A muffle furnace is a critical piece of laboratory equipment designed for high-temperature applications, such as solid-state reactions, metal reduction, and chemical vapor deposition. Its working principle revolves around converting electrical energy into heat through resistance heating, which is then transferred to the sample within the furnace. The furnace's insulated ceramic chamber, known as the muffle, ensures uniform heating and minimizes heat loss. By leveraging thermal convection and radiation, the muffle furnace achieves precise temperature control, making it ideal for experiments requiring high temperatures and isolation from external contaminants.
Key Points Explained:
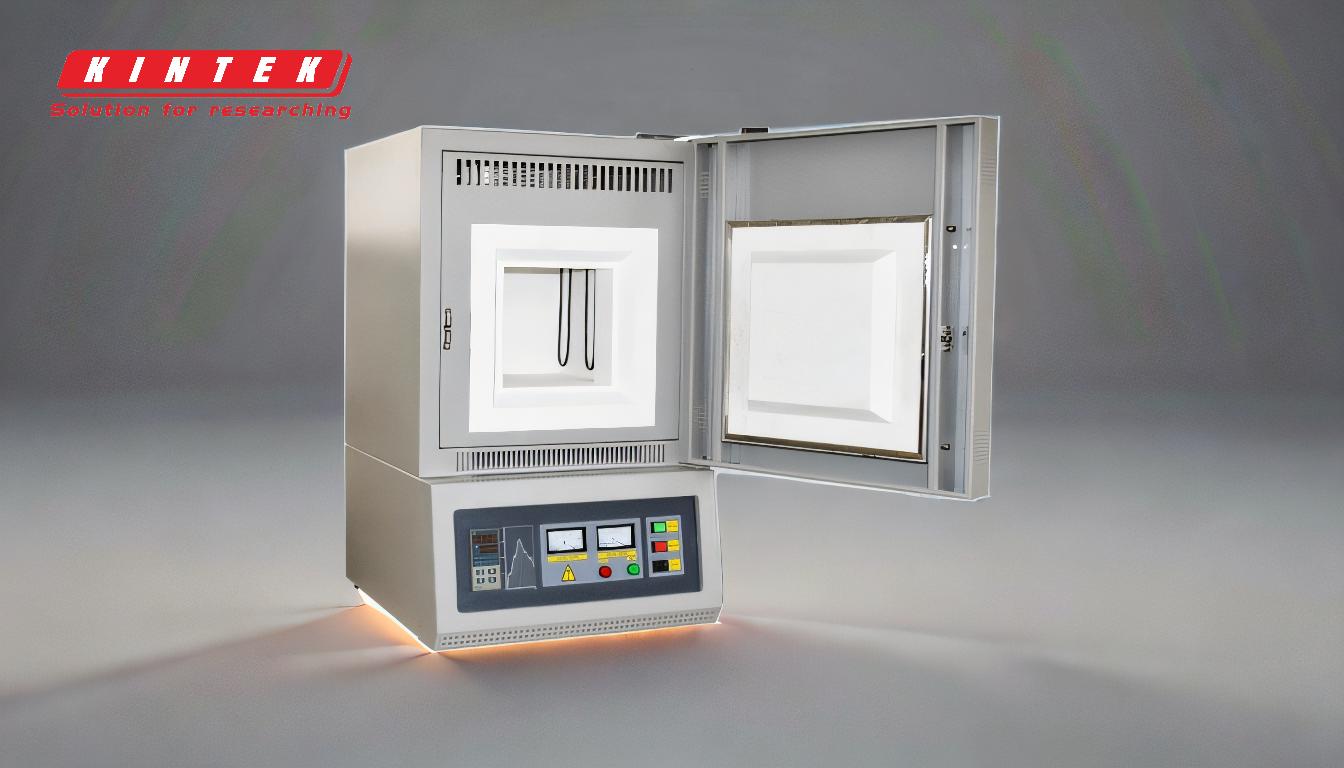
-
Energy Conversion and Heating Mechanism:
- The muffle furnace operates on the principle of converting electrical energy into heat. This is achieved through resistance heating, where electric current passes through a heating element (usually a coil or resistor), generating heat.
