The vacuum evaporation Physical Vapor Deposition (PVD) method is a widely used technique for depositing thin films onto substrates. It involves the transformation of a solid material into vapor through heating in a high vacuum environment, followed by condensation of the vapor onto a substrate to form a thin film. This method is simple, cost-effective, and has been utilized for decades in various applications, including optical coatings, electronics, and decorative finishes. The process relies on resistive heating to evaporate the source material, ensuring high purity and uniformity of the deposited films.
Key Points Explained:
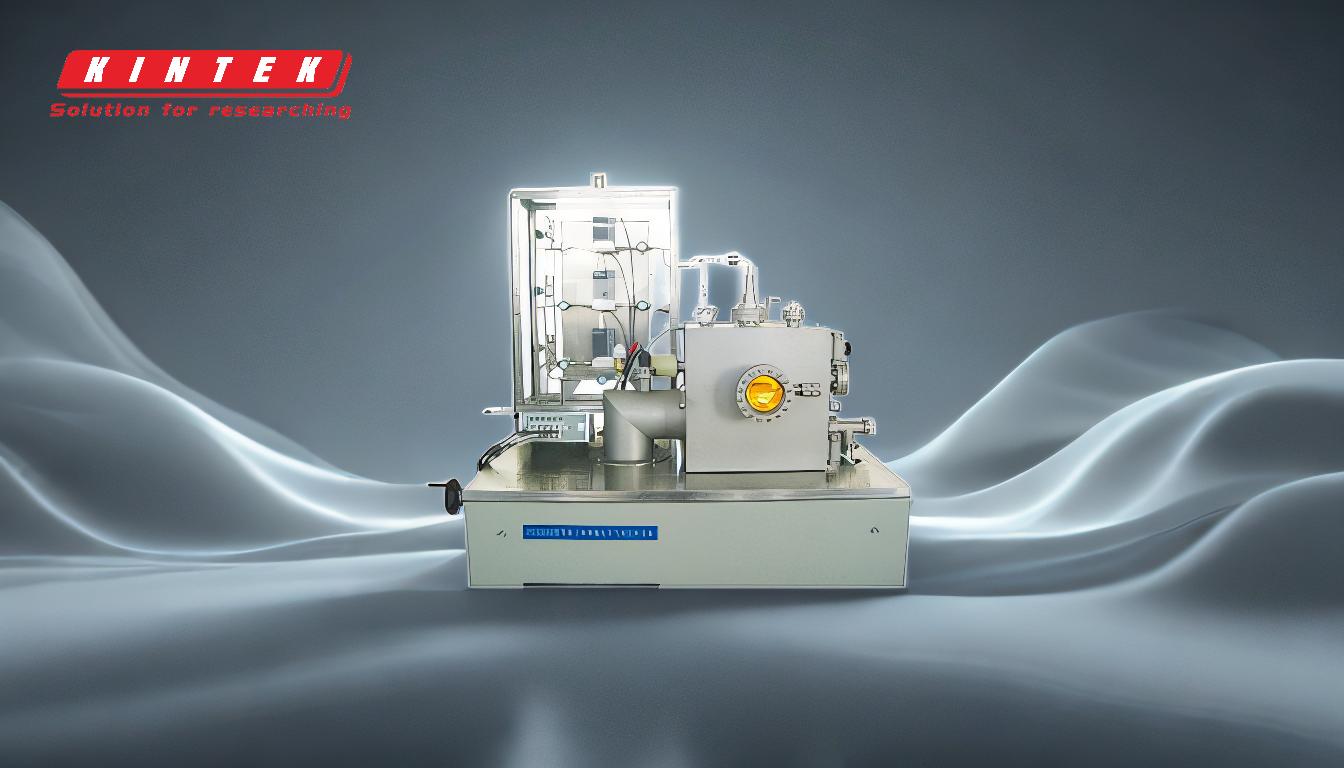
-
Definition and Process of Vacuum Evaporation PVD:
- Vacuum evaporation is a physical vapor deposition (PVD) technique where a solid material is heated in a high vacuum chamber until it evaporates. The vapor then travels through the vacuum and condenses onto a substrate, forming a thin film.
- The process involves three main steps:
- Evaporation: The source material is heated to its evaporation point, typically using resistive heating, electron beams, or other methods.
- Transport: The vaporized material travels through the vacuum environment to the substrate.
- Condensation: The vapor condenses on the substrate, forming a thin, uniform film.
-
Applications of Vacuum Evaporation PVD:
- This method is versatile and used in various industries:
- Optical Coatings: For mirrors, lenses, and anti-reflective coatings.
- Electronics: In the production of semiconductors, solar cells, and thin-film transistors.
- Decorative Finishes: For toys, cosmetics, and shoe heels.
- Functional Coatings: In aerospace, automotive, and medical devices for wear resistance and corrosion protection.
- This method is versatile and used in various industries:
-
Advantages of Vacuum Evaporation PVD:
- High Purity: The vacuum environment minimizes contamination, resulting in high-purity films.
- Uniformity: The process allows for precise control over film thickness and uniformity.
- Cost-Effectiveness: It is relatively simple and cost-effective compared to other PVD methods.
- Versatility: Suitable for a wide range of materials, including metals, alloys, and ceramics.
-
Specialized Forms of Evaporation PVD:
- Plasma Spraying: A variant of evaporation PVD where a plasma flame is used to melt or evaporate coating material in powder form, creating thick films on substrates.
- Electron Beam Evaporation: Uses an electron beam to heat the source material, allowing for higher evaporation rates and better control over deposition.
-
Historical Context:
- Vacuum evaporation has been used since the 19th century, particularly for creating mirrors by depositing silver onto glass. This historical application highlights the method's reliability and effectiveness.
-
Challenges and Considerations:
- High Vacuum Requirements: The process requires a high vacuum environment, which can be expensive to maintain.
- Material Limitations: Not all materials can be easily evaporated, and some may require specialized equipment.
- Substrate Compatibility: The substrate must withstand the high temperatures and vacuum conditions of the process.
In conclusion, vacuum evaporation PVD is a foundational and versatile method for thin film deposition, offering high purity, uniformity, and cost-effectiveness. Its applications span multiple industries, and its historical use underscores its reliability. While there are challenges, such as high vacuum requirements and material limitations, the method remains a cornerstone of modern coating technologies.
Summary Table:
Aspect | Details |
---|---|
Process | Evaporation, transport, and condensation of materials in a high vacuum. |
Applications | Optical coatings, electronics, decorative finishes, functional coatings. |
Advantages | High purity, uniformity, cost-effectiveness, versatility. |
Specialized Forms | Plasma spraying, electron beam evaporation. |
Challenges | High vacuum requirements, material limitations, substrate compatibility. |
Discover how vacuum evaporation PVD can enhance your projects—contact our experts today!