Brazing is a versatile joining process that involves melting a filler metal to bond two or more base materials without melting the base materials themselves. The choice of materials for brazing depends on the base materials being joined, the desired properties of the joint, and the specific brazing method used. Common filler metals include aluminium-silicon alloys, copper, copper-silver, copper-zinc (brass), copper-tin (bronze), gold-silver-nickel alloys, and silver. Additionally, amorphous brazing foils made of nickel, iron, copper, silicon, boron, and phosphorus are also used. The selection of materials is crucial to ensure strong, durable, and reliable joints in various applications.
Key Points Explained:
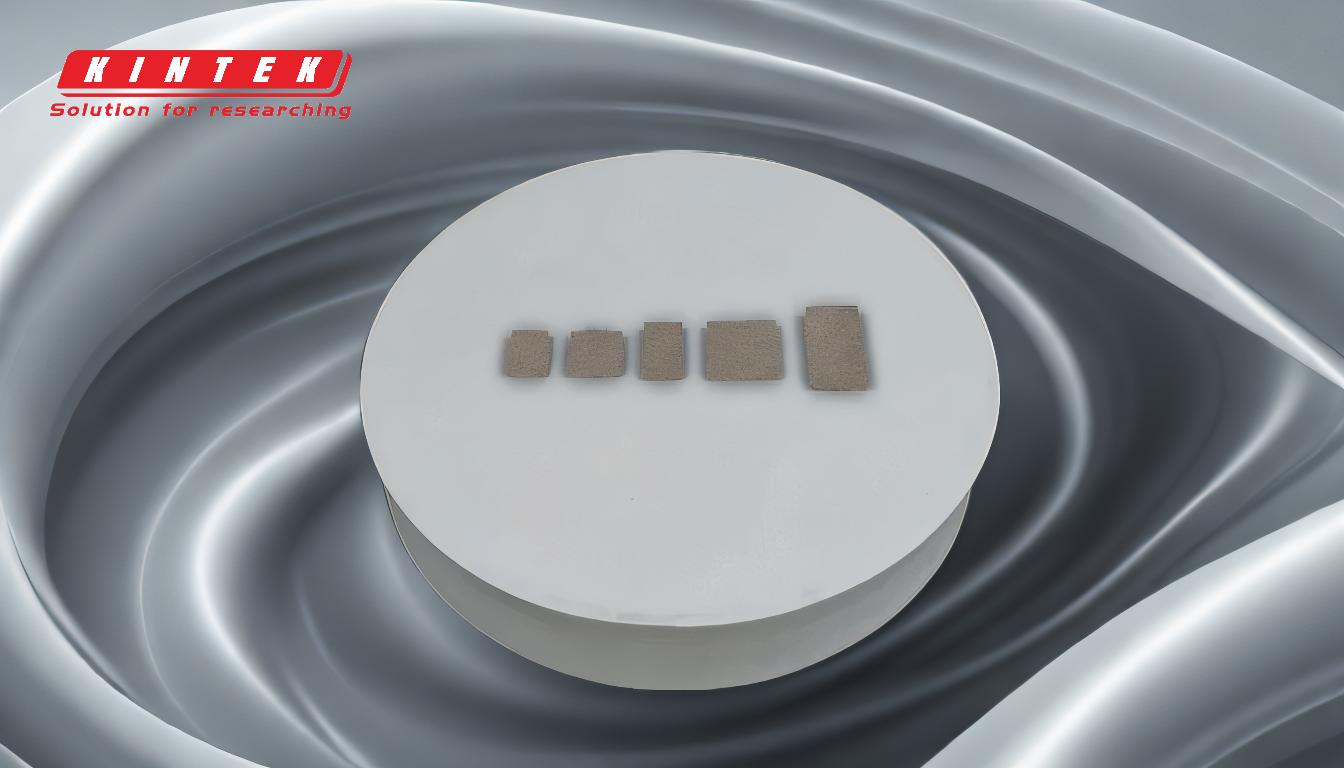
-
Base Materials for Brazing:
- The base materials being joined play a significant role in determining the appropriate filler metal and brazing method. Common base materials include metals like steel, stainless steel, aluminium, copper, and titanium, as well as ceramics and certain composites.
