Sintering is a critical manufacturing process used to create solid materials from powdered substances by applying heat and pressure without reaching the material's melting point. The process involves several stages, including powder preparation, compaction, heating, and cooling. During sintering, particles bond through diffusion, leading to densification and the formation of a cohesive structure. The process is widely used in metallurgy, ceramics, and other industries to produce high-strength, low-porosity materials. Below, the key stages and mechanisms of sintering are explained in detail.
Key Points Explained:
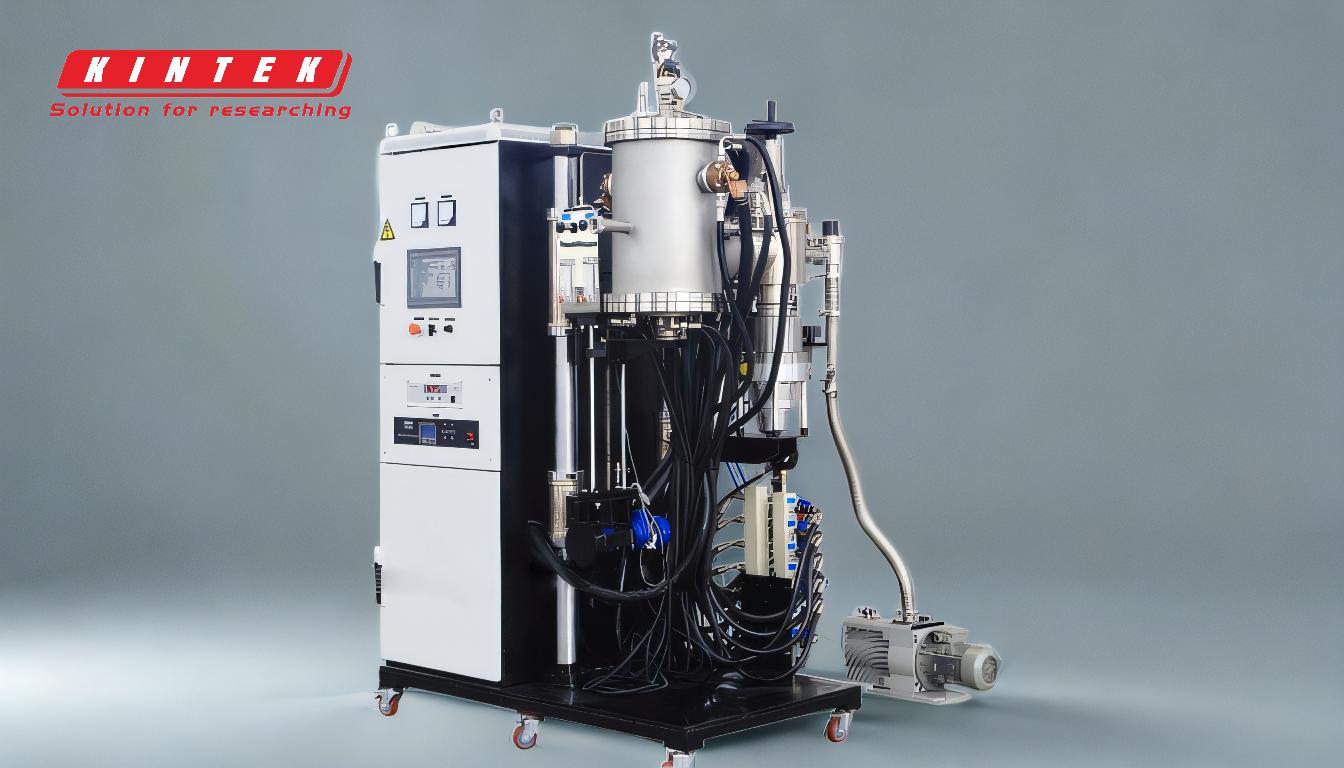
-
Powder Preparation
- The sintering process begins with the preparation of raw materials in powder form.
- The powder is often mixed with additives such as binders, deflocculants, or coupling agents to improve handling and compaction properties.
- For ceramics, a slurry is created by mixing water, binders, and ceramic powder, which is then spray-dried to form granules.
- In metallurgy, metal powders are selected based on the desired final properties, such as strength or thermal conductivity.
-
Compaction
- The powder is compacted into a specific shape using mechanical pressure.
- Methods include cold or hot pressing, where the powder is compressed in a mold to form a "green" part.
- Compaction ensures uniformity and eliminates voids, creating a dense and cohesive structure before sintering.
- The green part is fragile and requires careful handling to avoid damage before the sintering process.
-
Heating and Sintering
- The compacted material is heated in a controlled environment, typically in a sintering furnace or kiln.
- The temperature is carefully regulated to remain just below the material's melting point, allowing particles to bond without liquefying.
- During heating, atoms diffuse across particle boundaries, forming necks and densifying the material.
- Liquid phase sintering (LPS) may be used to accelerate densification by introducing a liquid phase that flows into pores and promotes particle merging.
- The heating process also removes binders, lubricants, or other additives, leaving behind a solid, low-porosity structure.
-
Cooling and Solidification
- After sintering, the material is cooled gradually to solidify into a rigid and cohesive structure.
- Cooling rates are controlled to prevent internal stresses or cracking.
- The final product exhibits improved mechanical properties, such as strength, hardness, and wear resistance, due to the elimination of voids and the formation of strong interparticle bonds.
-
Types of Sintering
- Solid-State Sintering: Involves particle bonding through diffusion without a liquid phase. Commonly used for metals and ceramics.
- Liquid Phase Sintering (LPS): Introduces a liquid phase to enhance densification and particle merging. Suitable for materials with high melting points or complex compositions.
- Transient Liquid Phase Sintering: A temporary liquid phase forms during heating but solidifies during cooling, leaving a dense structure.
-
Applications of Sintering
- Sintering is used to produce a wide range of materials, including:
- Metal parts for automotive and aerospace industries.
- Ceramic components for electronics and medical devices.
- Cemented carbides for cutting tools and wear-resistant parts.
- The process is particularly valuable for materials with extremely high melting points, such as tungsten and molybdenum, which are difficult to process using traditional melting methods.
- Sintering is used to produce a wide range of materials, including:
-
Factors Influencing Sintering
- Temperature: Must be carefully controlled to ensure particle bonding without melting.
- Pressure: Applied during compaction to achieve uniform density.
- Atmosphere: Controlled environments (e.g., inert gases) prevent oxidation or contamination.
- Particle Size and Shape: Smaller particles and spherical shapes enhance densification and bonding.
Sintering is a versatile and essential process for manufacturing high-performance materials with tailored properties. By understanding the stages and mechanisms involved, manufacturers can optimize the process to produce components with superior strength, durability, and precision.
Summary Table:
Stage | Description |
---|---|
Powder Preparation | Raw materials are prepared in powder form, often mixed with additives. |
Compaction | Powder is pressed into a shape, forming a 'green' part with uniform density. |
Heating and Sintering | Material is heated below melting point, allowing particles to bond and densify. |
Cooling | Gradual cooling solidifies the material, enhancing strength and durability. |
Types of Sintering | Solid-state, liquid phase, and transient liquid phase sintering methods. |
Applications | Used in automotive, aerospace, electronics, and medical industries. |
Key Factors | Temperature, pressure, atmosphere, and particle size influence sintering. |
Optimize your sintering process for superior results—contact our experts today!