Brazing is a precise and versatile joining process used to bond two or more metal parts using a filler material with a lower melting point than the base materials. The process involves several critical steps, including joint preparation, cleaning, assembly, heating, and cooling. The filler material melts and flows into the joint via capillary action, creating a strong bond upon cooling. Brazing is widely used in industries requiring high precision, minimal deformation, and aesthetically pleasing joints, such as in the production of carbide tools and printed circuit boards. The process can be performed in various environments, including furnaces, vacuum chambers, and controlled atmospheres, each with specific steps to ensure optimal results.
Key Points Explained:
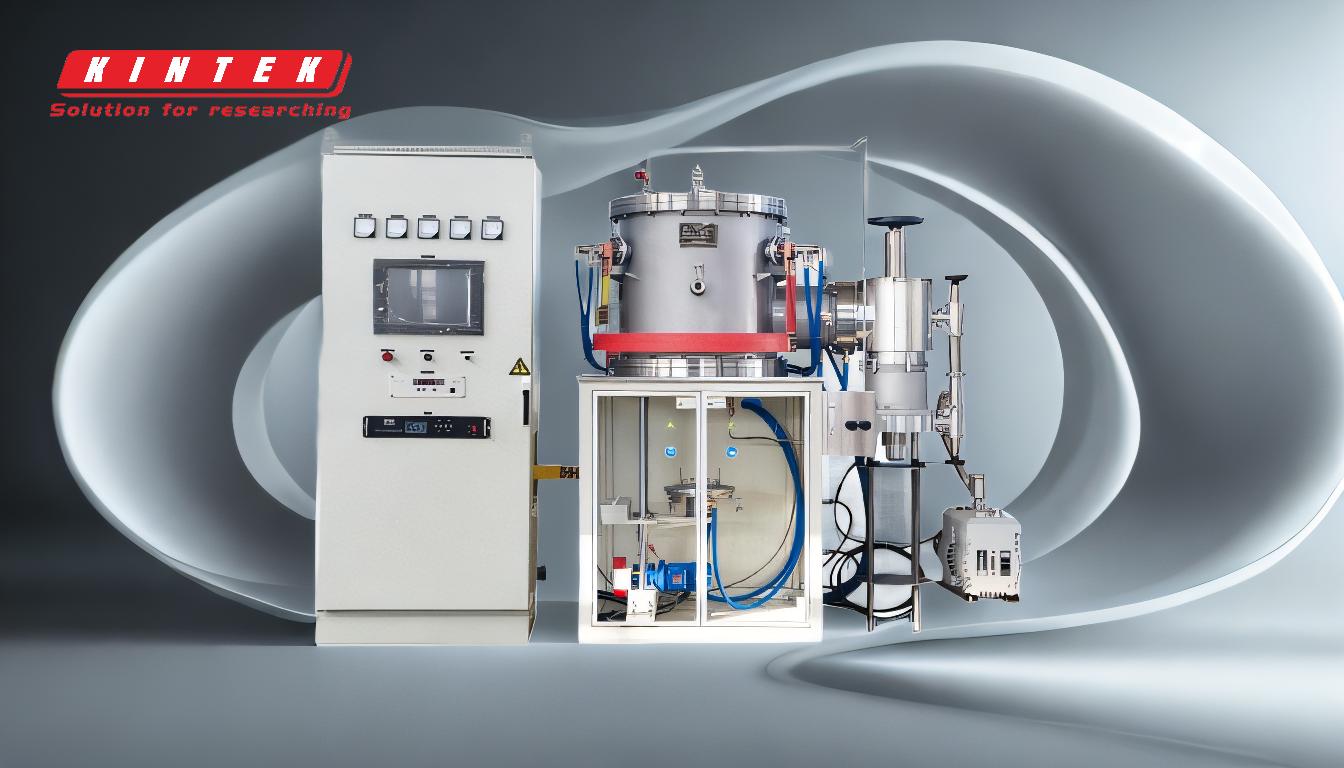
-
Understanding the Brazing Process:
- Brazing involves joining two or more metal parts using a filler material with a lower melting point than the base materials.
- The filler material melts and flows into the joint by capillary action, creating a strong bond upon cooling.
- This method is suitable for joining similar or dissimilar materials, including metals and ceramics.
-
Key Steps in Brazing:
- Joint Preparation: Ensure proper fit and alignment of the parts to allow the filler material to flow smoothly.
- Cleaning: Remove contaminants such as oils, oxides, and dirt from the metal surfaces to ensure a strong bond.
- Assembly: Use clamps or fixtures to hold the parts in precise alignment during the brazing process.
- Heating: Heat the assembly to a temperature above the liquidus temperature of the filler material but below the solidus temperature of the base materials.
- Cooling: Allow the assembly to cool, solidifying the filler material and creating a strong joint.
-
Types of Brazing Processes:
- Furnace Brazing: The entire assembly is heated in a furnace, allowing the filler material to melt and flow into the joint. This method is efficient for mass production.
- Vacuum Brazing: Conducted in a vacuum environment to prevent oxidation, this method is ideal for materials sensitive to atmospheric contamination.
- Controlled Atmosphere Brazing: Uses a controlled atmosphere (e.g., nitrogen or hydrogen) to prevent oxidation and ensure a clean joint.
-
Temperature Control and Phases:
- Brazing involves precise temperature control to ensure the filler material melts and flows properly without damaging the base materials.
- The process can be divided into phases:
- Initial Heating: Cracks the oxide layer on the base material.
- Flux Melting: Breaks down the oxide layer to allow the filler material to flow.
- Filler Melting: The filler material melts and flows into the joint.
- Cooling: The filler solidifies, forming a strong bond.
-
Applications and Advantages:
- Brazing is ideal for joining precision, complex, and multi-material components.
- It produces minimal deformation and smooth, aesthetically pleasing joints.
- Common applications include carbide tools, printed circuit boards, and aerospace components.
-
Equipment and Consumables:
- Brazing Furnaces: Provide controlled heating environments for consistent results.
- Filler Materials: Alloys with specific melting points tailored to the base materials.
- Fluxes: Used to clean and protect the joint area during heating.
- Clamps and Fixtures: Ensure precise alignment and stability during the brazing process.
By following these steps and understanding the nuances of each brazing method, manufacturers can achieve strong, reliable, and high-quality joints suitable for a wide range of applications.
Summary Table:
Key Aspect | Details |
---|---|
Process Overview | Joins metal parts using a filler material with a lower melting point. |
Key Steps | Joint prep, cleaning, assembly, heating, cooling. |
Types of Brazing | Furnace, vacuum, controlled atmosphere. |
Temperature Control | Precise heating phases to melt filler without damaging base materials. |
Applications | Carbide tools, printed circuit boards, aerospace components. |
Equipment | Brazing furnaces, filler materials, fluxes, clamps, and fixtures. |
Ready to achieve precision metal joints with brazing? Contact our experts today for tailored solutions!