Brazing is a versatile joining process that can be used to bond a wide variety of metals and alloys. It involves melting a filler metal with a lower melting point than the base metals being joined, which then flows into the joint by capillary action and solidifies to form a strong bond. The process is suitable for joining dissimilar metals, as well as metals with different thicknesses and complex geometries. Common metals that can be joined by brazing include steel, stainless steel, copper, brass, aluminum, nickel alloys, and titanium. The choice of filler metal and brazing technique depends on the specific properties of the base metals and the intended application.
Key Points Explained:
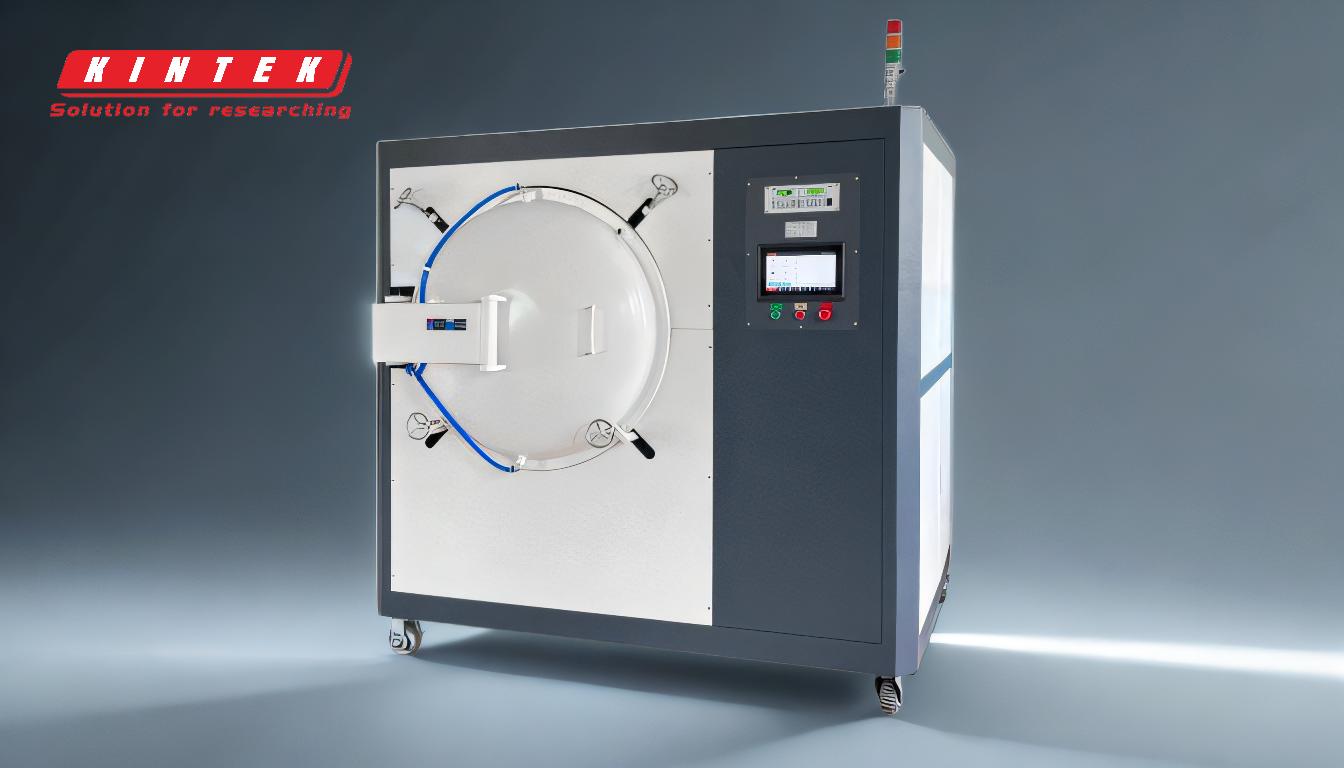
-
Steel and Stainless Steel:
- Brazing is commonly used to join carbon steel, low-alloy steel, and stainless steel. These materials are widely used in industries such as automotive, aerospace, and construction.
- For stainless steel, the filler metal must be carefully selected to avoid issues like carbide precipitation, which can reduce corrosion resistance. Nickel-based filler metals are often used for high-temperature applications.
-
Copper and Brass:
- Copper and its alloys, such as brass and bronze, are frequently brazed due to their excellent thermal and electrical conductivity. These materials are commonly used in plumbing, electrical components, and heat exchangers.
- Silver-based filler metals are often used for brazing copper and brass because they provide strong, leak-proof joints with good corrosion resistance.
-
Aluminum and Aluminum Alloys:
- Aluminum can be challenging to braze due to its oxide layer, which must be removed or controlled during the brazing process. However, with proper techniques, aluminum and its alloys can be successfully joined.
- Aluminum-silicon filler metals are commonly used for brazing aluminum, as they have a lower melting point and good wetting properties.
-
Nickel and Nickel Alloys:
- Nickel and its alloys, such as Inconel and Monel, are often brazed for high-temperature and corrosive environments, such as in gas turbines and chemical processing equipment.
- Nickel-based filler metals are typically used for brazing nickel alloys, as they provide excellent strength and corrosion resistance at elevated temperatures.
-
Titanium and Titanium Alloys:
- Titanium is a lightweight, strong, and corrosion-resistant metal that is often used in aerospace and medical applications. Brazing titanium requires careful control of the atmosphere to prevent oxidation.
- Silver-based and titanium-based filler metals are commonly used for brazing titanium, depending on the application requirements.
-
Dissimilar Metals:
- One of the key advantages of brazing is its ability to join dissimilar metals, such as copper to steel or aluminum to stainless steel. This is particularly useful in applications where different materials are required for their specific properties.
- The choice of filler metal is critical when joining dissimilar metals to ensure compatibility and a strong bond.
-
Complex Geometries and Thin Sections:
- Brazing is well-suited for joining components with complex shapes or thin sections, as the process does not require high pressure or extensive heating. This makes it ideal for applications in electronics, jewelry, and precision engineering.
- The capillary action of the filler metal allows it to flow into tight spaces, creating strong, uniform joints.
-
Applications and Industries:
- Brazing is used in a wide range of industries, including automotive, aerospace, HVAC, electronics, and medical devices. Each industry has specific requirements for the materials and filler metals used in brazing.
- For example, in the automotive industry, brazing is used to join components in radiators and heat exchangers, while in the medical industry, it is used to create biocompatible joints in surgical instruments.
In summary, brazing is a highly adaptable joining process that can be used to bond a wide variety of metals and alloys, including steel, stainless steel, copper, brass, aluminum, nickel alloys, and titanium. The choice of filler metal and brazing technique depends on the specific properties of the base metals and the intended application. Brazing is particularly advantageous for joining dissimilar metals, complex geometries, and thin sections, making it a valuable process across numerous industries.
Summary Table:
Metal/Alloy | Key Applications | Common Filler Metals |
---|---|---|
Steel & Stainless Steel | Automotive, aerospace, construction | Nickel-based |
Copper & Brass | Plumbing, electrical components, heat exchangers | Silver-based |
Aluminum & Alloys | Aerospace, electronics | Aluminum-silicon |
Nickel & Alloys | Gas turbines, chemical processing | Nickel-based |
Titanium & Alloys | Aerospace, medical devices | Silver-based, titanium-based |
Dissimilar Metals | Applications requiring unique material properties | Depends on metal compatibility |
Need help selecting the right brazing solution for your metals? Contact our experts today!