Molding is a manufacturing process used to shape materials into desired forms by using a mold or pattern. The machines used for molding vary depending on the material being molded (e.g., plastic, metal, rubber, or ceramics) and the specific molding technique. Common types of molding machines include injection molding machines, blow molding machines, compression molding machines, and rotational molding machines. Each machine operates differently and is suited for specific applications, such as creating plastic parts, bottles, or complex industrial components.
Key Points Explained:
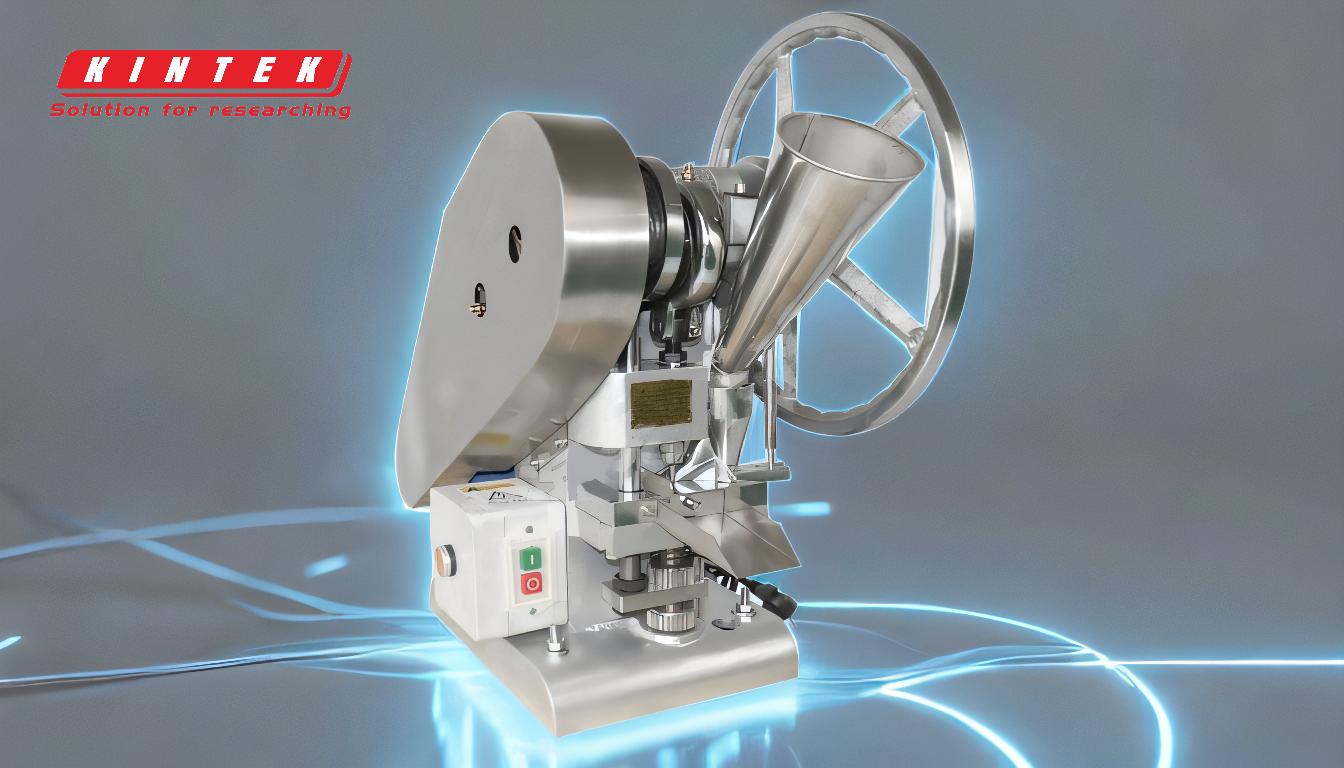
-
Injection Molding Machines:
- Function: These machines are primarily used for producing plastic parts by injecting molten plastic into a mold cavity.
- Process: Plastic pellets are heated until molten and then injected under high pressure into a mold. Once cooled, the mold opens, and the solidified part is ejected.
- Applications: Widely used in manufacturing items like automotive parts, toys, medical devices, and household goods.
- Key Features: High precision, repeatability, and ability to produce complex shapes.
-
Blow Molding Machines:
- Function: These machines are used to create hollow plastic products, such as bottles and containers.
- Process: A heated plastic tube (parison) is placed in a mold, and air is blown into it to expand the plastic against the mold walls.
- Applications: Commonly used in the production of bottles, fuel tanks, and other hollow items.
- Key Features: Suitable for high-volume production and lightweight products.
-
Compression Molding Machines:
- Function: These machines are used for molding materials like rubber, plastics, and composites by applying heat and pressure.
- Process: Material is placed in a heated mold cavity, and pressure is applied to shape it. The material cures or hardens under heat and pressure.
- Applications: Used for producing large, durable parts like automotive components, electrical insulators, and appliance parts.
- Key Features: Ideal for materials that are difficult to process with other methods, such as thermosetting plastics.
-
Rotational Molding Machines:
- Function: These machines are used to create large, hollow plastic products.
- Process: Plastic powder is placed in a mold, which is then rotated and heated. The powder melts and coats the interior of the mold, forming the desired shape as it cools.
- Applications: Used for making items like storage tanks, playground equipment, and kayaks.
- Key Features: Suitable for producing large, seamless, and stress-free parts.
-
Other Molding Machines:
- Transfer Molding Machines: Used for molding thermosetting materials, where the material is first heated and then transferred into the mold.
- Extrusion Molding Machines: Used to create continuous shapes like pipes, tubes, and sheets by forcing material through a die.
- Vacuum Forming Machines: Used to shape thermoplastic sheets by heating them and using vacuum pressure to form them over a mold.
Each type of molding machine has its unique advantages and is selected based on the material, product design, and production requirements. Understanding the specific needs of your project will help you choose the right machine for molding.
Summary Table:
Machine Type | Function | Applications | Key Features |
---|---|---|---|
Injection Molding Machines | Produces plastic parts by injecting molten plastic into a mold cavity. | Automotive parts, toys, medical devices, household goods. | High precision, repeatability, complex shapes. |
Blow Molding Machines | Creates hollow plastic products like bottles and containers. | Bottles, fuel tanks, hollow items. | High-volume production, lightweight products. |
Compression Molding Machines | Molds rubber, plastics, and composites using heat and pressure. | Automotive components, electrical insulators, appliance parts. | Ideal for thermosetting plastics, durable parts. |
Rotational Molding Machines | Produces large, hollow plastic products by rotating heated molds. | Storage tanks, playground equipment, kayaks. | Seamless, stress-free parts, suitable for large items. |
Transfer Molding Machines | Molds thermosetting materials by transferring heated material into a mold. | Electrical components, rubber parts. | Suitable for thermosetting materials, precise molding. |
Extrusion Molding Machines | Creates continuous shapes like pipes, tubes, and sheets. | Pipes, tubes, sheets. | Continuous production, versatile material processing. |
Vacuum Forming Machines | Shapes thermoplastic sheets using vacuum pressure over a mold. | Packaging, automotive interiors, signage. | Cost-effective for large, simple shapes. |
Need help choosing the right molding machine for your project? Contact our experts today!