteristics, all of which must be carefully considered to optimize performance and safety.
Key Points Explained:
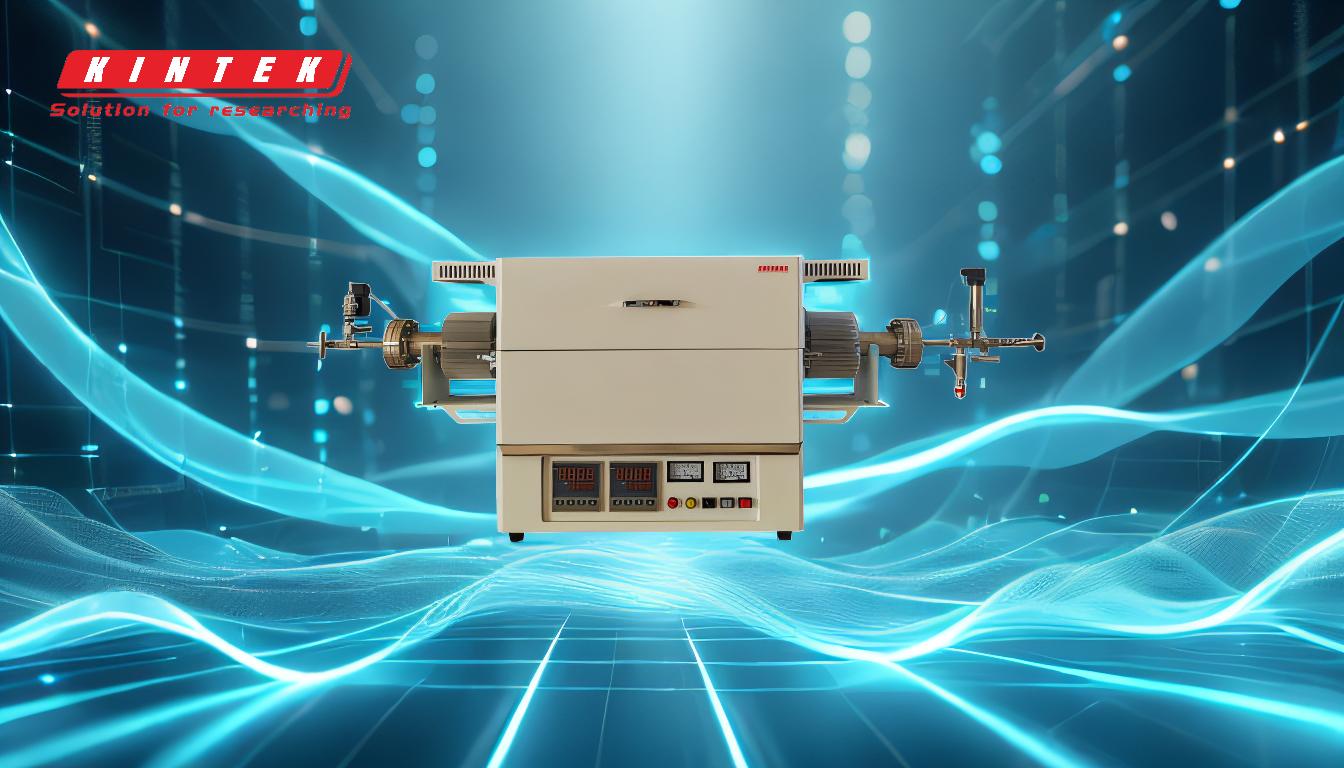
-
Pressure Limits in Tube Furnaces:
- Tube furnaces with quartz tubes are designed to operate under vacuum or low-pressure conditions, typically below 0.2 bars (3 psi or 0.02 MPa).
- This pressure limit is critical to prevent structural damage to the quartz tube, which could compromise the integrity of the furnace.
- Operating under vacuum or low pressure is particularly important when the furnace is used at high temperatures, up to 1000°C, as higher pressures could lead to unsafe conditions or equipment failure.
-
Temperature Constraints:
- The pressure limits are closely tied to the operating temperature of the furnace. For example, vacuum pressure should only be used up to 1000°C to ensure safety.
- Exceeding the recommended temperature or pressure limits can lead to thermal stress on the quartz tube, potentially causing cracks or other damage.
- The furnace should always be used within its rated temperature range to avoid overheating, which could lead to equipment failure or safety hazards.
-
Gas Flow Rate and Thermal Shock:
- The flow rate of gases within the tube furnace is limited to less than 200 SCCM (200 ml/min) to reduce the risk of thermal shocks.
- Thermal shocks occur when rapid temperature changes cause stress on the quartz tube, leading to potential cracking or failure.
- Controlling the gas flow rate helps maintain a stable thermal environment within the furnace, ensuring consistent heating and preventing damage to the tube.
-
Design Considerations for Tube Furnaces:
- The design of a tube furnace varies based on several factors, including process temperature, throughput, atmosphere requirements, material characteristics, and cooling needs.
- For example, multi-zone furnaces require precise control over each zone to ensure consistent temperatures throughout the chamber, which is critical for processes that demand uniform heating.
- Proper insulation and efficient heat transfer mechanisms are also essential design considerations to optimize furnace performance and energy efficiency.
-
Operational Safety and Best Practices:
- Before operating a tube furnace, it is essential to check the sealing of the furnace to ensure no flammable gases or items are present in the working environment.
- Overheating or overloading the furnace should be avoided, as these practices can lead to equipment damage or safety risks.
- The furnace door should not be opened during operation, and the furnace should not be used for experiments involving corrosive materials unless specifically designed for such use.
-
Impact of Gas Flow on Performance:
- The gas flow rate and composition within the furnace can significantly influence reaction efficiency, product yields, and reaction kinetics.
- A higher gas flow rate can help remove reaction byproducts, improving efficiency, while a lower flow rate may result in longer reaction times and higher yields.
- Understanding the relationship between gas flow and furnace performance is crucial for optimizing experimental conditions and achieving desired outcomes.
-
Choosing the Right Tube Furnace:
- The intended use of the tube furnace will determine the most suitable type of furnace. Options range from simple, economical wire-wound single-zone tube furnaces to more advanced systems with multi-zone control.
- Factors such as process temperature, throughput, and atmosphere requirements should be considered when selecting a furnace to ensure it meets the specific needs of the application.
In summary, the pressure inside a tube furnace is a critical parameter that must be carefully controlled to ensure safe and efficient operation. By adhering to pressure and temperature limits, controlling gas flow rates, and following best practices, users can optimize the performance of their tube furnaces while minimizing risks. The design and selection of a tube furnace should be based on the specific requirements of the intended application, taking into account factors such as process temperature, throughput, and material characteristics.
Summary Table:
Parameter | Limit/Constraint | Importance |
---|---|---|
Pressure | Below 0.2 bars (3 psi or 0.02 MPa) | Prevents quartz tube damage and ensures safe operation at high temperatures. |
Temperature | Up to 1000°C | Avoids thermal stress and equipment failure. |
Gas Flow Rate | Less than 200 SCCM (200 ml/min) | Minimizes thermal shocks and maintains consistent heating. |
Design Considerations | Process temperature, throughput, atmosphere, materials | Optimizes performance and safety for specific applications. |
Need help selecting or operating a tube furnace? Contact our experts today for personalized guidance!