Thin film process technology is a critical and versatile field in modern manufacturing and electronics, involving the deposition of extremely thin layers of materials onto substrates to create functional or decorative coatings. These films, often just a few micrometers thick, are used in a wide range of applications, from semiconductors and solar cells to medical devices and consumer electronics. The technology leverages advanced deposition techniques, such as ion beam sputtering, to achieve precise control over film thickness and quality. Thin films exhibit unique properties due to their reduced structure, enabling innovations in industries like aerospace, automotive, and renewable energy. This technology is foundational to the development of compact, lightweight, and high-performance devices across multiple sectors.
Key Points Explained:
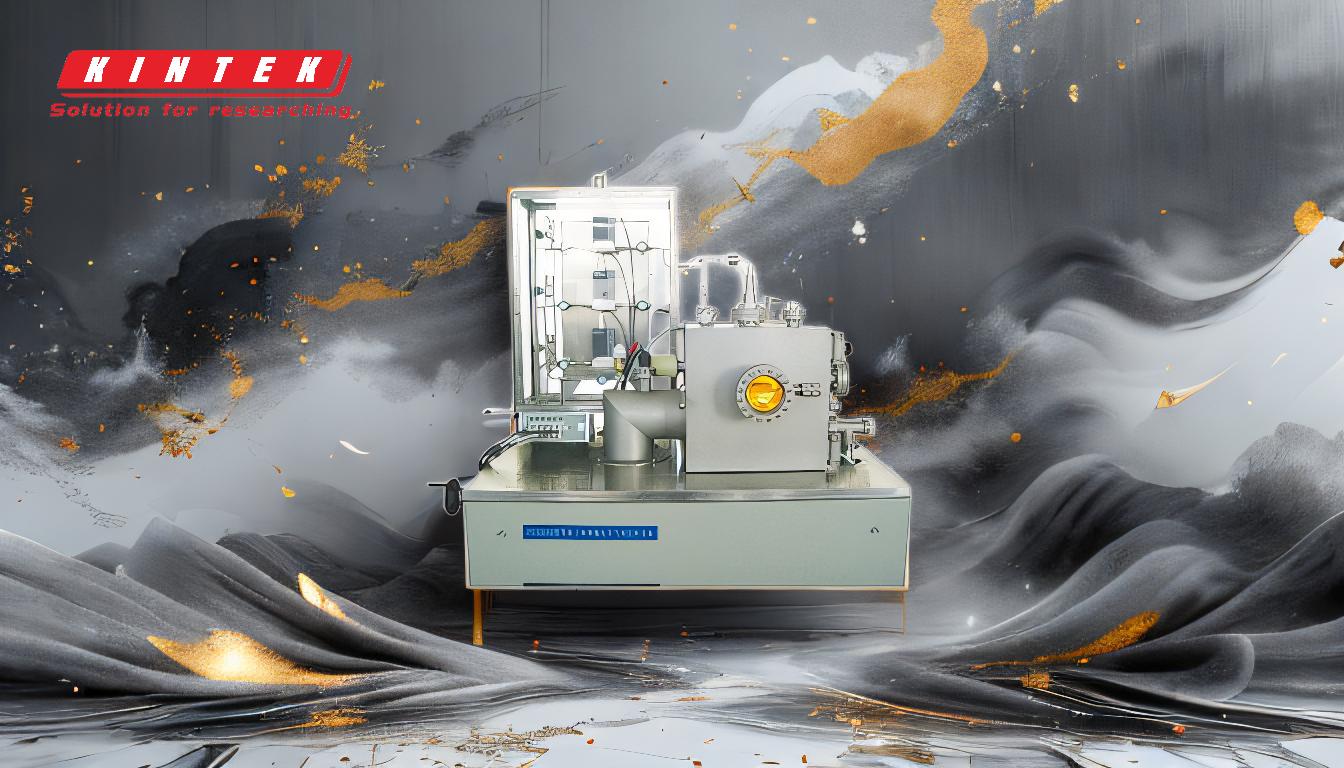
-
Definition of Thin Film Process Technology:
- Thin film process technology involves depositing ultra-thin layers of materials (ranging from nanometers to micrometers in thickness) onto substrates using specialized techniques.
