Physical Vapor Deposition (PVD) is a coating process used to produce thin films and coatings by physically transferring material from a source (target) to a substrate. The process involves four main steps: Evaporation, Transportation, Reaction, and Deposition. During evaporation, a high-energy source bombards the target material, dislodging atoms to form a vapor. These atoms are then transported to the substrate, where they may react with selected gases to form compounds like metal oxides, nitrides, or carbides. Finally, the coating builds up and bonds to the substrate surface. PVD is widely used in industries such as electronics, optics, and aerospace due to its ability to produce durable, high-quality coatings with precise control over thickness and composition.
Key Points Explained:
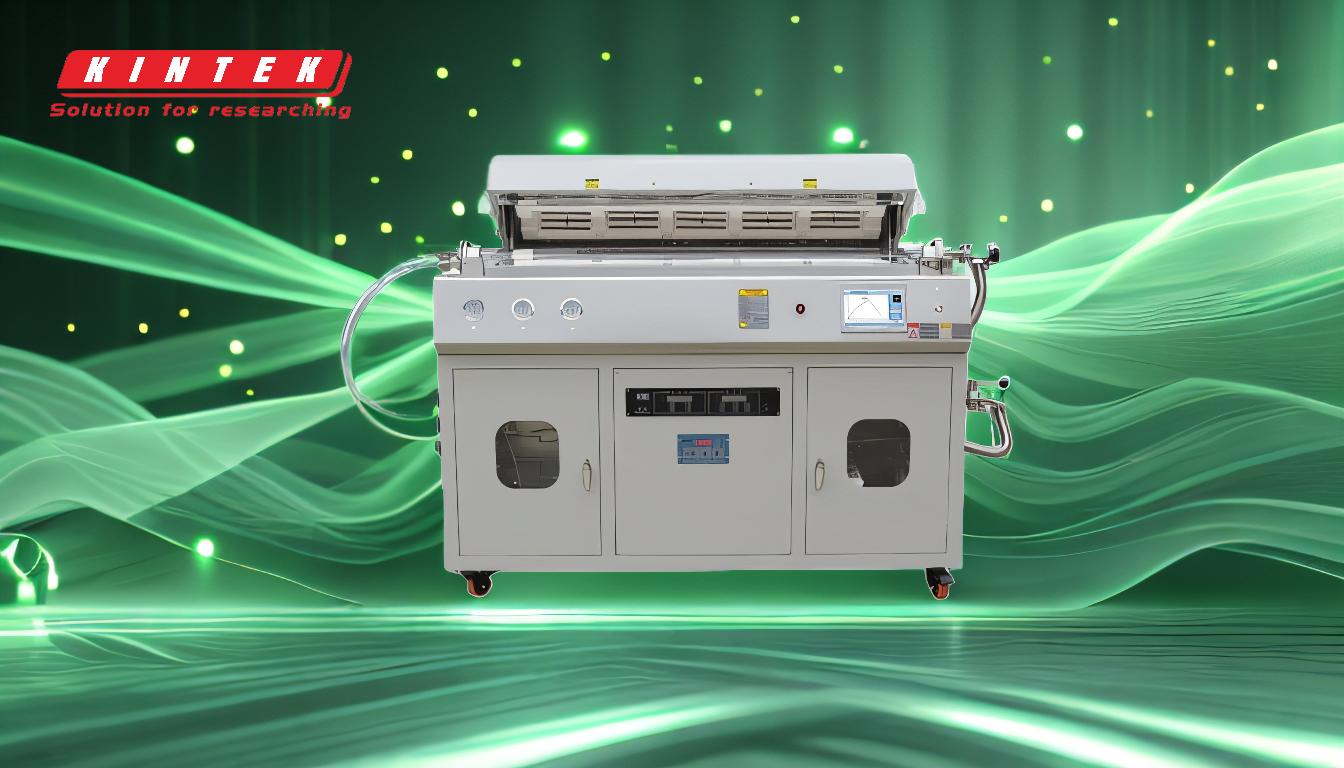
-
Evaporation:
- The first step in the PVD process involves the creation of a vapor from the target material. This is achieved by bombarding the target with a high-energy source, such as an electron beam or plasma, which dislodges atoms from the surface. These atoms are then transformed into a vapor phase, ready for transportation to the substrate.
-
Transportation:
- Once the target material is vaporized, the atoms or molecules are transported through a vacuum or low-pressure environment to the substrate. This step ensures that the vaporized material reaches the substrate uniformly, which is critical for achieving a consistent coating.
-
Reaction:
- During the reaction stage, the vaporized atoms may react with specific gases introduced into the chamber. For example, metal atoms can react with oxygen, nitrogen, or carbon-containing gases to form metal oxides, nitrides, or carbides, respectively. This step is crucial for creating coatings with desired chemical and mechanical properties.
-
Deposition:
- The final step involves the deposition of the coating onto the substrate. The vaporized material condenses on the substrate surface, forming a thin film. The deposition process is carefully controlled to ensure that the coating adheres well to the substrate and achieves the desired thickness and properties.
-
Types of PVD Technologies:
- PVD encompasses several technologies, including sputtering, evaporation, and plasma-assisted PVD. Sputtering, for instance, involves ejecting atoms from a target material by bombarding it with high-energy particles. Plasma-assisted PVD uses plasma to enhance the deposition process, improving coating quality and adhesion.
-
Applications of PVD:
- PVD is widely used in various industries due to its ability to produce high-quality, durable coatings. Common applications include:
- Electronics: For creating thin films in semiconductors and microelectronics.
- Optics: For producing anti-reflective and protective coatings on lenses and mirrors.
- Aerospace: For coating components to improve wear resistance and thermal stability.
- Tooling: For enhancing the durability and performance of cutting tools and molds.
- PVD is widely used in various industries due to its ability to produce high-quality, durable coatings. Common applications include:
-
Advantages of PVD:
- Precision: PVD allows for precise control over coating thickness and composition.
- Durability: PVD coatings are highly durable and resistant to wear, corrosion, and high temperatures.
- Versatility: The process can be used with a wide range of materials, including metals, ceramics, and composites.
- Environmental Friendliness: PVD is a clean process that produces minimal waste and does not involve harmful chemicals.
-
Challenges and Considerations:
- Cost: PVD equipment and processes can be expensive, making it less suitable for low-cost applications.
- Complexity: The process requires precise control over parameters such as temperature, pressure, and gas composition.
- Substrate Limitations: Some substrates may not be compatible with the high temperatures or vacuum conditions required for PVD.
In summary, Physical Vapor Deposition is a versatile and precise coating process that involves four key steps: Evaporation, Transportation, Reaction, and Deposition. It is widely used in industries requiring high-performance coatings, offering advantages such as durability, precision, and environmental friendliness. However, it also comes with challenges related to cost, complexity, and substrate compatibility.
Summary Table:
Step | Description |
---|---|
Evaporation | High-energy source bombards the target, dislodging atoms to form a vapor phase. |
Transportation | Vaporized atoms are transported through a vacuum to the substrate. |
Reaction | Atoms react with gases to form compounds like oxides, nitrides, or carbides. |
Deposition | Coating condenses on the substrate, forming a thin, durable film. |
Discover how PVD can enhance your materials—contact our experts today for tailored solutions!