Physical vapor deposition (PVD) is a sophisticated process used to create thin films on substrates by vaporizing a solid material and allowing it to condense on the desired surface. This process involves several key steps, including evaporation, transportation, reaction, and deposition, each critical to achieving the desired thin film properties. PVD techniques, such as sputtering, utilize high-energy sources like electron beams or plasma to dislodge atoms from a target material, which are then transported and deposited onto a substrate. The process is conducted under vacuum conditions to ensure that the vaporized atoms reach the substrate without interference from residual gas molecules. PVD is widely used in various industries for its ability to produce durable, high-quality coatings with precise control over film thickness and composition.
Key Points Explained:
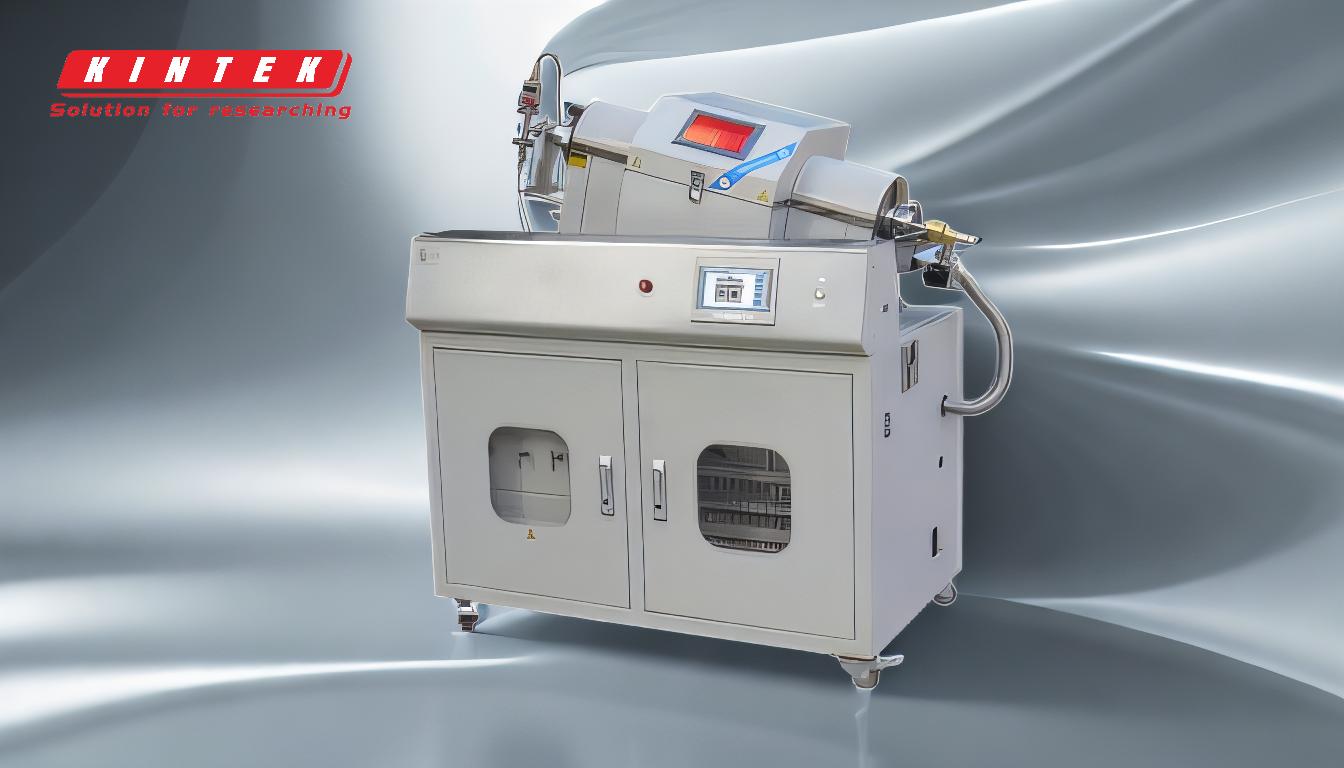
-
Evaporation:
- Process: The first step in PVD involves the evaporation of a solid material. This is achieved using high-energy sources such as electron beams, plasma, or simple heating. The energy causes atoms to be dislodged from the target material, creating a vapor.
- Importance: Evaporation is crucial as it initiates the formation of the vapor phase, which is necessary for the subsequent steps in the PVD process.
-
Transportation:
- Process: Once the material is vaporized, the atoms or molecules are transported through a medium, typically a vacuum, to the substrate. The vacuum environment minimizes collisions with residual gas molecules, ensuring a clean and efficient transfer.
- Importance: Transportation ensures that the vaporized material reaches the substrate without contamination or loss, maintaining the purity and integrity of the thin film.
-
Reaction:
- Process: During the reaction stage, the vaporized atoms may react with introduced gases to form compounds such as metal oxides, nitrides, or carbides. This step is optional and depends on the desired properties of the final coating.
- Importance: The reaction stage allows for the customization of the thin film's chemical composition, enabling the creation of coatings with specific properties like hardness, corrosion resistance, or electrical conductivity.
-
Deposition:
- Process: The final step involves the deposition of the vaporized material onto the substrate. The atoms or molecules condense on the surface, forming a thin film that bonds to the substrate.
- Importance: Deposition is the culmination of the PVD process, resulting in the formation of a thin, uniform coating with the desired characteristics. The quality of the deposition directly affects the performance and durability of the coating.
-
Sputtering Techniques:
- Process: Sputtering is a common PVD technique where a target material is bombarded with high-energy particles, causing atoms to be ejected and deposited onto a substrate. Techniques include direct current (DC) sputtering and radio frequency (RF) sputtering.
- Importance: Sputtering techniques offer precise control over the deposition process, allowing for the creation of thin films with specific properties and thicknesses. These techniques are essential for applications requiring high-quality, uniform coatings.
-
Vacuum Environment:
- Process: The entire PVD process is conducted under vacuum conditions to prevent contamination and ensure that the vaporized atoms reach the substrate without interference.
- Importance: A vacuum environment is critical for maintaining the purity and quality of the thin film. It minimizes the presence of impurities and ensures a clean deposition process.
-
Post-Deposition Treatment:
- Process: After deposition, the thin film may undergo additional treatments such as annealing or heat treatment to enhance its properties.
- Importance: Post-deposition treatments can improve the adhesion, hardness, and overall performance of the thin film, making it more suitable for specific applications.
By understanding and controlling each of these steps, manufacturers can produce thin films with precise properties tailored to specific applications, making PVD a versatile and valuable process in modern material science and engineering.
Summary Table:
Step | Process | Importance |
---|---|---|
Evaporation | High-energy sources vaporize solid material. | Initiates vapor phase for subsequent steps. |
Transportation | Vaporized atoms are transported through a vacuum to the substrate. | Ensures clean transfer and maintains film purity. |
Reaction | Vaporized atoms react with gases to form compounds (optional). | Customizes film properties like hardness and conductivity. |
Deposition | Atoms condense on the substrate, forming a thin film. | Culminates in a uniform coating with desired characteristics. |
Sputtering | High-energy particles eject atoms from a target material for deposition. | Offers precise control over film properties and thickness. |
Vacuum | Process conducted under vacuum to prevent contamination. | Ensures clean, high-quality thin films. |
Post-Deposition | Additional treatments like annealing enhance film properties. | Improves adhesion, hardness, and overall performance. |
Discover how PVD can enhance your material coatings—contact our experts today for tailored solutions!