- The "thin" aspect refers to the minimal thickness of the material layers, while the "film" aspect refers to the layered construction method.
- This technology is used to create functional or decorative coatings with unique properties.
-
Deposition Techniques:
- Ion Beam Sputtering: A high-precision method where an ion source sputters target materials (metallic or dielectric) onto a substrate, producing high-quality films with exact thickness control.
- Other common techniques include chemical vapor deposition (CVD), physical vapor deposition (PVD), and atomic layer deposition (ALD).
- These methods ensure uniformity, adhesion, and precise control over film properties.
-
Applications of Thin Film Technology:
- Semiconductors and Electronics: Used in micro-electromechanical systems (MEMS), thin-film transistors, and integrated circuits.
- Photovoltaics: Essential for manufacturing solar cells and cost-efficient photovoltaic systems.
- Optical Coatings: Applied in antireflective, reflective, and self-cleaning glass.
- Energy Storage: Used in thin-film batteries for compact and lightweight energy solutions.
- Medical Devices: Enables the creation of biocompatible coatings and sensors.
- Consumer Electronics: Found in OLED displays, foldable smartphones, and smartwatches.
- Aerospace and Automotive: Provides thermal barriers, corrosion-resistant coatings, and lightweight materials.
-
Unique Properties of Thin Films:
- Thin films exhibit unique properties due to their reduced structure, which alters the surface-to-volume ratio compared to bulk materials.
- These properties include enhanced hardness, low friction, thermal resistance, and chemical degradation resistance.
- Thin films can also manipulate electromagnetic radiation, making them useful in optical and absorptive coatings.
-
Materials Used in Thin Film Technology:
- Metals: Aluminum, chromium, tungsten, and refractory metals.
- Dielectrics: Silicon dioxide, aluminum oxide.
- Ceramics: Titanium nitride (TiN), diamond-like carbon (DLC).
- Compound Semiconductors: Gallium arsenide (GaAs), germanium.
- Functional Materials: Superconductors, photosensitive, and thermosensitive materials.
-
Advantages of Thin Film Technology:
- Precision: Enables the creation of films with exact thickness and composition.
- Versatility: Applicable across a wide range of industries and materials.
- Miniaturization: Reduces the size and weight of devices, enabling compact designs.
- Performance: Enhances the functionality of materials, such as hardness, corrosion resistance, and thermal barriers.
- Cost Efficiency: Offers cost-effective solutions for high-performance applications.
-
Future Trends and Innovations:
- Development of flexible and foldable electronics for wearable devices and foldable smartphones.
- Advancements in thin-film solar cells for renewable energy.
- Integration of thin films in biomedical applications, such as implantable sensors and drug delivery systems.
- Exploration of new materials, such as 2D materials (e.g., graphene), for next-generation thin-film devices.
In summary, thin film process technology is a foundational and transformative field that enables the creation of advanced materials and devices with unique properties. Its applications span numerous industries, driving innovation in electronics, energy, healthcare, and beyond. The precision, versatility, and performance of thin films make them indispensable in modern technology and manufacturing.
Summary Table:
Aspect | Details |
---|---|
Definition | Deposition of ultra-thin material layers (nanometers to micrometers thick). |
Deposition Techniques | Ion beam sputtering, CVD, PVD, ALD. |
Applications | Semiconductors, solar cells, medical devices, aerospace, and more. |
Unique Properties | Enhanced hardness, thermal resistance, and electromagnetic manipulation. |
Materials Used | Metals, dielectrics, ceramics, compound semiconductors, functional materials. |
Advantages | Precision, versatility, miniaturization, performance, and cost efficiency. |
Future Trends | Flexible electronics, thin-film solar cells, biomedical integration, 2D materials. |
Ready to explore how thin film technology can transform your industry? Contact us today for expert insights!