Thermal debinding is a critical step in the manufacturing process of metal or ceramic parts, particularly in powder metallurgy and additive manufacturing. The temperature range for thermal debinding typically falls between 200°C and 550°C, depending on the binder material and the metal or ceramic being processed. This process is carried out in a temperature-controlled environment using relatively inexpensive equipment. However, it often involves a long processing cycle and results in parts with poor "brown" strength, meaning the parts are fragile before sintering. The specific temperature and cycle depend on the material properties, such as whether the material requires sintering under specific gases like hydrogen or nitrogen.
Key Points Explained:
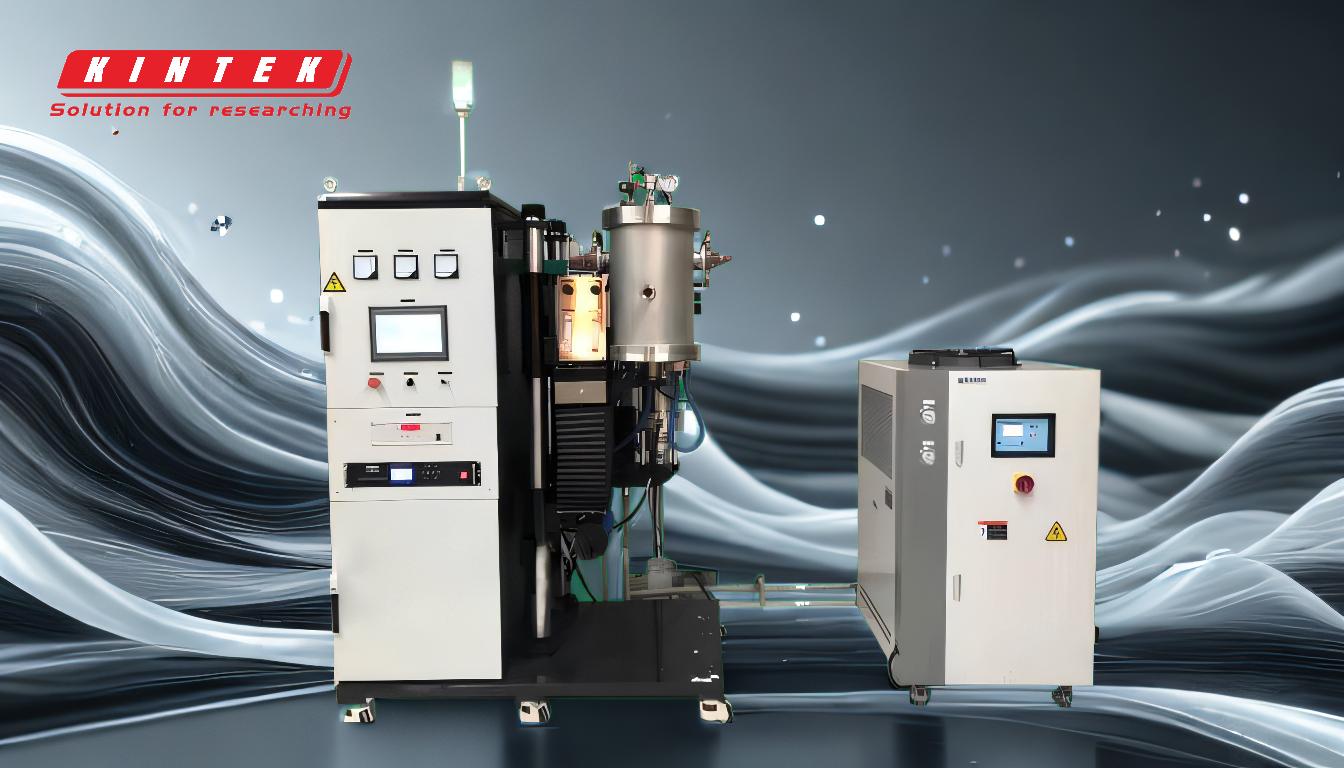
-
Temperature Range for Thermal Debinding:
- Thermal debinding generally occurs between 200°C and 550°C.
- This range is not fixed and depends on the binder material and the metal or ceramic being processed. For example, different binders decompose at different temperatures, and metals or ceramics may have specific requirements to avoid damage during the debinding process.
-
Dependence on Binder and Material:
- The temperature is highly dependent on the binder material used in the process. Binders are organic compounds that hold the powder particles together, and their decomposition temperature dictates the debinding temperature.
- The metal or ceramic material also influences the temperature. For instance, oxide ceramics may not require specific gases, while nitrides, carbides, and metals often need sintering under controlled atmospheres like hydrogen or nitrogen.
-
Temperature-Controlled Environment:
- Thermal debinding is performed in a temperature-controlled environment to ensure uniform heating and avoid thermal shocks that could damage the parts.
- This environment is typically achieved using furnaces or ovens designed for precise temperature regulation.
-
Equipment and Cost:
- The equipment used for thermal debinding is relatively inexpensive compared to other stages in the manufacturing process, such as sintering.
- However, the process requires careful monitoring to ensure the temperature remains within the optimal range for the specific material and binder.
-
Processing Cycle and Brown Strength:
- Thermal debinding has a long processing cycle due to the need for gradual heating to avoid rapid binder decomposition, which could cause defects like cracking or blistering.
- After debinding, the parts have poor "brown" strength, meaning they are fragile and require careful handling before sintering. This is because the binder, which provided structural integrity, has been removed.
-
Material-Specific Considerations:
- For oxide ceramics, thermal debinding can often be performed in air, as these materials do not require protective atmospheres.
- For nitrides, carbides, and metals, debinding is often followed by sintering under gases like hydrogen or nitrogen to achieve fully dense parts. This adds complexity to the process and may influence the debinding temperature.
-
Importance of Controlled Atmosphere:
- In some cases, a controlled atmosphere is necessary during debinding to prevent oxidation or other chemical reactions that could degrade the material.
- This is particularly important for materials that are sensitive to oxygen or moisture.
-
Trade-Offs in Thermal Debinding:
- While thermal debinding is cost-effective in terms of equipment, the long processing time and fragility of debound parts are significant trade-offs.
- Manufacturers must balance these factors when designing the debinding process to ensure high-quality final products.
By understanding these key points, equipment and consumable purchasers can make informed decisions about the materials and processes required for thermal debinding, ensuring optimal results in their manufacturing workflows.
Summary Table:
Key Aspect | Details |
---|---|
Temperature Range | 200°C–550°C, depending on binder and material. |
Binder Dependence | Organic binders decompose at specific temperatures. |
Material Influence | Oxide ceramics, nitrides, carbides, and metals have unique requirements. |
Equipment | Inexpensive furnaces or ovens with precise temperature control. |
Processing Cycle | Long cycle to avoid defects like cracking or blistering. |
Brown Strength | Fragile parts post-debinding; careful handling required before sintering. |
Controlled Atmosphere | Necessary for materials sensitive to oxidation or moisture. |
Trade-Offs | Cost-effective equipment but long processing time and fragile parts. |
Optimize your thermal debinding process with expert guidance—contact us today!