Spark Plasma Sintering (SPS) is an advanced sintering technique that combines pulsed direct electric current with uniaxial pressure to achieve rapid densification of materials. The process involves applying a pulsed DC current through a conductive graphite die and, if applicable, through the material itself. This generates localized high temperatures, plasma, and Joule heating, which activate particle surfaces and promote rapid bonding and densification. SPS allows for significantly lower sintering temperatures, faster heating and cooling rates, and shorter holding times compared to conventional sintering methods. The result is highly dense materials with improved properties, often exceeding 99% density.
Key Points Explained:
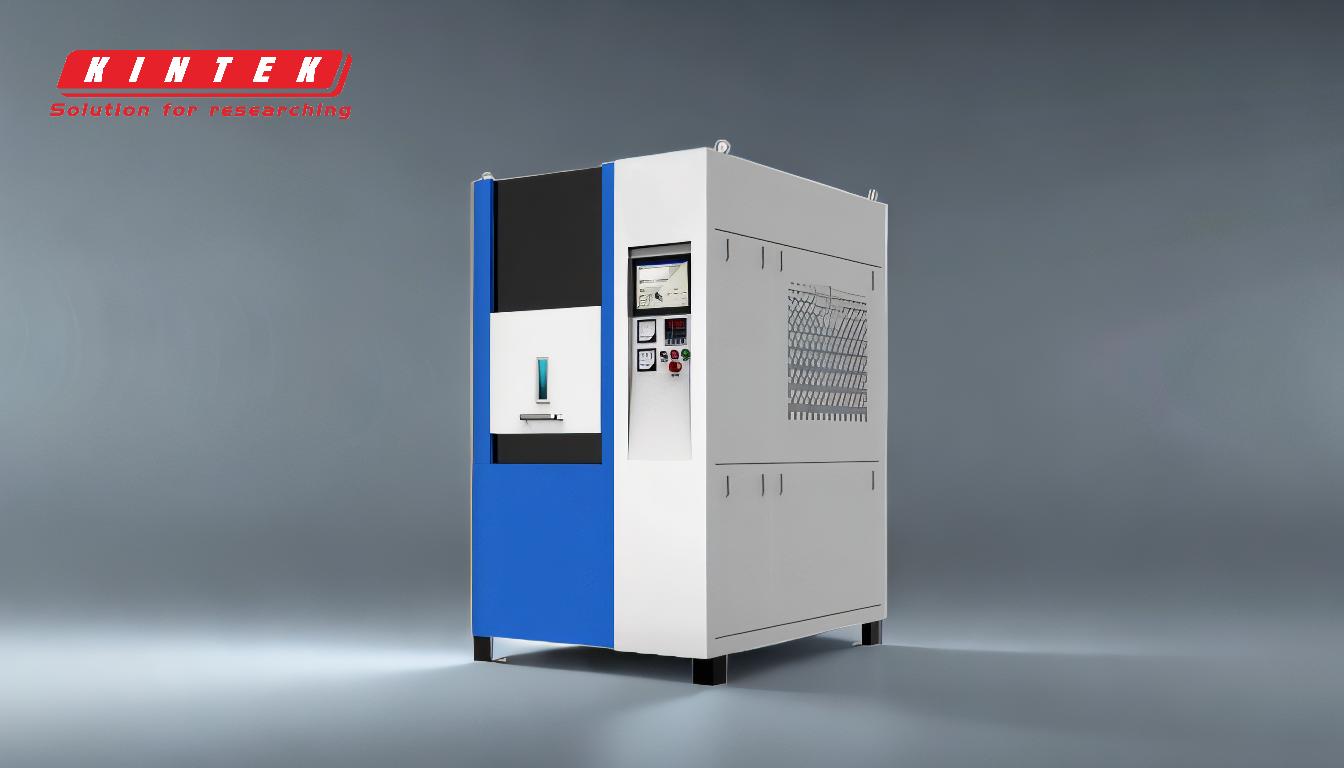
-
Application of Pulsed DC Current:
- SPS utilizes a pulsed direct current (DC) that is applied through a conductive graphite die and, in some cases, directly through the material being sintered.
