Heat treatment is a critical process in materials engineering, primarily used to alter or enhance the physical and chemical properties of metals and other materials. By subjecting materials to controlled heating and cooling cycles, heat treatment can improve characteristics such as strength, ductility, hardness, and toughness. This process is essential in various industrial applications, enabling materials to meet specific performance requirements, reduce internal stresses, and enhance durability. Heat treatment is particularly beneficial for steel and other metals, making them more suitable for manufacturing processes like welding, machining, and forming.
Key Points Explained:
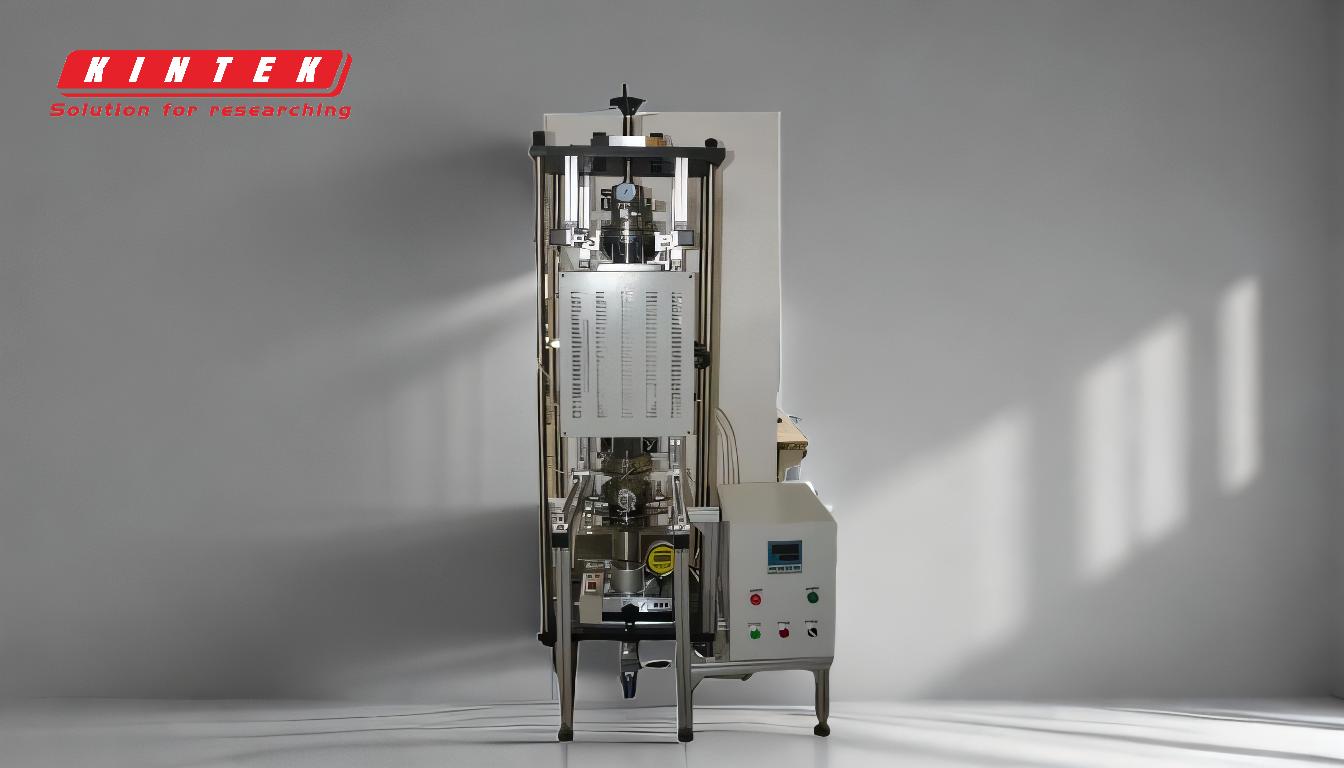
-
Altering Material Properties:
- Heat treatment is primarily used to modify the physical and chemical properties of materials, especially metals. This includes improving strength, ductility, hardness, and toughness.
- For example, steel can be hardened to increase its wear resistance or softened to improve its machinability.
-
Controlled Heating and Cooling:
- The process involves precise control of heating and cooling cycles to achieve desired material characteristics.
- Uniform heating, as in furnace heat treating, ensures consistent results across the entire material, making it cost-effective for parts requiring overall hardening.
-
Application to Ferrous and Non-Ferrous Metals:
- Heat treatment is not limited to steel; it can be applied to a wide range of ferrous (iron-based) and non-ferrous metals (e.g., aluminum, copper).
- Each material responds differently to heat treatment, allowing for tailored improvements in properties like surface hardness or flexibility.
-
Industrial Applications:
- Heat-treated materials are widely used in industries such as automotive, aerospace, construction, and manufacturing.
- For instance, heat-treated steel components are essential in machinery, tools, and structural applications due to their enhanced durability and strength.
-
Stress Relief and Machinability:
- Heat treatment can relieve internal stresses in materials, making them easier to machine, weld, or form.
- This is particularly important after processes like welding, where residual stresses can compromise the integrity of the material.
-
Enhancing Wear Resistance and Brittleness:
- By introducing wear-resistant characteristics, heat treatment extends the lifespan of components subjected to friction or abrasion.
- It also reduces brittleness, making materials less prone to cracking or failure under stress.
-
Improving Electrical and Magnetic Properties:
- Certain heat treatment processes can enhance the electrical conductivity or magnetic properties of materials, making them suitable for specialized applications like electronics or transformers.
-
Cost-Efficiency and Versatility:
- Heat treatment is a cost-effective method for improving material properties without altering their chemical composition.
- Its versatility allows manufacturers to achieve a wide range of desired characteristics, making it indispensable in modern engineering and production processes.
In summary, heat treatment serves as a transformative process that enhances the performance, durability, and functionality of materials, ensuring they meet the rigorous demands of industrial and manufacturing applications.
Summary Table:
Key Benefits of Heat Treatment | Description |
---|---|
Alters Material Properties | Improves strength, ductility, hardness, and toughness. |
Controlled Heating & Cooling | Ensures uniform results and cost-effectiveness. |
Applies to Ferrous & Non-Ferrous Metals | Tailored improvements for steel, aluminum, copper, etc. |
Industrial Applications | Widely used in automotive, aerospace, and construction. |
Stress Relief & Machinability | Reduces internal stresses for easier welding and forming. |
Wear Resistance & Brittleness | Extends lifespan and reduces failure under stress. |
Electrical & Magnetic Properties | Enhances conductivity for specialized applications. |
Cost-Efficiency & Versatility | Improves properties without altering chemical composition. |
Transform your materials with heat treatment—contact our experts today to learn more!