Thin film deposition is a critical process in semiconductor manufacturing, involving the application of a thin layer of material onto a substrate to enhance its properties for specific applications. This process is essential for creating microelectronic devices, such as transistors and integrated circuits, by forming conductive layers and insulating barriers. The main methods used are Chemical Vapour Deposition (CVD) and Physical Vapour Deposition (PVD), with CVD being more common in the semiconductor industry due to its high precision. Thin film deposition is also used in various other industries, including aerospace, optics, and biomedical fields, to modify surfaces for improved performance and protection.
Key Points Explained:
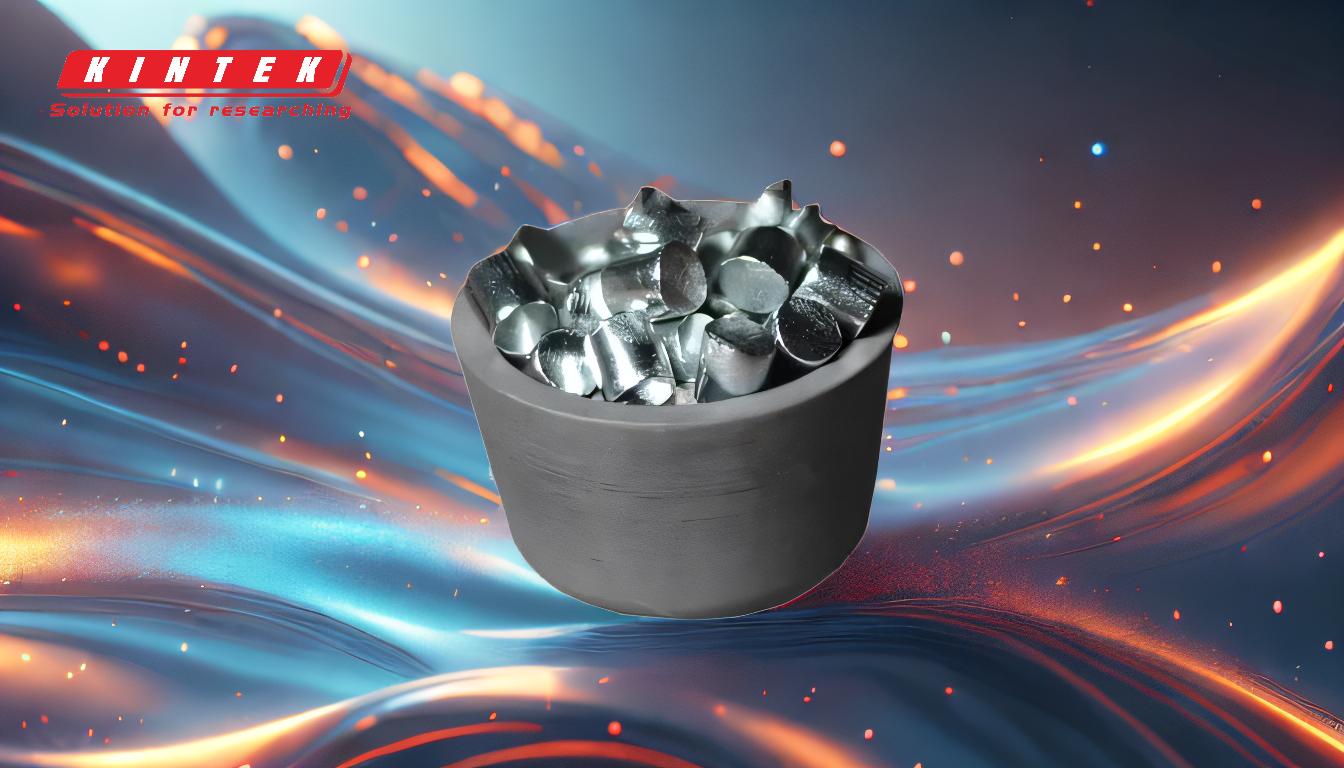
-
Definition and Importance of Thin Film Deposition:
- Thin film deposition involves applying a thin layer of material (such as a compound, metal, or oxide) onto a substrate to enhance its properties.
- This process is crucial in semiconductor manufacturing for creating microelectronic devices like transistors and integrated circuits.
- It is also used to form conductive layers and insulating barriers, which are essential for the functionality of these devices.
-
Applications in Semiconductor Manufacturing:
- Microelectronic Devices: Thin film deposition is used to create transistors and integrated circuits, which are the building blocks of modern electronics.
- Conductive Layers: The process forms conductive layers that allow for the flow of electrical current within the device.
- Insulating Barriers: It also creates insulating barriers that prevent electrical interference between different components.
-
Methods of Thin Film Deposition:
- Chemical Vapour Deposition (CVD): This method is widely used in the semiconductor industry due to its high precision. It involves the chemical reaction of gaseous precursors to form a solid film on the substrate.
- Physical Vapour Deposition (PVD): This method includes techniques like sputtering, thermal evaporation, and e-beam evaporation. PVD is known for producing high-purity coatings and is used in various applications beyond semiconductors.
-
Other Industrial Applications:
- Aerospace: Thin film deposition is used to create thermal and chemical barrier coatings that protect components from extreme environments.
- Optics: The process is used to apply optical coatings that improve the transmission, refraction, and reflection properties of lenses and other optical devices.
- Biomedical: Thin film deposition is used in the production of drug delivery systems and other biomedical devices.
-
Process Details:
- The thin film deposition process typically takes place in a vacuum chamber to ensure a controlled environment.
- The method used (CVD, PVD, etc.) determines the specific steps and conditions required to achieve the desired film properties.
- The thickness and composition of the deposited film can be precisely controlled to meet the requirements of the application.
-
Benefits and Challenges:
- Benefits: Thin film deposition enhances the properties of the substrate, making it suitable for specific applications. It allows for the creation of ultra-small structures and complex designs.
- Challenges: The process requires precise control over various parameters, such as temperature, pressure, and gas composition, to achieve the desired film properties. Additionally, the equipment and materials used can be expensive.
In summary, thin film deposition is a versatile and essential process in semiconductor manufacturing and various other industries. It enables the creation of advanced materials and devices by precisely controlling the properties of thin films applied to substrates. The choice of deposition method depends on the specific requirements of the application, with CVD and PVD being the most commonly used techniques in the semiconductor industry.
Summary Table:
Aspect | Details |
---|---|
Definition | Application of a thin material layer onto a substrate to enhance properties. |
Key Applications | Semiconductor manufacturing, aerospace, optics, biomedical devices. |
Main Methods | Chemical Vapour Deposition (CVD), Physical Vapour Deposition (PVD). |
Benefits | High precision, improved material properties, complex design capabilities. |
Challenges | Requires precise control; equipment and materials can be costly. |
Discover how thin film deposition can transform your applications—contact us today for expert guidance!