Iron sintering is a critical process in metallurgy, where iron ore particles are heated to high temperatures to form a cohesive, low-porosity material. The temperature range for iron sintering typically falls between 1250-1350 °C, which is high enough to facilitate particle bonding through diffusion but remains below the melting point of iron to avoid liquefaction. This process is carried out in a sintering furnace, where temperature control is essential to ensure the desired density, strength, and porosity of the final product. The sintering process involves several stages, including composition, compression, heating, and cooling, each of which is carefully controlled to achieve optimal results.
Key Points Explained:
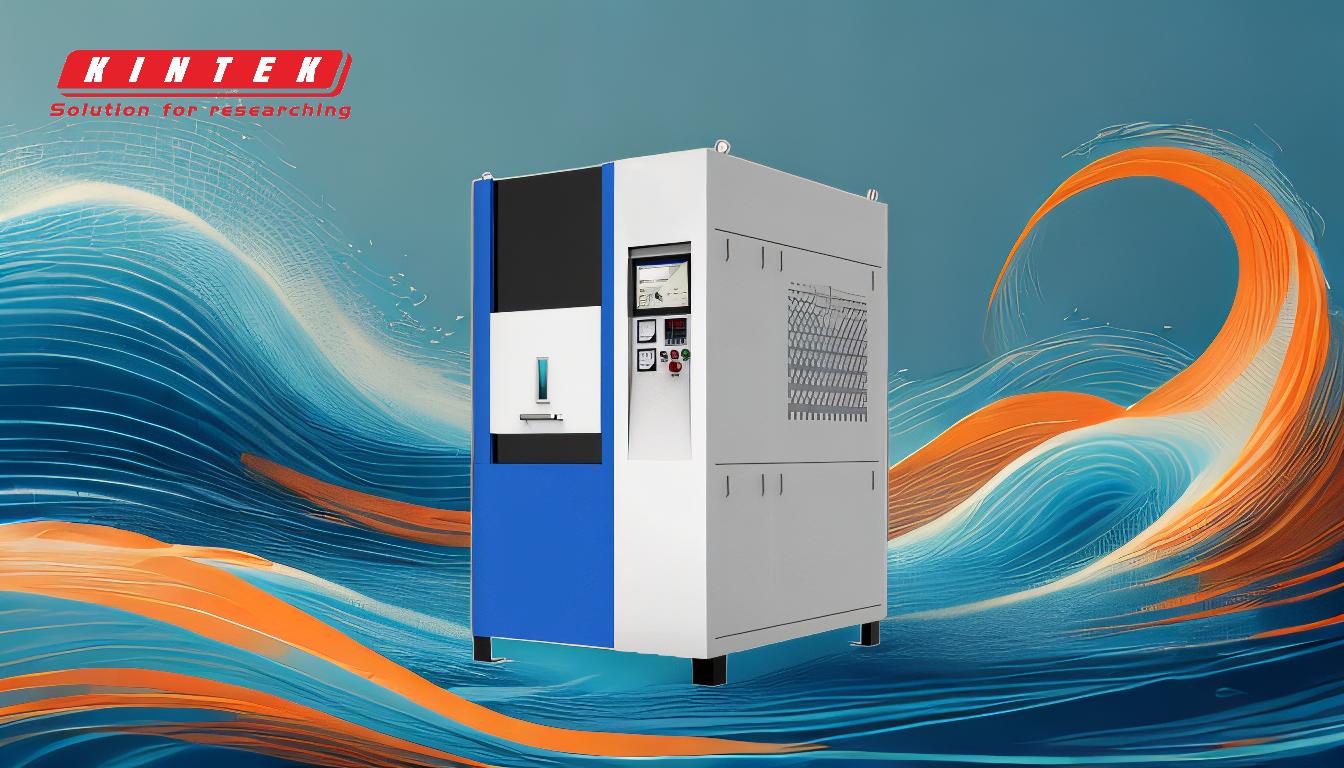
-
Temperature Range for Iron Sintering
- The temperature for iron sintering typically ranges between 1250-1350 °C.
- This range is chosen because it allows for sufficient diffusion of atoms across particle boundaries, enabling the particles to bond and form a cohesive structure.
- The temperature must remain below the melting point of iron to prevent complete liquefaction, which would disrupt the sintering process.
-
Role of Temperature in Sintering
- Temperature is a critical factor in sintering because it directly influences diffusion mechanisms, such as grain boundary diffusion and bulk diffusion.
- High temperatures promote the movement of atoms, leading to the formation of "necks" between particles, which are essential for densification and strength.
- However, excessively high temperatures or prolonged heating times can lead to defects like scorching or reduced product properties.
-
Stages of the Sintering Process
- Composition: The raw materials, including iron ore and coupling agents, are mixed to create a uniform blend.
- Compression: The powder is pressed into the desired shape using controlled pressure to eliminate voids and ensure uniformity.
- Heating: The compacted material is heated in a sintering furnace to the required temperature, where particle bonding occurs through diffusion.
- Cooling: The sintered product is cooled to solidify into a rigid and cohesive structure.
-
Importance of Temperature Control
- Temperature control is vital to achieve the desired properties of the sintered product, such as density, porosity, strength, and hardness.
- Variations in temperature or heating time can significantly impact the final product's quality. For example, low temperatures may result in incomplete sintering, while excessively high temperatures can cause defects.
-
Factors Influencing Sintering Temperature
- The specific temperature and heating time depend on factors such as the type of iron ore, particle size, material composition, and the desired density of the final product.
- The sintering environment, including the atmospheric conditions within the furnace, also plays a crucial role in determining the optimal temperature.
-
Impact of Sintering Temperature on Product Properties
- Porosity and Density: Higher sintering temperatures generally reduce porosity and increase density, resulting in a stronger and more durable product.
- Strength and Hardness: Proper temperature control ensures that the sintered product achieves the desired mechanical properties without compromising its structural integrity.
- Defects: Inadequate temperature control can lead to issues such as incomplete sintering, scorching, or degraded properties.
-
Applications of Sintering in Metallurgy
- Sintering is widely used in the production of iron and steel products, where it enhances the material's strength, durability, and performance.
- The process is also applied in other industries, such as ceramics and powder metallurgy, where controlled heating is essential for achieving specific material properties.
In summary, the temperature of iron sintering is carefully controlled within the range of 1250-1350 °C to ensure optimal particle bonding and material properties. The process involves multiple stages, each of which is critical to the final product's quality. Temperature control, along with factors like particle size and material composition, plays a vital role in determining the success of the sintering process.
Summary Table:
Key Aspect | Details |
---|---|
Temperature Range | 1250-1350 °C |
Purpose | Facilitates particle bonding through diffusion without liquefaction |
Stages of Sintering | Composition, Compression, Heating, Cooling |
Critical Factors | Temperature control, particle size, material composition |
Impact on Product | Density, porosity, strength, hardness, and defect prevention |
Applications | Iron and steel production, ceramics, powder metallurgy |
Ensure your sintering process achieves optimal results—contact our experts today for tailored solutions!