Sintering is a critical process in materials science and chemistry, used to transform powdery or granular materials into dense, solid structures without melting them completely. It involves the application of heat and pressure below the material's melting point, enabling atomic diffusion across particle boundaries and resulting in a cohesive, low-porosity product. This process is widely applied in industries such as powder metallurgy, ceramics, and advanced material manufacturing. The sintering process typically involves stages like powder preparation, compaction, controlled heating in a sintering furnace, and cooling, ensuring the final product achieves the desired mechanical and structural properties.
Key Points Explained:
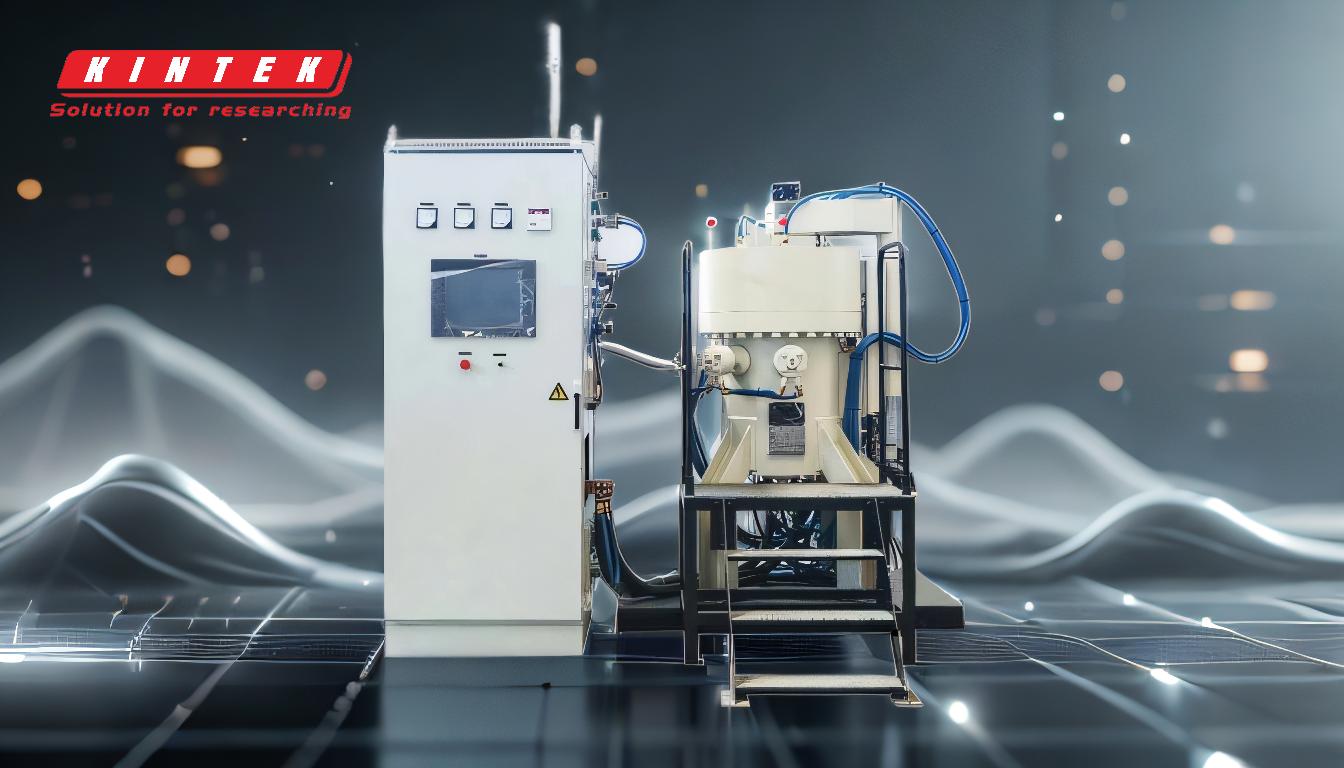
-
Definition of Sintering:
- Sintering, also known as frittage, is the process of compacting and forming a solid mass of material by applying heat and pressure without reaching the material's melting point. This allows atoms to diffuse across particle boundaries, fusing them into a single, cohesive structure.
-
Stages of the Sintering Process:
- Powder Preparation: The raw material, often in powder form, is mixed with a bonding agent (e.g., water, wax, or polymer) to create a uniform blend.
- Compaction: The powder mixture is pressed into a desired shape using mechanical pressure, reducing voids and ensuring uniformity.
- Heating in a Sintering Furnace: The compacted material is subjected to controlled heating in a sintering furnace. The temperature is carefully regulated to facilitate particle bonding without causing complete melting.
- Cooling: After sintering, the material is cooled to solidify into a rigid, low-porosity structure.
-
Mechanisms of Sintering:
- Diffusion: Heat causes atoms to diffuse across particle boundaries, leading to neck formation between particles.
- Densification: As particles bond, the material becomes denser, reducing porosity and increasing strength.
- Bonding Agent Role: In some cases, intermediate bonding agents (e.g., bronze) melt and couple between particles, leaving the primary material unaltered.
-
Applications of Sintering:
- Powder Metallurgy: Used to create metal components with high strength and durability.
- Ceramics: Essential for producing ceramic products with precise shapes and properties.
- Advanced Materials: Applied in manufacturing materials with high melting points, such as tungsten and molybdenum.
-
Types of Sintering Furnaces:
- Sintering furnaces vary in design and functionality, with some using vacuum environments and high pressure to achieve optimal results. For example, a hot press sintering furnace combines high temperature and pressure to fuse ceramic powders into solid materials.
-
Advantages of Sintering:
- Enhanced Material Properties: Sintered materials exhibit improved hardness, strength, and durability.
- Cost-Effectiveness: The process is efficient and reduces material waste.
- Versatility: Suitable for a wide range of materials and applications.
By understanding the sintering process and its stages, manufacturers can optimize the production of high-quality materials for various industrial applications. The use of advanced sintering furnaces ensures precise control over temperature and pressure, resulting in consistent and reliable outcomes.
Summary Table:
Key Aspect | Details |
---|---|
Definition | Compacting and forming solid materials using heat and pressure below melting point. |
Stages | Powder preparation, compaction, heating in a sintering furnace, and cooling. |
Mechanisms | Diffusion, densification, and bonding agent role. |
Applications | Powder metallurgy, ceramics, and advanced materials. |
Advantages | Enhanced material properties, cost-effectiveness, and versatility. |
Discover how sintering can optimize your material production—contact our experts today!