The sputtering process is a vacuum-enabled technique used to deposit thin films of material onto a substrate. It involves creating a plasma by ionizing an inert gas (typically argon) in a vacuum chamber. The plasma generates high-energy ions that bombard a target material (cathode), causing atoms to be ejected from its surface. These ejected atoms travel through the chamber and deposit onto the substrate, forming a thin film with specific properties. The process is highly controlled, allowing for precise adjustments in film morphology, grain size, and density. Key steps include creating a vacuum, introducing inert gas, generating plasma, and accelerating ions to sputter the target material.
Key Points Explained:
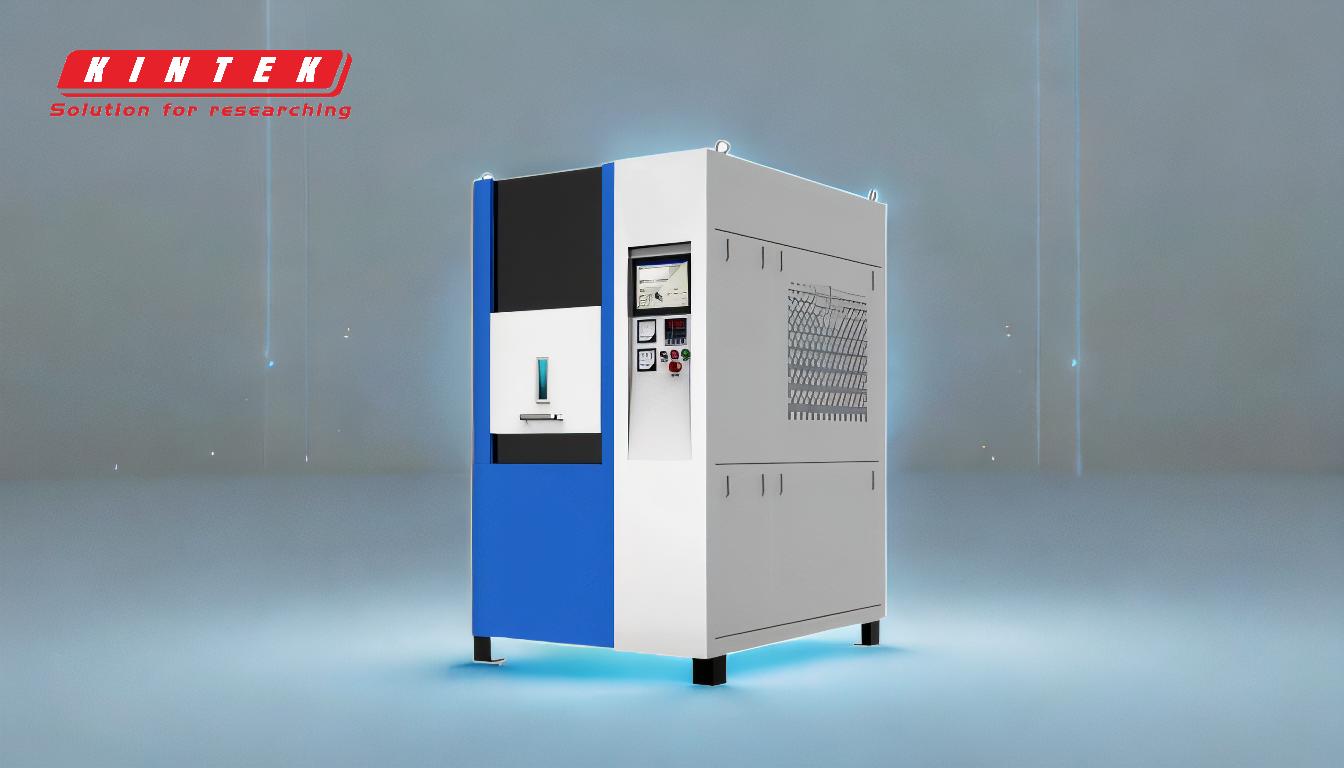
-
Vacuum Creation and Inert Gas Introduction:
- The process begins by evacuating the reaction chamber to a low pressure (around 1 Pa or lower) to remove moisture and impurities, ensuring a clean environment.
- An inert gas, typically argon, is introduced into the chamber to create a low-pressure atmosphere. This gas is essential for plasma generation.
-
Plasma Generation:
- A high voltage (3-5 kV) is applied to ionize the argon gas, creating a plasma composed of positively charged argon ions and free electrons.
- A magnetic field is often used to confine and enhance the plasma, increasing the efficiency of ion bombardment on the target material.
-
Ion Bombardment and Sputtering:
- The target material (cathode) is negatively charged, attracting the positively charged argon ions.
- These ions strike the target with high kinetic energy, dislodging atoms or molecules from its surface in a process called sputtering.
-
Transport and Deposition:
- The sputtered atoms form a vapor stream that travels through the vacuum chamber.
- These atoms deposit onto the substrate (anode) and condense, forming a thin film with desired properties such as reflectivity, electrical resistivity, or ionic resistivity.
-
Control Over Film Properties:
- The sputtering process allows for precise control over film characteristics, including morphology, grain orientation, grain size, and density.
- Parameters such as pressure, temperature, voltage, and magnetic field strength can be adjusted to achieve specific film properties.
-
Applications and Advantages:
- Sputtering is widely used in industries requiring precision coatings, such as semiconductors, optics, and electronics.
- The process is highly accurate, reproducible, and capable of depositing a wide range of materials, including metals, alloys, and ceramics.
By following these steps, the sputtering process enables the creation of high-quality thin films with tailored properties, making it a critical technology in modern manufacturing and research.
Summary Table:
Step | Description |
---|---|
Vacuum Creation | Evacuate the chamber to low pressure (~1 Pa) to remove impurities. |
Inert Gas Introduction | Introduce argon gas for plasma generation. |
Plasma Generation | Apply high voltage (3-5 kV) to ionize argon, creating a plasma. |
Ion Bombardment | Positively charged argon ions strike the target, ejecting atoms. |
Transport & Deposition | Sputtered atoms deposit onto the substrate, forming a thin film. |
Control Over Film Properties | Adjust parameters like pressure, temperature, and voltage for desired properties. |
Applications | Used in semiconductors, optics, and electronics for precision coatings. |
Discover how the sputtering process can elevate your manufacturing—contact our experts today!