The process of CVD (Chemical Vapor Deposition) diamond coating involves several critical steps, including substrate preparation, gas introduction, and energizing the gases to form a diamond layer. The substrate, often made of materials like cemented tungsten-carbide or ceramics, must be meticulously prepared and cleaned. A mixture of gases, primarily methane and hydrogen, is introduced into a chamber and energized using methods like microwaves or hot filaments. This process results in the deposition of a high-quality diamond film, which is evaluated using techniques such as Raman spectroscopy and scanning electron microscopy. The CVD method allows for precise control over the diamond's properties, making it suitable for applications like cvd diamond domes.
Key Points Explained:
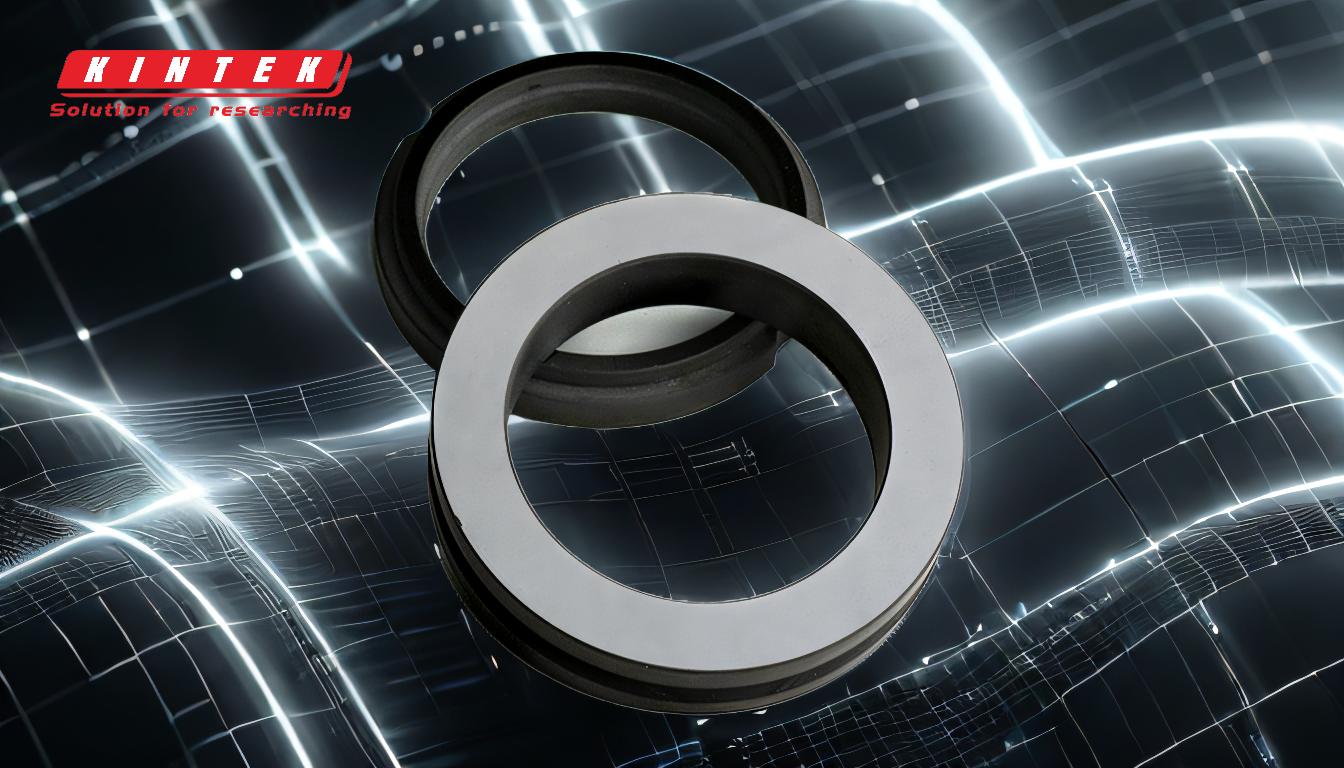
-
Substrate Preparation:
- The substrate material is chosen based on its compatibility with the CVD process, often using cemented tungsten-carbide or ceramics.
- The substrate is cleaned, typically with diamond powder, to ensure proper adhesion of the diamond film.
- The substrate temperature is optimized to around 800 °C (1,470 °F) to facilitate diamond growth.
-
Gas Introduction:
- A mixture of gases, primarily methane (as the carbon source) and hydrogen, is introduced into the chamber.
- The gas ratio is typically 1:99 (methane to hydrogen), with hydrogen playing a crucial role in etching non-diamond carbon.
-
Energizing the Gases:
- The gases are ionized into chemically active radicals using methods such as microwave power, hot filaments, or lasers.
- This energization process initiates the chemical reactions necessary for diamond formation.
-
Chemical Reactions:
- Key reactions include the cracking of hydrogen and methane, leading to the formation of reactive carbon groups.
- These groups interact with the substrate to form carbon-carbon bonds, resulting in diamond film deposition.
-
Diamond Growth:
- The diamond grows layer by layer on the substrate, with hydrogen selectively etching away non-diamond carbon.
- The process allows for fine control over the diamond's properties, including its purity and stress levels.
-
Quality Evaluation:
- Techniques like Raman spectroscopy, X-ray diffraction, and scanning electron microscopy are used to evaluate the diamond film's quality.
- These methods assess the film's structure, purity, morphology, and bonding strength.
-
Applications:
- The CVD diamond coating process is used in various applications, including cutting tools, optical components, and cvd diamond domes.
- The ability to grow diamonds over large areas and on various substrates makes CVD a versatile and valuable technique.
By following these steps, the CVD diamond coating process produces high-quality diamond films with precise control over their properties, making it suitable for a wide range of industrial and scientific applications.
Summary Table:
Step | Description |
---|---|
Substrate Preparation | Substrate (e.g., tungsten-carbide or ceramics) is cleaned and heated to ~800°C. |
Gas Introduction | Methane and hydrogen (1:99 ratio) are introduced into the chamber. |
Energizing the Gases | Gases are ionized using microwaves, hot filaments, or lasers. |
Chemical Reactions | Reactive carbon groups form, leading to diamond film deposition. |
Diamond Growth | Diamond grows layer by layer, with hydrogen etching non-diamond carbon. |
Quality Evaluation | Techniques like Raman spectroscopy and SEM assess film quality. |
Applications | Used in cutting tools, optical components, and CVD diamond domes. |
Discover how CVD diamond coating can enhance your applications—contact us today for expert guidance!