Quenching is a critical heat treatment process used to rapidly cool a heated workpiece, typically made of steel or alloy, to achieve desired mechanical properties such as increased hardness and strength. The process involves heating the workpiece to a specific temperature, holding it for a period to achieve uniform temperature distribution, and then rapidly cooling it using a medium like oil, water, gas, or brine. The choice of cooling medium depends on the material, its hardenability, and the desired outcome. Quenching transforms the microstructure of the material from austenite to martensite, enhancing its hardness. Different quenching methods, such as oil quenching, nitrogen quenching, and air quenching, are employed based on the application, particularly in industries like aerospace. Additionally, the atmosphere in the furnace and the type of quenching oil (fast or hot) play significant roles in achieving uniform cooling and minimizing defects like distortion or cracking.
Key Points Explained:
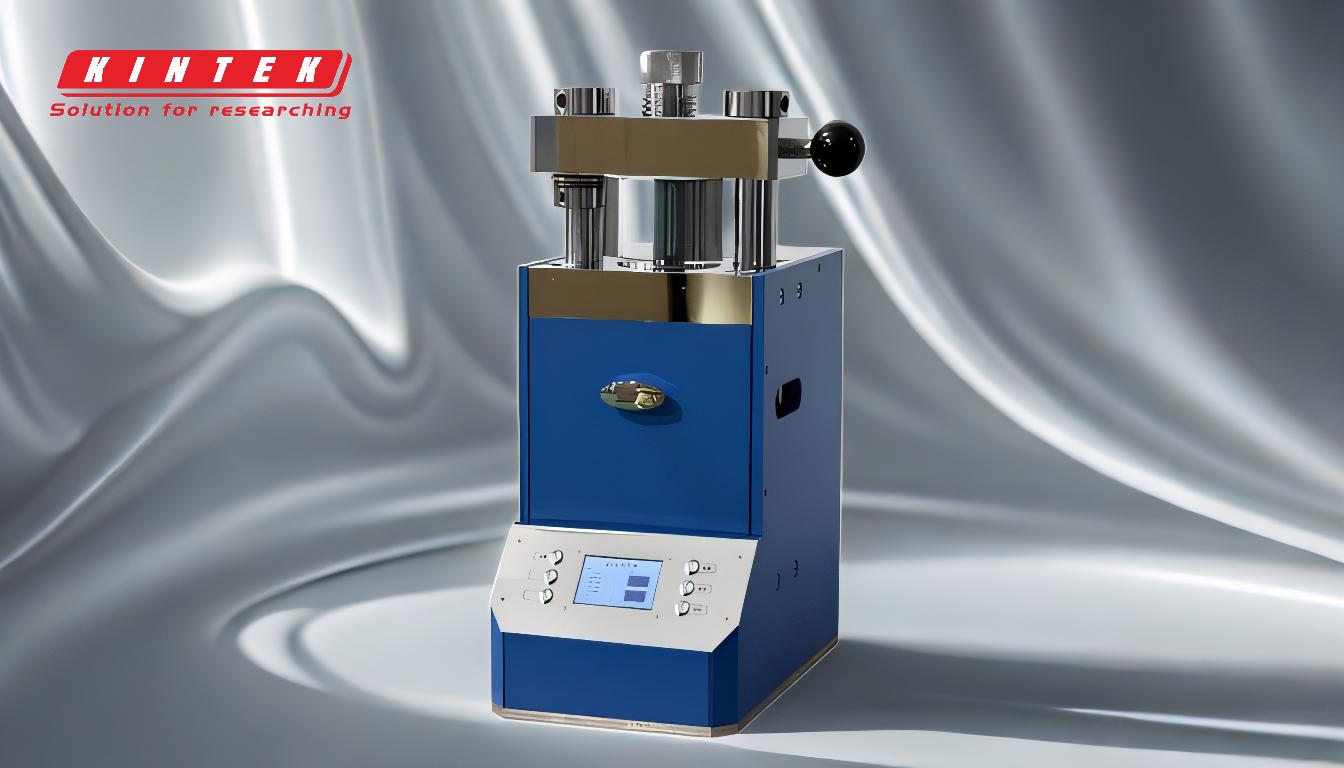
-
Heating and Holding the Workpiece:
- The workpiece, often made of steel or alloy, is heated to a specific temperature, typically within the austenitic range. This temperature varies depending on the material composition.
- The workpiece is held at this temperature for a specific duration to ensure uniform heating throughout its structure. This step is crucial for achieving consistent results during quenching.
-
Rapid Cooling (Quenching):
- After heating, the workpiece is rapidly cooled using a quenching medium. The cooling rate is critical as it determines the transformation of the microstructure from austenite to martensite, which enhances hardness.
- Common cooling mediums include:
- Oil: Fast oils are used for low-carbon steels and low-hardenability alloys, while hot oils are preferred for highly-hardenable alloys to reduce distortion and cracking.
- Water: Often used for materials requiring very rapid cooling, such as plain carbon steels.
- Gas (e.g., Nitrogen): Used in controlled environments to achieve uniform cooling, especially in aerospace applications.
- Brine: A mixture of water and salt, used for faster cooling rates than plain water.
-
Microstructural Transformation:
- The rapid cooling process transforms the microstructure of the workpiece from austenite to martensite. Martensite is a hard, brittle phase that significantly increases the material's hardness and strength.
- This transformation is critical for achieving the desired mechanical properties in the final product.
-
Quenching Methods in Aerospace:
- In aerospace heat treatment, quenching methods like oil quenching, nitrogen quenching, brine quenching, and air quenching are employed. Each method is chosen based on the material and the specific properties required for aerospace components.
- For example, nitrogen quenching is often used for its ability to provide uniform cooling and reduce the risk of distortion.
-
Role of Furnace Atmosphere:
- The atmosphere inside the furnace during heating plays a crucial role in the quenching process. It can be chemically inert to protect the material from surface reactions or chemically reactive to enable surface changes.
- This is particularly important for materials like fine ceramics, where surface integrity is critical.
-
Minimizing Defects:
- Proper selection of quenching medium and method is essential to minimize defects such as distortion, cracking, and residual stresses.
- For instance, hot oils are used at elevated temperatures to ensure uniform cooling across the workpiece's cross-section, reducing the risk of cracking.
-
Practical Implementation:
- In practice, quenching involves moving the workpiece from the furnace to the quenching medium. For example, in a water quenching setup, the water tank is positioned below the furnace, and the workpiece is lowered into the water using a chain mechanism.
- This step must be executed quickly and precisely to ensure consistent cooling rates and avoid uneven hardening.
By understanding these key points, equipment and consumable purchasers can make informed decisions about the quenching process, ensuring they select the right materials, mediums, and methods for their specific applications.
Summary Table:
Step | Description |
---|---|
Heating | Workpiece is heated to a specific temperature within the austenitic range. |
Holding | Held at temperature to ensure uniform heating for consistent results. |
Rapid Cooling | Cooled rapidly using mediums like oil, water, gas, or brine for transformation. |
Microstructural Change | Transforms austenite to martensite, increasing hardness and strength. |
Defect Minimization | Proper medium selection reduces distortion, cracking, and residual stresses. |
Optimize your quenching process for superior results—contact our experts today!