The vapour growth technique is a highly effective method for growing crystals, particularly for creating thin layers of metals, insulators, and semiconductors. This process involves depositing material from the vapour phase onto a substrate, resulting in crystals with exceptionally flat surfaces and minimal imperfections. Unlike other crystal growth methods, vapour growth offers unique advantages in terms of material purity and structural perfection, making it a preferred choice for applications requiring high-quality thin films.
Key Points Explained:
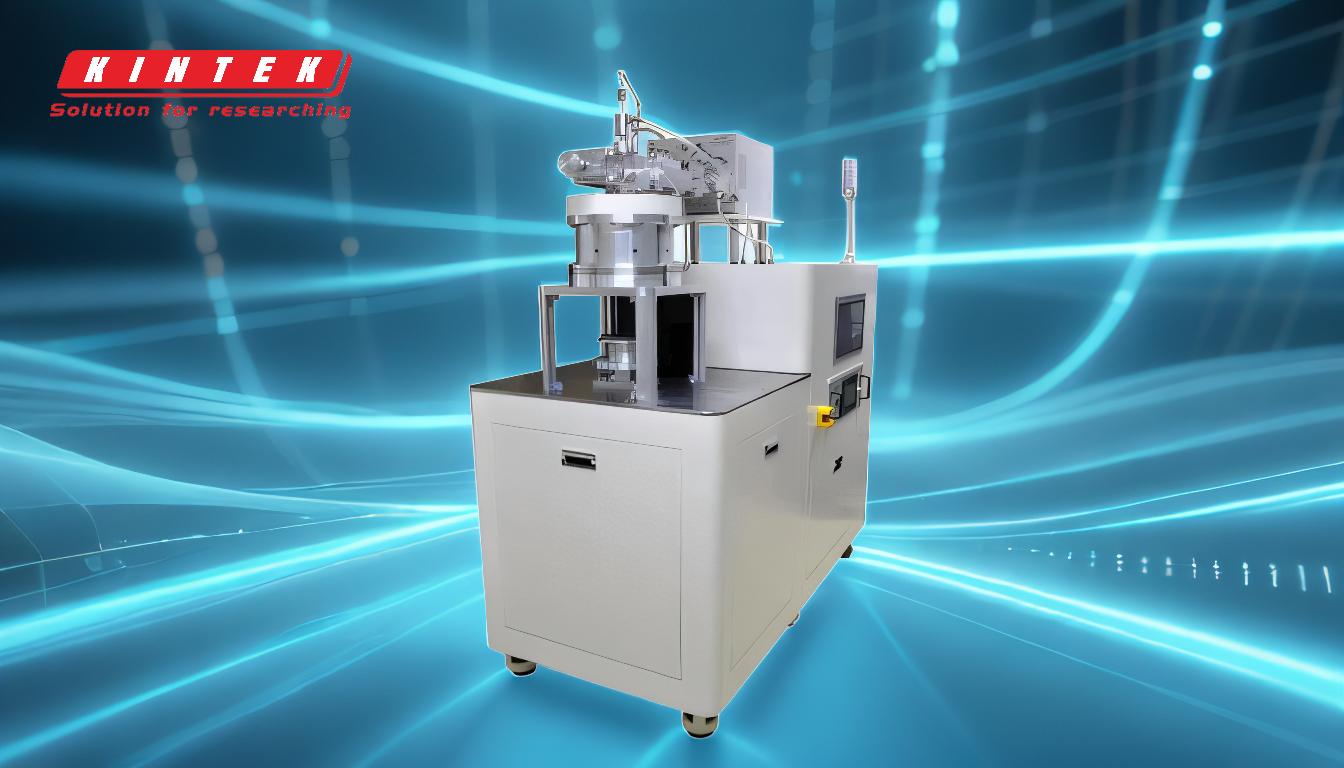
-
Definition of Vapour Growth Technique:
- The vapour growth technique is a process where materials are deposited from the vapour phase onto a substrate to form thin layers of crystals.
- It is widely used for growing high-quality crystals of metals, insulators, and semiconductors.
-
Advantages of Vapour Growth:
- Flat Surfaces: The crystals produced through this method often have perfectly flat external surfaces, which is crucial for many applications in electronics and optics.
- Minimal Imperfections: The technique results in fewer defects and imperfections compared to other crystal growth methods, leading to higher material quality.
- Material Versatility: It can be used to grow a wide range of materials, including metals, insulators, and semiconductors, making it versatile for various industries.
-
Applications of Vapour Growth:
- Semiconductor Industry: Vapour growth is extensively used in the fabrication of semiconductor devices, where high-quality thin films are essential for performance.
- Optoelectronics: The technique is employed in the production of optoelectronic devices, such as LEDs and laser diodes, where material purity and structural perfection are critical.
- Thin Film Coatings: It is also used for creating thin film coatings in various applications, including protective coatings and optical coatings.
-
Comparison with Other Techniques:
- Liquid Phase Epitaxy (LPE): While LPE is another common method for growing crystals, it often results in more defects and less control over the material properties compared to vapour growth.
- Molecular Beam Epitaxy (MBE): MBE offers high precision but is more complex and expensive than vapour growth, making vapour growth a more accessible option for many applications.
- Chemical Vapour Deposition (CVD): CVD is similar to vapour growth but often involves chemical reactions at the substrate surface, which can introduce impurities. Vapour growth, on the other hand, typically relies on physical deposition, leading to purer materials.
-
Process Details:
- Vapour Phase Formation: The material to be deposited is first vaporized, often through heating or chemical reactions.
- Deposition onto Substrate: The vapour is then directed onto a substrate, where it condenses and forms a thin layer of crystal.
- Control Parameters: Key parameters such as temperature, pressure, and deposition rate are carefully controlled to ensure the desired crystal quality and properties.
-
Challenges and Considerations:
- Temperature Control: Precise temperature control is crucial to avoid defects and ensure uniform deposition.
- Substrate Preparation: The substrate must be meticulously prepared to ensure proper adhesion and crystal growth.
- Material Purity: Ensuring the purity of the source material is essential to achieve high-quality crystals.
In summary, the vapour growth technique is a sophisticated method for growing high-quality crystals with flat surfaces and minimal imperfections. Its versatility and ability to produce superior materials make it a preferred choice in various high-tech industries, despite the challenges associated with precise control and substrate preparation.
Summary Table:
Aspect | Details |
---|---|
Definition | Deposits materials from vapour phase onto a substrate to form thin crystals. |
Advantages | Flat surfaces, minimal imperfections, material versatility. |
Applications | Semiconductor devices, optoelectronics, thin film coatings. |
Comparison | Superior to LPE, more accessible than MBE, purer than CVD. |
Process | Vapour phase formation, deposition onto substrate, precise control. |
Challenges | Temperature control, substrate preparation, material purity. |
Learn how the vapour growth technique can elevate your crystal growth process—contact our experts today!