- The heat is then transferred to the sample or workpiece placed inside the furnace chamber. This process adheres to the law of conservation of energy, ensuring efficient energy utilization.
-
Role of the Muffle Chamber:
- The muffle furnace features a ceramic chamber, referred to as the "muffle," which is designed to withstand high temperatures and provide a controlled environment for heating.
- The muffle chamber is surrounded by layers of insulation to prevent heat loss, ensuring that the furnace can achieve and maintain the desired high temperatures efficiently.
-
Thermal Convection and Radiation:
- The furnace relies on thermal convection and radiation to heat the air inside the chamber. Thermal convection involves the movement of heated air, while thermal radiation transfers heat directly to the sample.
- These mechanisms ensure uniform heating of the sample, which is crucial for consistent and reproducible experimental results.
-
Isolation from External Contaminants:
- The muffle furnace is designed to isolate the sample from external factors, such as air or contaminants, which could interfere with the heating process. This is particularly important for applications like combustion, where the sample is heated to ash without external interference.
-
Applications in Laboratory Settings:
- Muffle furnaces are widely used in laboratories for processes such as:
- Solid-state reactions (e.g., reducing metals or creating oxides).
- High-temperature chemical vapor deposition (CVD).
- Combustion of samples to determine ash content.
- These applications require precise temperature control and uniform heating, which the muffle furnace provides.
- Muffle furnaces are widely used in laboratories for processes such as:
-
Insulation and Heat Retention:
- The furnace's insulation plays a critical role in maintaining high temperatures. Refractory materials and insulating layers surround the muffle chamber to minimize heat loss and ensure energy efficiency.
- This design allows the furnace to reach and sustain temperatures required for various high-temperature processes.
-
Electrically Powered Operation:
- Unlike traditional furnaces that may use fuel combustion, modern muffle furnaces are electrically powered. This makes them safer and more controllable, as they do not produce combustion byproducts.
- The heating coil, surrounded by insulated material, ensures that the furnace structure remains undamaged even at high temperatures.
-
Precision and Uniformity:
- The muffle furnace is engineered to provide precise temperature control, which is essential for experiments requiring consistent heating.
- The uniform distribution of heat within the chamber ensures that all parts of the sample are heated evenly, reducing the risk of experimental errors.
-
Versatility in High-Temperature Applications:
- The ability to achieve high temperatures makes the muffle furnace versatile for a wide range of applications, including smelting, casting, heat treatment, and material testing.
- Its design allows it to handle various materials and processes, making it a valuable tool in both research and industrial settings.
-
Safety and Isolation Features:
- The closed chamber design of the muffle furnace ensures that high-temperature processes are conducted safely, without exposing the operator to extreme heat or harmful byproducts.
- The isolation of the sample from the external environment also prevents contamination, ensuring the integrity of the experimental results.
In summary, the muffle furnace is a highly efficient and versatile laboratory tool that leverages electrical energy conversion, thermal convection, and radiation to achieve precise and uniform heating. Its insulated ceramic chamber, combined with advanced insulation techniques, ensures high-temperature performance and energy efficiency. These features make it indispensable for a wide range of high-temperature applications in both research and industrial laboratories.
Summary Table:
Key Feature | Description |
---|---|
Energy Conversion | Converts electrical energy into heat via resistance heating. |
Muffle Chamber | Ceramic chamber ensures uniform heating and minimizes heat loss. |
Heating Mechanism | Uses thermal convection and radiation for precise, uniform heating. |
Isolation | Protects samples from external contaminants during high-temperature processes. |
Applications | Solid-state reactions, CVD, combustion, and material testing. |
Insulation | Refractory materials and insulating layers enhance heat retention. |
Safety Features | Electrically powered, closed chamber design ensures operator safety. |
Temperature Control | Provides precise and consistent heating for reproducible results. |
Discover how a muffle furnace can elevate your lab’s capabilities—contact us today for expert advice!