Induction furnaces are versatile equipment used for melting metals, and their voltage limits are determined by their design, power supply configuration, and operational requirements. The voltage limit for an induction furnace typically depends on the power supply system, the furnace's capacity, and the specific application. For instance, a high-frequency induction heating furnace might operate at a three-phase AC 380V 50Hz with a 60A air switch, indicating a voltage limit of 380V. However, the actual voltage limit can vary based on the furnace's design, the material being processed, and the required melting speed. Understanding the voltage limit is crucial for ensuring safe and efficient operation.
Key Points Explained:
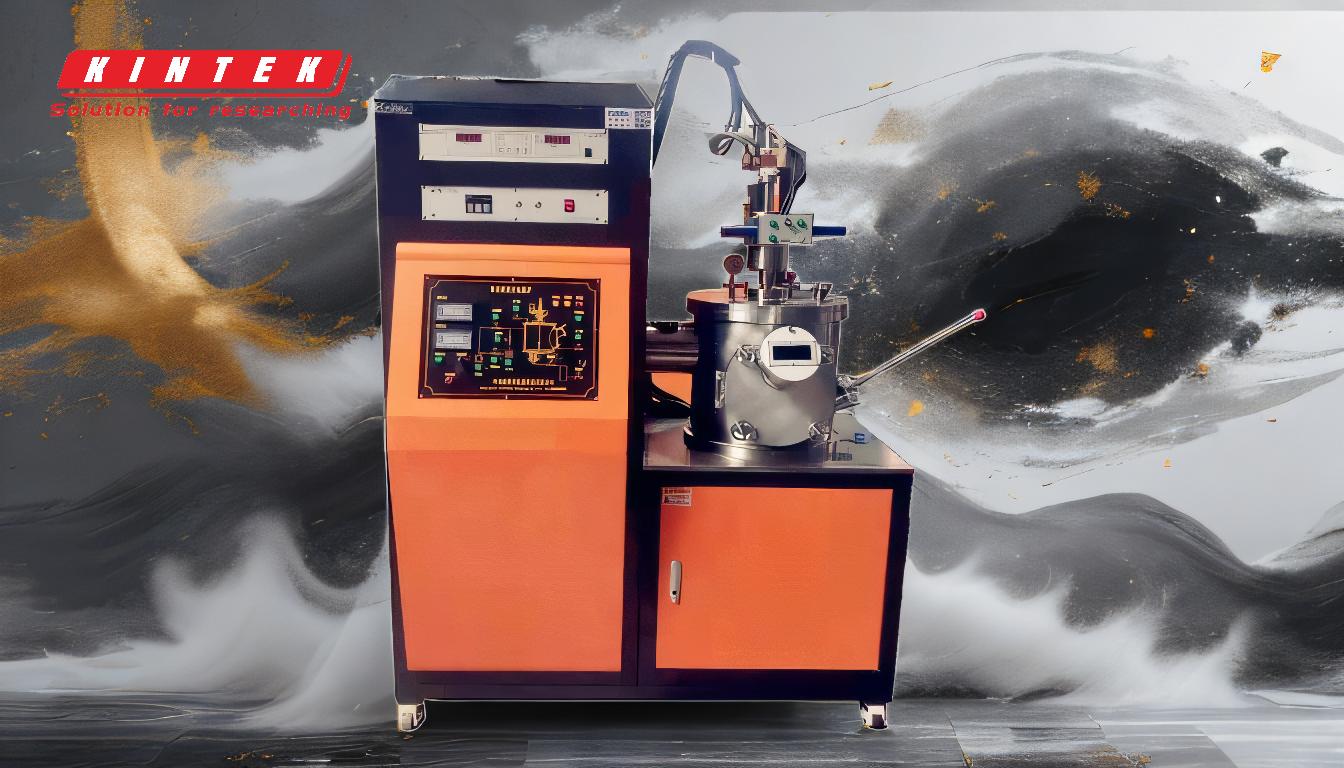
-
Voltage Limit in Induction Furnaces:
- The voltage limit for an induction furnace is typically determined by its power supply configuration. For example, a high-frequency induction heating furnace operates at a three-phase AC 380V 50Hz, indicating a voltage limit of 380V.
- The voltage limit ensures that the furnace operates within safe electrical parameters, preventing overheating or electrical failures.
-
Power Supply and Voltage Relationship:
- The power supply of an induction furnace is designed to work within specific voltage ranges. For instance, the mentioned furnace has a maximum input power of 15KW, which is directly related to the voltage and current (380V and 60A).
- The voltage limit is crucial for maintaining the furnace's efficiency and ensuring that the induction coil and other components operate within their designed parameters.
-
Frequency and Voltage Considerations:
- The operating frequency of an induction furnace ranges from utility frequency (50 or 60 Hz) to 400 kHz or higher. Higher frequencies are typically used for smaller volumes of melts due to the skin depth effect.
- The voltage limit must be compatible with the operating frequency to ensure effective heating and melting of the material.
-
Design and Operational Factors:
- The design of the induction furnace, including the induction coil dimensions (e.g., outer diameter of Ø120mm, inner diameter of Ø110mm, and height of 50mm), influences the voltage limit.
- Operational factors such as the type of refractory materials used, the cleanliness and size of the charge, and the required melting speed also impact the voltage limit.
-
Safety and Efficiency:
- Operating within the voltage limit ensures the safety of the equipment and personnel. Exceeding the voltage limit can lead to electrical hazards, equipment damage, and inefficient melting processes.
- Proper voltage management contributes to the furnace's longevity and consistent performance, especially in continuous operation scenarios.
-
Flexibility in Power Supply:
- The power supply of an induction furnace can be adjusted flexibly, allowing it to work smoothly and steadily with 24-hour continuous operation. This flexibility is essential for meeting production demands while maintaining the voltage within safe limits.
Understanding the voltage limit in induction furnaces involves considering the power supply configuration, operating frequency, design parameters, and safety requirements. By adhering to the specified voltage limits, operators can ensure efficient, safe, and reliable furnace operation.
Summary Table:
Factor | Details |
---|---|
Voltage Limit | Typically 380V for high-frequency induction furnaces, varies by design. |
Power Supply | Three-phase AC 380V 50Hz with 60A air switch, max input power of 15KW. |
Operating Frequency | Ranges from 50/60 Hz to 400 kHz or higher, depending on application. |
Design Parameters | Induction coil dimensions: Ø120mm (outer), Ø110mm (inner), 50mm (height). |
Operational Factors | Refractory materials, charge size, and melting speed impact voltage limits. |
Safety & Efficiency | Operating within voltage limits prevents hazards and ensures longevity. |
Flexibility | Adjustable power supply for 24-hour continuous operation. |
Need help understanding induction furnace voltage limits? Contact our experts today for tailored solutions!