An induction furnace is a highly efficient and clean method for melting metals, widely used in metal casting and foundry operations. The process involves generating an electromagnetic field using an alternating current passed through a hollow copper coil. This field induces eddy currents within the conductive metal charge, which in turn generate heat through Joule heating. The heat is produced directly within the metal itself, ensuring rapid and uniform melting. The frequency of the alternating current influences the depth of current penetration, with higher frequencies resulting in shallower penetration. Once melted, the eddy currents also cause stirring of the molten metal, ensuring good mixing and uniform temperature.
Key Points Explained:
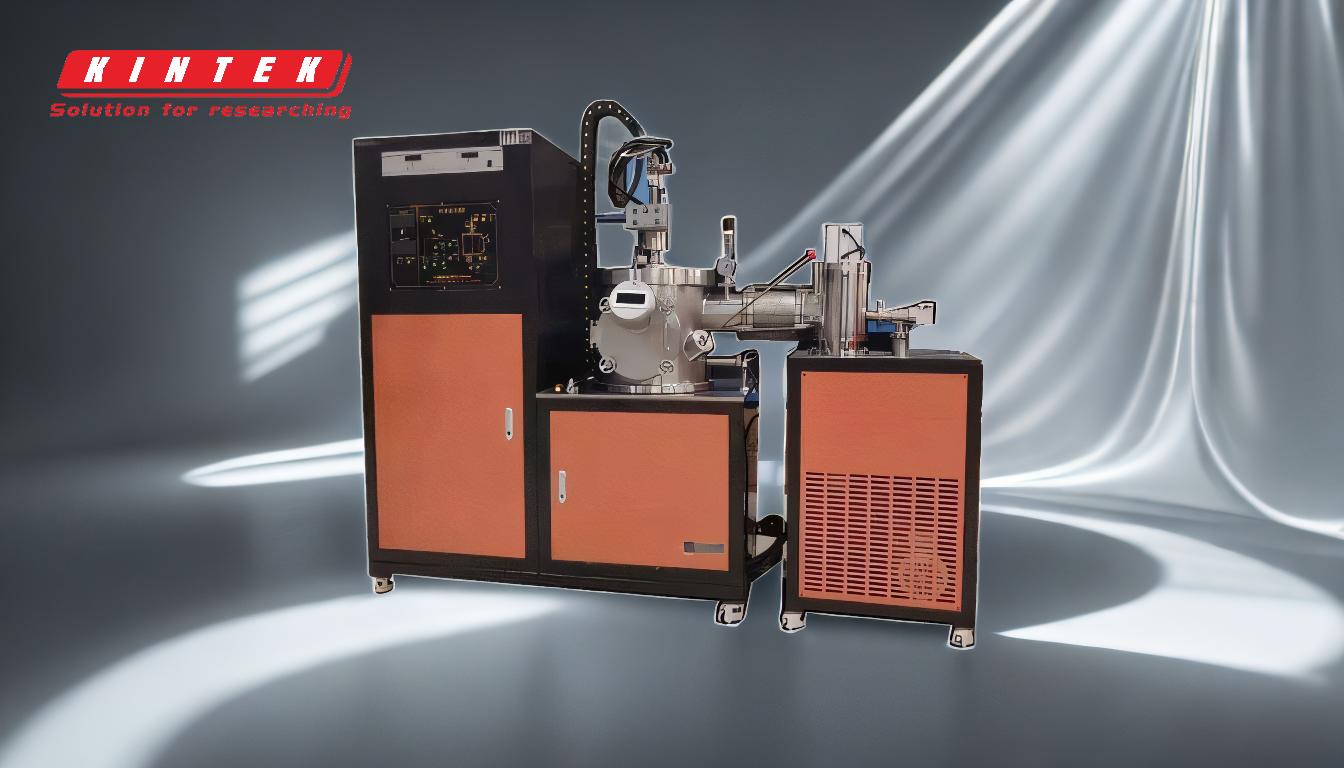
-
Electromagnetic Induction:
- The core principle behind an induction furnace is electromagnetic induction. An alternating current (AC) is passed through a copper coil, creating a powerful electromagnetic field. This field penetrates the conductive metal charge placed inside the furnace.
-
Eddy Currents and Joule Heating:
- When the electromagnetic field interacts with the conductive metal, it induces eddy currents within the metal. These currents flow through the electrical resistance of the metal, generating heat through Joule heating. The heat is produced directly within the metal, making the process highly efficient and clean.
-
Frequency and Penetration Depth:
- The frequency of the alternating current plays a crucial role in determining the depth of current penetration into the metal. Higher frequencies result in shallower penetration, which can be advantageous for certain applications where surface heating is required. Conversely, lower frequencies allow for deeper penetration, suitable for melting larger volumes of metal.
-
Stirring Effect:
- The eddy currents not only generate heat but also cause a stirring effect within the molten metal. This stirring ensures good mixing and uniform temperature distribution, which is essential for producing high-quality alloys and consistent metal properties.
-
Components of an Induction Furnace:
- Copper Coil: The coil is a critical component that carries the alternating current and generates the electromagnetic field.
- Power Supply: An induction power unit converts the input electrical power into the required alternating current. This often involves rectification and filtering to produce a stable medium-frequency current.
- Furnace Chamber: The chamber holds the metal charge and is designed to withstand high temperatures and the mechanical stresses induced by the stirring effect.
-
Advantages of Induction Furnaces:
- Efficiency: Heat is generated directly within the metal, minimizing energy losses.
- Cleanliness: The process produces minimal emissions and waste, making it environmentally friendly.
- Precision: The ability to control the frequency and power input allows for precise temperature control and uniform heating.
- Versatility: Induction furnaces can be used for a wide range of metals and alloys, making them suitable for various industrial applications.
-
Applications:
- Induction furnaces are commonly used in metal casting and foundry operations. They are ideal for melting and alloying metals, producing components with exact compositions and properties. Additionally, they are used in heat treatment processes where precise temperature control is required.
By understanding these key points, one can appreciate the sophisticated yet straightforward process of induction furnaces, making them an indispensable tool in modern metallurgy and manufacturing.
Summary Table:
Key Aspect | Description |
---|---|
Electromagnetic Induction | AC creates a magnetic field, inducing eddy currents in the metal for heating. |
Eddy Currents & Joule Heating | Heat is generated directly within the metal, ensuring efficiency and cleanliness. |
Frequency & Penetration | Higher frequencies = shallow penetration; lower frequencies = deeper penetration. |
Stirring Effect | Eddy currents stir molten metal, ensuring uniform mixing and temperature. |
Components | Copper coil, power supply, and furnace chamber. |
Advantages | High efficiency, cleanliness, precision, and versatility. |
Applications | Metal casting, foundry operations, and heat treatment processes. |
Discover how an induction furnace can revolutionize your metal melting process—contact us today for expert guidance!