Brazing is a metal-joining process that involves melting and flowing a filler metal into the joint between two or more metal parts. The filler metal has a lower melting point than the base metals being joined, and it bonds to the base metals through capillary action. The purpose of brazing is to create strong, durable, and leak-proof joints between metal components, often in applications where welding is not feasible or desirable. Brazing is widely used in industries such as automotive, aerospace, electronics, and HVAC due to its ability to join dissimilar metals, produce clean joints, and operate at lower temperatures compared to welding.
Key Points Explained:
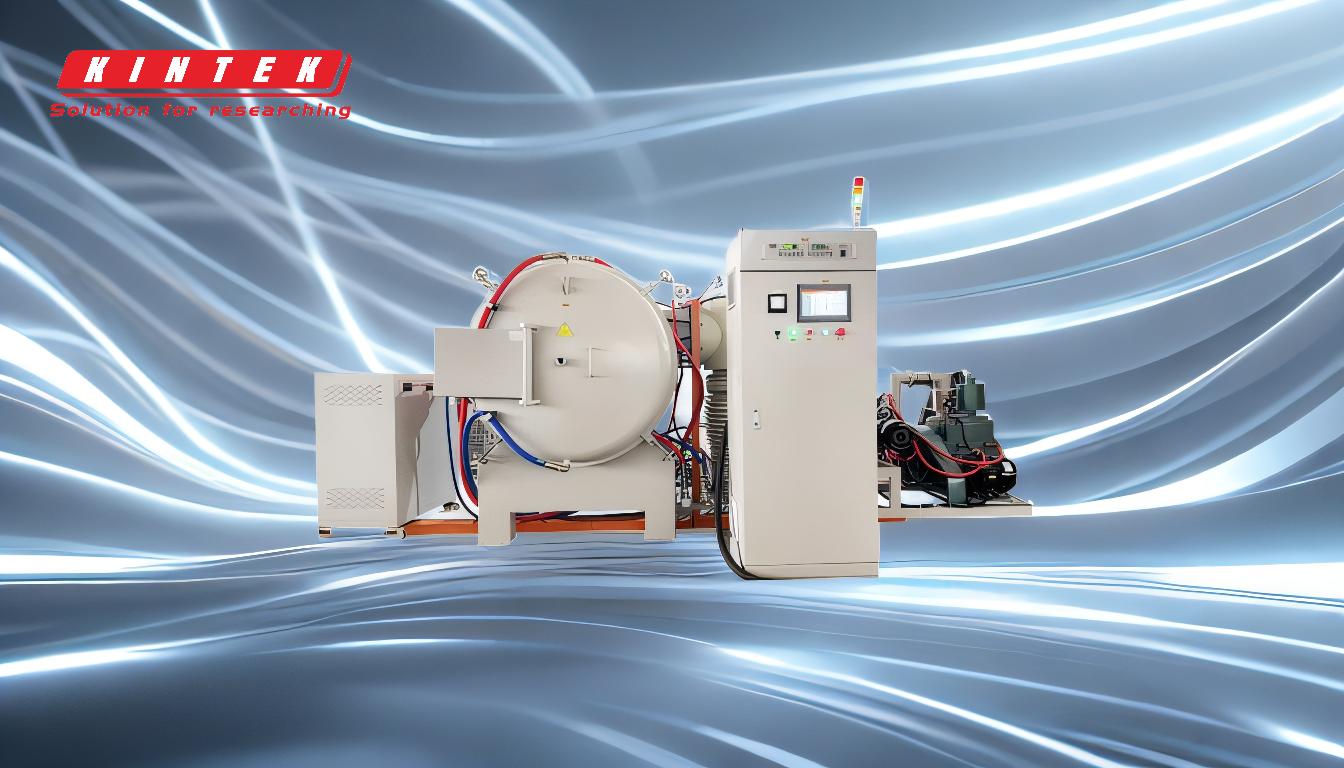
-
Strong and Durable Joints:
- Brazing creates joints that are strong and capable of withstanding mechanical stress, vibration, and thermal cycling. The filler metal forms a metallurgical bond with the base metals, resulting in a joint that is often as strong as or stronger than the base materials themselves.
