Thin film production involves a variety of techniques designed to deposit thin layers of material onto a substrate, with precise control over thickness and properties. These methods can be broadly categorized into chemical, physical, and electrically-based processes, each suited for specific applications and industries. Common techniques include chemical vapor deposition (CVD), physical vapor deposition (PVD), spin coating, and sputtering, among others. These methods are used to create thin films for applications ranging from semiconductors and flexible solar cells to organic light-emitting diodes (OLEDs). The choice of method depends on the desired film properties, substrate material, and application requirements.
Key Points Explained:
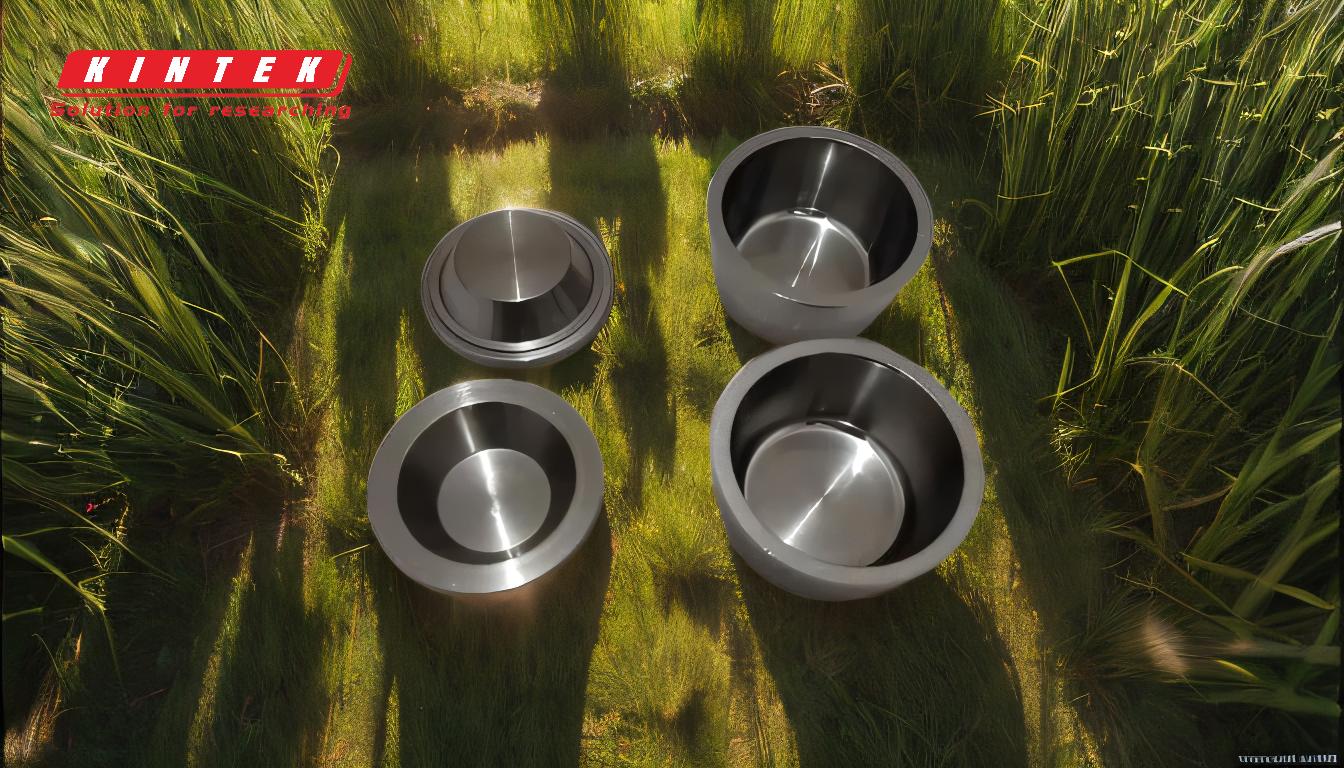
-
Overview of Thin Film Production Methods:
- Thin film production involves depositing thin layers of material onto a substrate, often at the nanometer or micrometer scale.
- The methods can be categorized into chemical, physical, and electrically-based processes, each with its own advantages and limitations.
