Heat treatment is a critical process in metallurgy and materials science, aimed at altering the physical and sometimes chemical properties of materials, primarily metals. The standard heat treatment process involves controlled heating and cooling of materials to achieve desired characteristics such as increased hardness, improved ductility, or enhanced strength. The process is essential in industries like automotive, aerospace, and manufacturing, where material performance is paramount. Below, we break down the key aspects of the standard heat treatment process.
Key Points Explained:
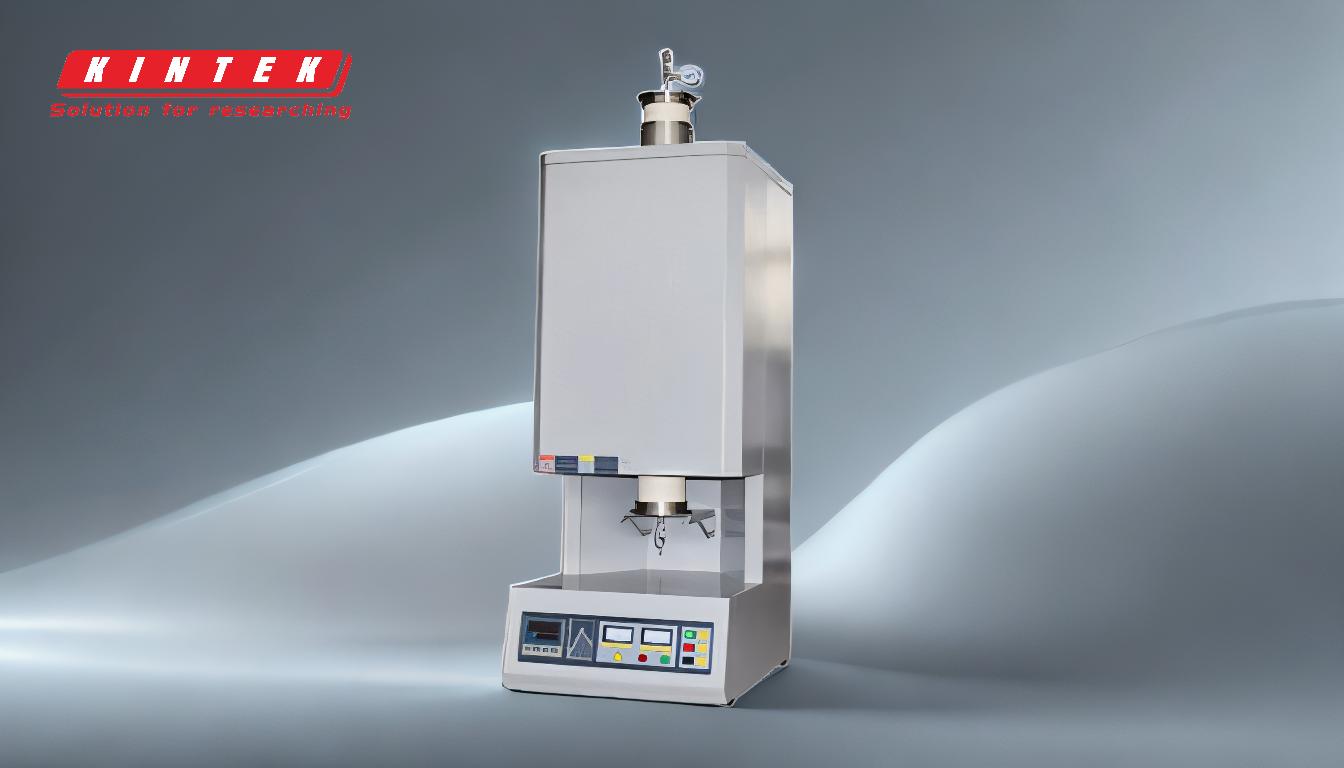
-
Definition and Purpose of Heat Treatment:
- Heat treatment involves heating materials, typically metals, to specific temperatures and then cooling them under controlled conditions.
- The primary goal is to improve material properties such as hardness, strength, toughness, and wear resistance.
- It can also relieve internal stresses, improve machinability, and enhance electrical or magnetic properties.
-
Key Stages of Heat Treatment:
- Heating: The material is heated to a predetermined temperature, which varies depending on the material and desired outcome.
- Soaking: The material is held at the target temperature for a specific duration to ensure uniform heating and structural changes.
- Cooling: The material is cooled at a controlled rate, which can involve quenching (rapid cooling), air cooling, or furnace cooling, depending on the desired properties.
-
Common Heat Treatment Processes:
- Annealing: This process involves heating the material to a specific temperature and then slowly cooling it to soften the material, improve ductility, and reduce internal stresses.
- Hardening: The material is heated and then rapidly cooled (quenched) to increase hardness and strength. This is often followed by tempering to reduce brittleness.
- Tempering: After hardening, the material is reheated to a lower temperature and then cooled to improve toughness and reduce brittleness.
- Normalizing: Similar to annealing but involves cooling in air to refine the grain structure and improve mechanical properties.
- Case Hardening: This process hardens the surface of the material while maintaining a softer core, enhancing wear resistance.
-
Factors Influencing Heat Treatment:
- Material Composition: Different alloys and metals require specific heat treatment temperatures and cooling rates.
- Heating Rate: The speed at which the material is heated can affect the final properties.
- Cooling Rate: Rapid cooling (quenching) increases hardness, while slow cooling (annealing) improves ductility.
- Atmosphere Control: The environment during heating (e.g., vacuum, inert gas) can prevent oxidation and other surface defects.
-
Applications of Heat Treatment:
- Automotive Industry: Used to strengthen engine components, gears, and axles.
- Aerospace Industry: Enhances the performance of turbine blades and structural components.
- Tool Manufacturing: Improves the durability and cutting ability of tools.
- Construction: Strengthens steel beams and reinforcements.
-
Challenges in Heat Treatment:
- Distortion: Uneven heating or cooling can cause warping or cracking.
- Oxidation: Exposure to air during heating can lead to surface degradation.
- Energy Consumption: High-temperature processes require significant energy, impacting costs and sustainability.
By understanding these key points, purchasers of equipment and consumables can make informed decisions about the heat treatment processes and materials that best suit their needs. Proper heat treatment ensures that materials meet the required specifications for strength, durability, and performance, making it a vital step in manufacturing and engineering applications.
Summary Table:
Aspect | Details |
---|---|
Definition | Controlled heating and cooling to alter material properties. |
Key Stages | Heating, Soaking, Cooling. |
Common Processes | Annealing, Hardening, Tempering, Normalizing, Case Hardening. |
Influencing Factors | Material Composition, Heating Rate, Cooling Rate, Atmosphere Control. |
Applications | Automotive, Aerospace, Tool Manufacturing, Construction. |
Challenges | Distortion, Oxidation, Energy Consumption. |
Optimize your material performance with expert heat treatment solutions—contact us today!