Spark Plasma Sintering (SPS) is an advanced sintering technique that utilizes pulsed direct current (DC) to rapidly densify powder materials. Unlike traditional sintering methods, SPS applies uniaxial mechanical pressure and a pulsed electric current to the powder compact, generating localized high temperatures (up to 10,000°C) and plasma between particles. This process enables rapid heating rates (up to 1000°C/min), short sintering times, and densification at lower temperatures compared to conventional sintering. The combination of mechanical pressure, electric field, and thermal field enhances particle bonding, leading to high-density materials (over 99% in some cases) while preserving the inherent properties of nano-powders. SPS is energy-efficient, environmentally friendly, and suitable for a wide range of materials.
Key Points Explained:
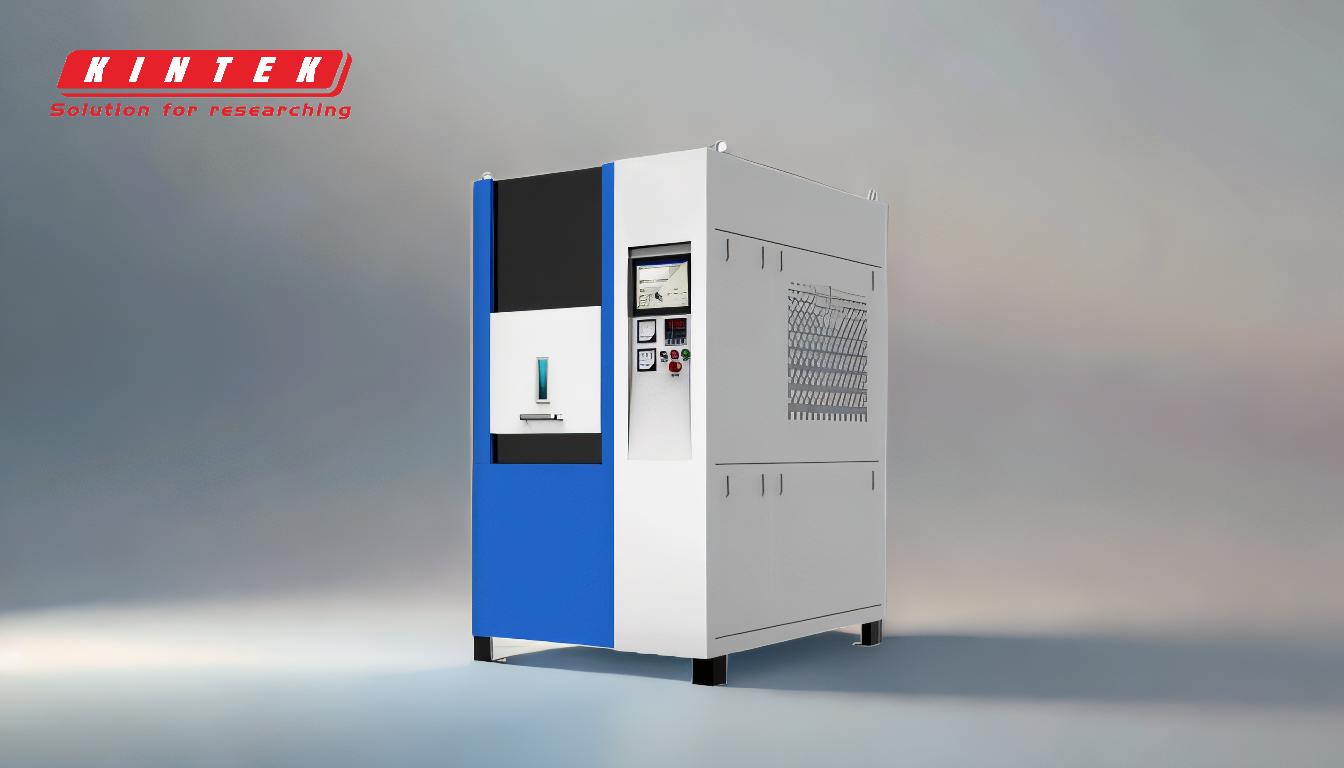
-
Principle of SPS:
- SPS operates on the principle of electric spark discharge, where a high-energy pulsed current generates spark plasma between powder particles.
- This plasma creates localized high temperatures (up to 10,000°C), which melt and fuse particle surfaces, forming "necks" that grow over time to increase material density.
-
Components and Setup:
- SPS uses a punch/die system similar to hot pressing, where powder is placed in a die and compressed under uniaxial mechanical load.
- A pulsed DC current is applied directly to the powder compact, generating Joule heating and plasma activation.
-
Key Mechanisms:
- Plasma Activation: The pulsed current creates plasma between particles, reducing particle gaps and enhancing surface diffusion.
- Joule Heating: The electric current heats the powder compact directly, achieving rapid heating rates (up to 1000°C/min).
- Discharge Shock Pressure: The high-energy pulses generate shock pressure, further aiding densification.
-
Advantages of SPS:
- Rapid Densification: SPS achieves full densification in minutes, significantly faster than conventional sintering.
- Lower Sintering Temperatures: SPS can densify materials at temperatures 200–500°C lower than traditional methods.
- Energy Efficiency: Direct heating and short processing times reduce energy consumption.
- Material Preservation: High heating and cooling rates help maintain the properties of nano-powders in the final product.
-
Applications:
- SPS is widely used for sintering advanced ceramics, metals, composites, and nanomaterials.
- It is particularly beneficial for materials that require high density and fine microstructure control.
-
Environmental and Economic Benefits:
- The process is environmentally friendly due to reduced energy usage and shorter processing times.
- Lower sintering temperatures and faster processing reduce overall production costs.
-
Comparison with Conventional Sintering:
- Unlike hot pressing, which relies on radiation heating, SPS uses direct Joule heating and plasma activation.
- SPS achieves higher densities and better material properties in a fraction of the time required by conventional methods.
-
Challenges and Limitations:
- The high cost of SPS equipment and the need for specialized training can be barriers to adoption.
- The process may not be suitable for all materials, particularly those sensitive to rapid heating or high electric fields.
By combining mechanical pressure, electric fields, and thermal fields, SPS offers a unique and efficient approach to material densification, making it a valuable technique in advanced manufacturing and materials science.
Summary Table:
Aspect | Details |
---|---|
Principle | Uses pulsed DC to generate spark plasma, creating localized high temperatures (up to 10,000°C). |
Key Mechanisms | Plasma activation, Joule heating, and discharge shock pressure. |
Advantages | Rapid densification, lower sintering temperatures, energy efficiency, and material preservation. |
Applications | Advanced ceramics, metals, composites, and nanomaterials. |
Environmental Benefits | Reduced energy usage and shorter processing times. |
Challenges | High equipment cost and specialized training requirements. |
Ready to explore how Spark Plasma Sintering can transform your material processing? Contact us today to learn more!