Rapid annealing, specifically rapid thermal annealing (RTA) or rapid thermal processing (RTP), is a specialized heat treatment process used primarily in semiconductor manufacturing. It involves heating silicon wafers or other materials to extremely high temperatures (over 1,000 °C) in a matter of seconds. This rapid heating and cooling process is designed to alter the material's microstructure, improving its electrical and mechanical properties. Unlike traditional annealing, which involves slower heating and cooling cycles, RTA achieves its effects quickly, making it ideal for modern semiconductor fabrication where precision and speed are critical. The process is used to repair crystal defects, reduce internal stresses, and enhance the material's ductility and electrical performance.
Key Points Explained:
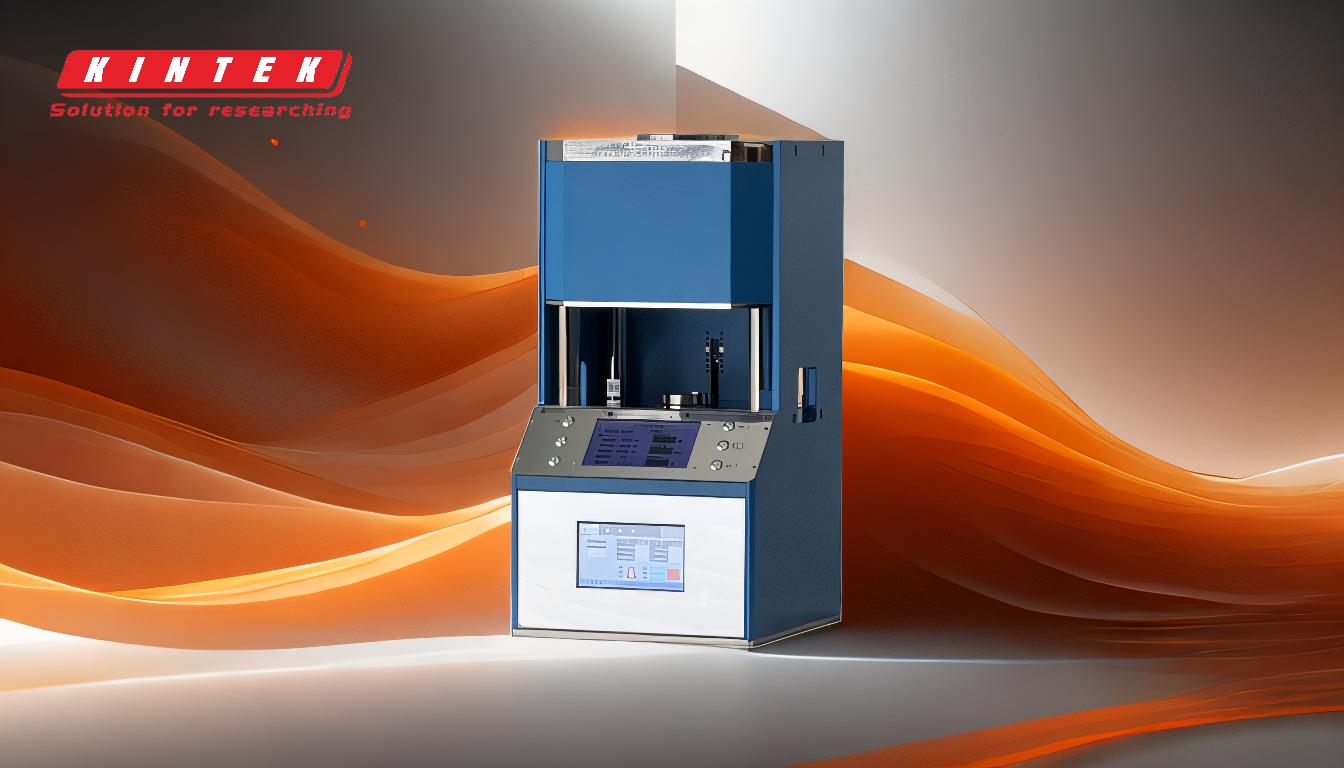
-
Definition and Purpose of Rapid Annealing:
- Rapid thermal annealing (RTA) is a high-temperature heat treatment process used to modify the microstructure of materials, particularly silicon wafers in semiconductor manufacturing.
- The primary purpose is to improve electrical properties, repair crystal defects, and reduce internal stresses in the material.
-
Temperature and Speed:
- RTA involves heating materials to temperatures exceeding 1,000 °C.
- The heating process is extremely fast, often completed in seconds or less, followed by rapid cooling.
- This speed distinguishes RTA from traditional annealing, which uses slower heating and cooling cycles.
-
Applications in Semiconductor Manufacturing:
- RTA is widely used in the production of semiconductors to enhance the performance of silicon wafers.
- It helps in activating dopants, repairing implantation damage, and improving the overall quality of the material.
-
Microstructural Changes:
- During RTA, the material's crystalline structure becomes fluid-like, allowing defects to repair themselves.
- The rapid cooling process results in a more uniform and refined grain structure, improving ductility and reducing hardness.
-
Benefits of Rapid Annealing:
- Improved Electrical Properties: Enhances the conductivity and performance of semiconductor materials.
- Stress Relief: Reduces internal stresses that could lead to material failure.
- Ductility and Workability: Makes the material more suitable for further processing, such as machining or cold working.
-
Comparison with Traditional Annealing:
- Traditional annealing involves slower heating and cooling cycles, making it less suitable for high-speed semiconductor manufacturing.
- RTA's speed and precision make it ideal for modern fabrication processes where time and accuracy are critical.
-
Material Suitability:
- While RTA is primarily used for silicon wafers, it can also be applied to other materials, including metals and ceramics, to achieve similar microstructural improvements.
-
Process Control and Precision:
- RTA requires precise control of temperature and timing to achieve the desired material properties.
- Advanced equipment, such as rapid thermal processing furnaces, is used to ensure consistent and accurate results.
-
Challenges and Considerations:
- The rapid heating and cooling can introduce thermal stresses if not properly managed.
- Careful monitoring is required to avoid material damage or inconsistent results.
-
Future Trends:
- As semiconductor devices continue to shrink in size, the demand for precise and rapid annealing processes like RTA is expected to grow.
- Advances in RTA technology may lead to even faster and more efficient heat treatment methods.
By understanding these key points, equipment and consumable purchasers can better evaluate the suitability of rapid annealing processes for their specific applications, ensuring optimal material performance and manufacturing efficiency.
Summary Table:
Aspect | Details |
---|---|
Definition | High-temperature heat treatment for microstructural modification. |
Temperature Range | Exceeds 1,000 °C in seconds. |
Key Applications | Semiconductor manufacturing, defect repair, stress reduction. |
Benefits | Improved electrical properties, enhanced ductility, stress relief. |
Comparison | Faster and more precise than traditional annealing. |
Materials | Primarily silicon wafers, but also metals and ceramics. |
Challenges | Thermal stress management, precise process control required. |
Future Trends | Growing demand for faster, more efficient RTA in semiconductor fabrication. |
Discover how rapid annealing can optimize your semiconductor processes—contact our experts today!