- The pulsed nature of the current (ON-OFF cycles) generates localized high temperatures and plasma between particles, which enhances surface activation and bonding.
-
Generation of Plasma and High Temperatures:
- The pulsed current creates spark plasma between particles, reaching extremely high temperatures (up to 10,000°C or 18,032°F).
- These high temperatures cause surface contaminants to oxidize or evaporate, while also melting and fusing particle surfaces together, forming "necks" that eventually develop into dense structures.
-
Joule Heating and Uniform Heat Distribution:
- Joule heating occurs as the electric current passes through the material, generating heat uniformly within the sintered body.
- This uniform heating facilitates rapid densification by promoting surface diffusion and boundary defect diffusion, which are critical for the sintering process.
-
Uniaxial Pressure Application:
- In addition to the electric current, uniaxial pressure is applied to the material during the sintering process.
- The combination of pressure and electric current enhances particle bonding and reduces porosity, leading to higher material density.
-
Rapid Densification and Lower Sintering Temperatures:
- SPS allows for rapid heating and cooling rates, as well as shorter holding times compared to conventional sintering methods.
- The process achieves densification at significantly lower temperatures (often hundreds of degrees lower), which helps preserve the material's microstructure and properties.
-
Mechanisms of Particle Bonding:
- The pulsed current generates discharge impact pressure and electric field diffusion, which activate particle surfaces and promote bonding.
- Particle interfaces melt and bond together, forming dense structures with minimal porosity.
-
Alternative Names and Misconceptions:
- Despite the name "Spark Plasma Sintering," research indicates that plasma is not always present in the process.
- Alternative names for the technique include Field Assisted Sintering Technique (FAST), Electric Field Assisted Sintering (EFAS), and Direct Current Sintering (DCS), reflecting the primary role of the electric field in the process.
-
Advantages of SPS:
- High Density: SPS can achieve material densities exceeding 99%, making it ideal for producing high-performance ceramics and metals.
- Efficiency: The rapid heating and cooling rates, combined with lower sintering temperatures, reduce energy consumption and processing time.
- Microstructure Control: The lower temperatures and shorter processing times help preserve fine microstructures, which are often lost in conventional sintering.
-
Applications of SPS:
- SPS is widely used in the production of advanced ceramics, metals, and composites.
- It is particularly valuable for materials that require high density, fine grain size, and enhanced mechanical properties, such as cutting tools, aerospace components, and biomedical implants.
-
Limitations and Considerations:
- The process requires specialized equipment, including a conductive graphite die and a power control device capable of generating pulsed DC currents.
- The high initial cost of SPS equipment may limit its adoption in some industries, though the benefits often outweigh the costs for high-performance applications.
In summary, Spark Plasma Sintering is a highly efficient and effective sintering technique that leverages pulsed DC current, plasma generation, and uniaxial pressure to achieve rapid densification of materials at lower temperatures. Its ability to produce dense, high-performance materials with fine microstructures makes it a valuable tool in advanced manufacturing and materials science.
Summary Table:
Key Aspect | Description |
---|---|
Pulsed DC Current | Generates localized high temperatures and plasma for enhanced particle bonding. |
Plasma & High Temperatures | Reaches up to 10,000°C, melting and fusing particle surfaces for densification. |
Joule Heating | Ensures uniform heat distribution for rapid densification. |
Uniaxial Pressure | Enhances particle bonding and reduces porosity. |
Advantages | High density (>99%), efficiency, and fine microstructure control. |
Applications | Advanced ceramics, metals, composites, aerospace, and biomedical implants. |
Limitations | Requires specialized equipment and has high initial costs. |
Learn how Spark Plasma Sintering can revolutionize your material production—contact us today!