- This makes brazing ideal for applications requiring high reliability, such as in aerospace components or automotive radiators.
-
Joining Dissimilar Metals:
- One of the key advantages of brazing is its ability to join dissimilar metals, such as copper to steel or aluminum to stainless steel. This is particularly useful in industries where different materials are used for their unique properties, such as thermal conductivity, corrosion resistance, or strength.
- For example, in HVAC systems, brazing is used to join copper tubing to aluminum fins, combining the thermal conductivity of copper with the lightweight properties of aluminum.
-
Lower Operating Temperatures:
- Brazing operates at temperatures below the melting point of the base metals, typically between 450°C and 900°C. This reduces the risk of thermal distortion, warping, or damage to heat-sensitive components, making it suitable for delicate or complex assemblies.
- Lower temperatures also mean less energy consumption compared to welding, contributing to cost savings and environmental benefits.
-
Clean and Aesthetic Joints:
- Brazed joints are often clean and smooth, requiring minimal post-processing. The capillary action of the filler metal ensures that the joint is filled evenly, resulting in a visually appealing finish.
- This is particularly important in industries like electronics or decorative metalwork, where appearance matters.
-
Leak-Proof Seals:
- Brazing is commonly used to create leak-proof seals in applications such as refrigeration, plumbing, and fuel systems. The filler metal flows into the joint, filling any gaps and creating a hermetic seal that prevents leaks.
- For instance, brazing is used in the manufacturing of heat exchangers and condensers, where leak-proof joints are critical for efficient operation.
-
Versatility in Applications:
- Brazing is a versatile process that can be used for a wide range of applications, from small electronic components to large industrial assemblies. It is suitable for both manual and automated production processes, making it adaptable to various manufacturing needs.
- Examples include joining turbine blades in jet engines, assembling circuit boards, and fabricating medical devices.
-
Cost-Effectiveness:
- Brazing is often more cost-effective than welding, especially for complex or high-volume production. The lower energy requirements, reduced need for post-processing, and ability to automate the process contribute to lower overall costs.
- Additionally, the ability to join dissimilar metals can reduce material costs by allowing the use of less expensive materials for certain parts of an assembly.
-
Minimal Heat-Affected Zone (HAZ):
- Since brazing operates at lower temperatures, the heat-affected zone (HAZ) is minimal compared to welding. This reduces the risk of weakening the base metals and preserves their mechanical properties.
- This is particularly important for materials that are sensitive to heat, such as certain alloys or heat-treated metals.
In summary, brazing is a highly effective metal-joining process that offers numerous advantages, including the ability to create strong, durable, and leak-proof joints, join dissimilar metals, and operate at lower temperatures. Its versatility and cost-effectiveness make it a preferred choice in many industries, from aerospace and automotive to electronics and HVAC.
Summary Table:
Key Advantage | Description |
---|---|
Strong and Durable Joints | Creates joints as strong as or stronger than base materials, ideal for high-reliability applications. |
Joins Dissimilar Metals | Bonds metals like copper to steel or aluminum to stainless steel, leveraging unique material properties. |
Lower Operating Temperatures | Operates at 450°C–900°C, reducing thermal distortion and energy consumption. |
Clean and Aesthetic Joints | Produces smooth, visually appealing joints with minimal post-processing. |
Leak-Proof Seals | Ensures hermetic seals in refrigeration, plumbing, and fuel systems. |
Versatility | Suitable for small electronics to large industrial assemblies, manual or automated. |
Cost-Effective | Lower energy use, reduced post-processing, and automation make it economical. |
Minimal Heat-Affected Zone | Preserves base metal properties, ideal for heat-sensitive materials. |
Discover how brazing can enhance your manufacturing process—contact our experts today!