The PVD (Physical Vapor Deposition) process gas is a critical component in the deposition of thin films onto substrates. The primary gas used is argon, which is inert and provides the necessary momentum to free atoms from the target material. Additionally, reactive gases such as oxygen, nitrogen, and methane are introduced to form compounds with the vaporized material, resulting in coatings like metal oxides, nitrides, and carbides. The process occurs in a vacuum environment, where the gas is ionized to create plasma, facilitating the deposition of atoms onto the substrate. This method is widely used for enhancing surface properties such as hardness, oxidation resistance, and friction reduction.
Key Points Explained:
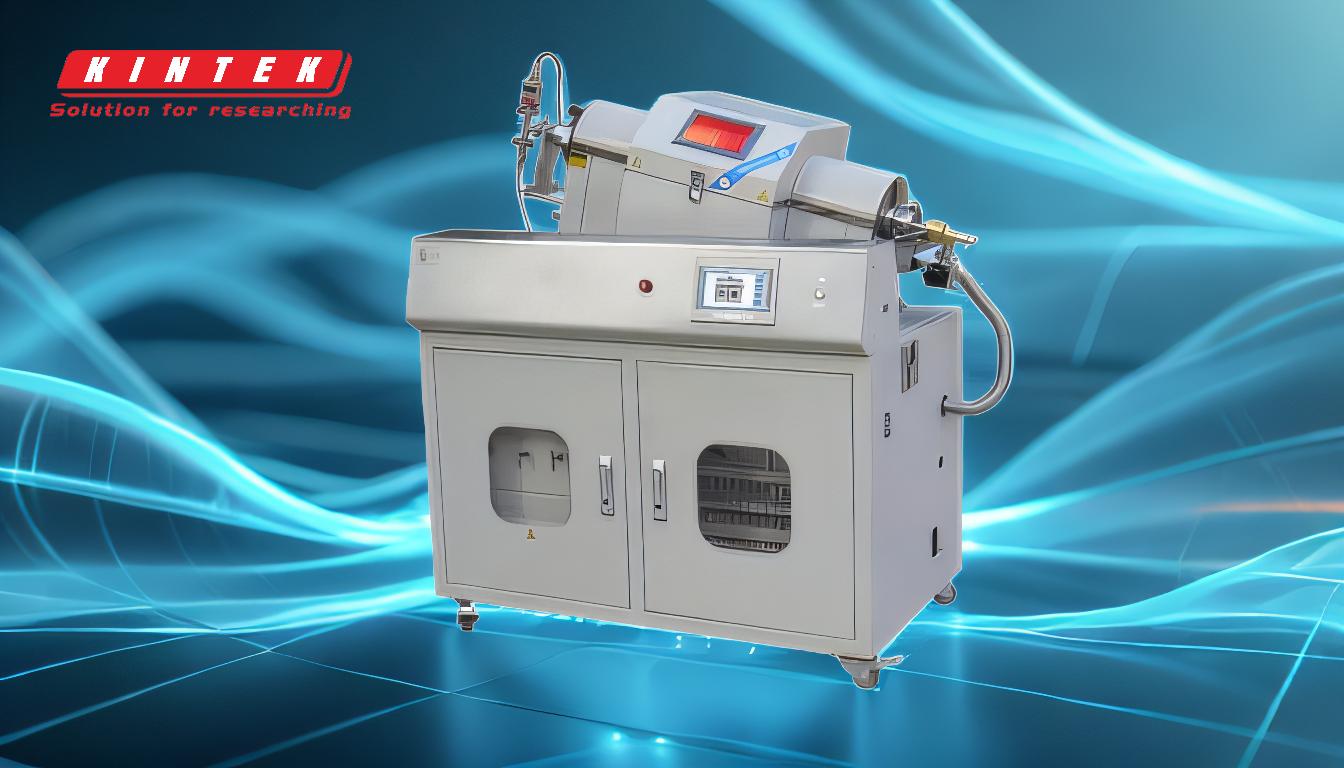
-
Primary Process Gas - Argon:
- Argon is the most commonly used gas in the PVD process due to its inert nature and ability to generate sufficient momentum to sputter atoms from the target material.
- It is used in the initial stages to create a plasma environment, which ionizes the gas and allows for the efficient transfer of energy to the target material.
- Argon's role is crucial in the sputtering process, where it bombards the target material, causing atoms to be ejected and subsequently deposited onto the substrate.
-
Reactive Gases - Oxygen, Nitrogen, and Methane:
- Reactive gases are introduced during the transportation stage of the PVD process to react with the vaporized metal atoms.
- Oxygen is used to form metal oxides, which can enhance oxidation resistance and other surface properties.
- Nitrogen is used to create metal nitrides, which are known for their hardness and wear resistance.
- Methane is used to produce metal carbides, which are valued for their high hardness and thermal stability.
- These reactive gases play a vital role in tailoring the properties of the final coating to meet specific application requirements.
-
Plasma Generation and Ionization:
- The PVD process begins with the creation of plasma from the process gas, often using an inductively coupled plasma (ICP) source.
- High-energy electrons within the plasma collide with gas molecules, causing them to dissociate into atoms and ions.
- This ionization process is essential for the efficient transfer of energy and the subsequent deposition of the coating material onto the substrate.
-
Vacuum Environment:
- The PVD process is conducted under vacuum conditions to minimize contamination and ensure a controlled environment for the deposition of thin films.
- The vacuum environment allows for the efficient movement of vaporized atoms from the target to the substrate without interference from atmospheric gases.
- The low pressure also helps in achieving a uniform and high-quality coating on the substrate.
-
Deposition and Coating Formation:
- The vaporized atoms or molecules travel through the vacuum chamber and deposit onto the substrate, where they condense to form a thin film.
- The deposition process can be influenced by the introduction of reactive gases, which react with the vaporized material to form compounds with specific properties.
- The resulting coatings can range from nanoscale to visible thicknesses, depending on the application requirements.
-
Applications and Benefits:
- PVD coatings are widely used in various industries to improve the performance of components by enhancing properties such as hardness, wear resistance, and oxidation resistance.
- The ability to incorporate different materials and tailor the coating properties makes PVD a versatile and valuable technique in surface engineering.
- The process is also environmentally friendly, as it does not involve the use of hazardous chemicals and produces minimal waste.
In summary, the PVD process gas, primarily argon, along with reactive gases like oxygen, nitrogen, and methane, plays a crucial role in the deposition of thin films with tailored properties. The process is conducted in a vacuum environment, where plasma generation and ionization facilitate the efficient transfer of material from the target to the substrate. The resulting coatings offer significant benefits in terms of surface properties and are widely used across various industries.
Summary Table:
Key Aspect | Details |
---|---|
Primary Gas (Argon) | Inert gas used for sputtering and plasma generation. |
Reactive Gases | Oxygen, nitrogen, and methane form metal oxides, nitrides, and carbides. |
Plasma Generation | Ionization of gas creates plasma for efficient energy transfer. |
Vacuum Environment | Ensures contamination-free, uniform coating deposition. |
Applications | Enhances hardness, wear resistance, and oxidation resistance in coatings. |
Discover how PVD process gases can optimize your surface engineering—contact our experts today!