- The choice of method depends on factors such as the material being deposited, the substrate, and the desired film properties.
-
Chemical Methods:
- Chemical Vapor Deposition (CVD): A process where a substrate is exposed to volatile precursors, which react or decompose on the substrate surface to form a thin film. CVD is widely used in semiconductor manufacturing and for creating high-quality, uniform films.
- Chemical Deposition: Involves chemical reactions to deposit thin films, often used for creating polymer-based films for applications like flexible solar cells and OLEDs.
-
Physical Methods:
- Physical Vapor Deposition (PVD): Includes techniques like evaporation and sputtering, where material is physically removed from a source and deposited onto a substrate. PVD is commonly used for creating metal and ceramic thin films.
- Spin Coating: A technique where a liquid precursor is applied to a substrate, which is then spun at high speed to spread the material evenly and form a thin film. This method is widely used in the production of polymer films and coatings.
- Magnetron Sputtering: A type of PVD where a plasma is used to sputter material from a target onto a substrate. This method is known for its ability to produce high-quality, uniform films with precise control over thickness.
-
Electrically-Based Methods:
- Plasma Sputtering: A technique that uses plasma to sputter material from a target onto a substrate. This method is often used in the production of thin films for electronic devices and coatings.
- Molecular Beam Epitaxy (MBE): A highly controlled method where beams of atoms or molecules are directed at a substrate to grow thin films layer by layer. MBE is used in the production of high-quality semiconductor films.
-
Other Techniques:
- Drop Casting: A simple method where a solution containing the material to be deposited is dropped onto a substrate and allowed to dry, forming a thin film. This method is often used for research purposes due to its simplicity.
- Oil Bathing: A technique where a substrate is immersed in a solution or oil bath to deposit a thin film. This method is less common but can be used for specific applications.
- Langmuir-Blodgett Film Formation: A method used to create highly ordered thin films by transferring monolayers from a liquid surface onto a solid substrate. This technique is used for creating films with precise molecular arrangements.
-
Applications of Thin Film Production:
- Semiconductors: Thin films are crucial in the production of semiconductor devices, where precise control over film thickness and composition is essential.
- Flexible Electronics: Thin films are used in the production of flexible solar cells, OLEDs, and other electronic devices that require lightweight, flexible materials.
- Optical Coatings: Thin films are used to create anti-reflective coatings, mirrors, and other optical components.
- Protective Coatings: Thin films are used to provide protective layers on surfaces, such as scratch-resistant coatings on glass or corrosion-resistant coatings on metals.
-
Advantages and Limitations:
- Advantages: Thin film production methods allow for precise control over film thickness, composition, and properties, making them suitable for a wide range of applications. They also enable the production of films with unique properties, such as flexibility, transparency, and conductivity.
- Limitations: Some methods, such as CVD and MBE, require specialized equipment and can be expensive. Other methods, like drop casting, may not produce films with the same level of uniformity and quality as more advanced techniques.
In summary, thin film production encompasses a wide range of techniques, each with its own set of advantages and limitations. The choice of method depends on the specific application, desired film properties, and available resources. These methods have enabled the development of advanced materials and devices, from semiconductors to flexible electronics, and continue to play a crucial role in modern technology.
Summary Table:
Category | Techniques | Applications |
---|---|---|
Chemical Methods | Chemical Vapor Deposition (CVD), Chemical Deposition | Semiconductors, polymer-based films for flexible solar cells and OLEDs |
Physical Methods | Physical Vapor Deposition (PVD), Spin Coating, Magnetron Sputtering | Metal and ceramic thin films, polymer coatings |
Electrical Methods | Plasma Sputtering, Molecular Beam Epitaxy (MBE) | Electronic devices, high-quality semiconductor films |
Other Techniques | Drop Casting, Oil Bathing, Langmuir-Blodgett Film Formation | Research purposes, specific applications, precise molecular arrangements |
Applications | Semiconductors, Flexible Electronics, Optical Coatings, Protective Coatings | Advanced materials, lightweight devices, anti-reflective coatings, scratch resistance |
Need help selecting the right thin film production method for your application? Contact our experts today!