- The compatibility between the base material and the filler metal is essential to ensure proper wetting, bonding, and joint strength.
-
Filler Metals:
- Aluminium-Silicon Alloys: These are commonly used for brazing aluminium and its alloys. The silicon content helps lower the melting point of the filler metal, making it suitable for joining aluminium without melting the base material.
- Copper and Copper Alloys: Copper is widely used for brazing steel and other metals due to its excellent thermal and electrical conductivity. Copper-silver alloys are particularly useful for joining stainless steel and other high-temperature alloys.
- Copper-Zinc (Brass) and Copper-Tin (Bronze): These alloys are often used for brazing steel, cast iron, and other ferrous metals. They provide good strength and corrosion resistance.
- Gold-Silver-Nickel Alloys: These are used for high-reliability applications, such as in the aerospace and electronics industries, where strong, corrosion-resistant joints are required.
- Silver-Based Filler Metals: Silver is a popular choice for brazing a wide range of materials, including stainless steel, copper, and nickel alloys. It offers excellent flow characteristics and joint strength.
- Amorphous Brazing Foils: These foils, made of nickel, iron, copper, silicon, boron, and phosphorus, are used in specialized applications where precise control of the brazing process is required. They are particularly useful in vacuum brazing and other high-precision joining processes.
-
Brazing Methods:
- Torch Brazing: This method uses a gas flame to heat the joint and melt the filler metal. It is suitable for small-scale or repair work.
- Furnace Brazing: This method involves heating the parts in a controlled atmosphere (such as exothermic, hydrogen, argon, or vacuum) to prevent oxidation and ensure a clean joint. It is ideal for mass production and complex assemblies.
- Induction Brazing: This method uses electromagnetic induction to heat the joint and melt the filler metal. It is fast and efficient, making it suitable for high-volume production.
- Dip Brazing: In this method, the parts are immersed in a molten salt or metal bath to heat the joint and melt the filler metal. It is commonly used for joining aluminium and other non-ferrous metals.
- Resistance Brazing: This method uses electrical resistance to generate heat at the joint. It is suitable for joining small, delicate parts.
- Infrared Brazing: This method uses infrared radiation to heat the joint and melt the filler metal. It is suitable for joining materials with low thermal conductivity.
- Blanket Brazing: This method uses a flexible heating blanket to heat the joint. It is suitable for large or irregularly shaped parts.
- Electron Beam and Laser Brazing: These advanced methods use focused electron beams or laser beams to heat the joint and melt the filler metal. They are used in high-precision applications, such as in the aerospace and electronics industries.
-
Preventing Distortion in Brazing:
- Stress Relieving: Parts can be stress-relieved by heating them for extended periods before brazing to reduce internal stresses that could cause distortion during the brazing process.
- Rigid Fixtures: Using rigid fixtures to hold parts in place during brazing can help prevent movement and distortion.
- Heavier and Larger Parts: Designing parts to be heavier and larger can increase their resistance to distortion during brazing. However, distortion may still occur despite these measures.
-
High-Temperature Brazing Materials:
- Graphite, Molybdenum, and Tungsten: These materials are commonly used in high-temperature brazing processes, such as hardening, sintering, and brazing of nickel or copper alloys. They can withstand the high temperatures required for these processes without degrading.
In conclusion, the materials used in brazing are diverse and depend on the specific requirements of the application. The choice of filler metal, base material, and brazing method must be carefully considered to achieve strong, durable, and reliable joints.
Summary Table:
Category | Details |
---|---|
Base Materials | Steel, stainless steel, aluminium, copper, titanium, ceramics, composites |
Filler Metals | Aluminium-silicon alloys, copper, copper-silver, brass, bronze, gold-silver-nickel, silver |
Brazing Methods | Torch, furnace, induction, dip, resistance, infrared, blanket, electron beam, laser brazing |
High-Temperature | Graphite, molybdenum, tungsten |
Preventing Distortion | Stress relieving, rigid fixtures, heavier/larger parts |
Need help selecting the right brazing materials for your project? Contact our experts today!